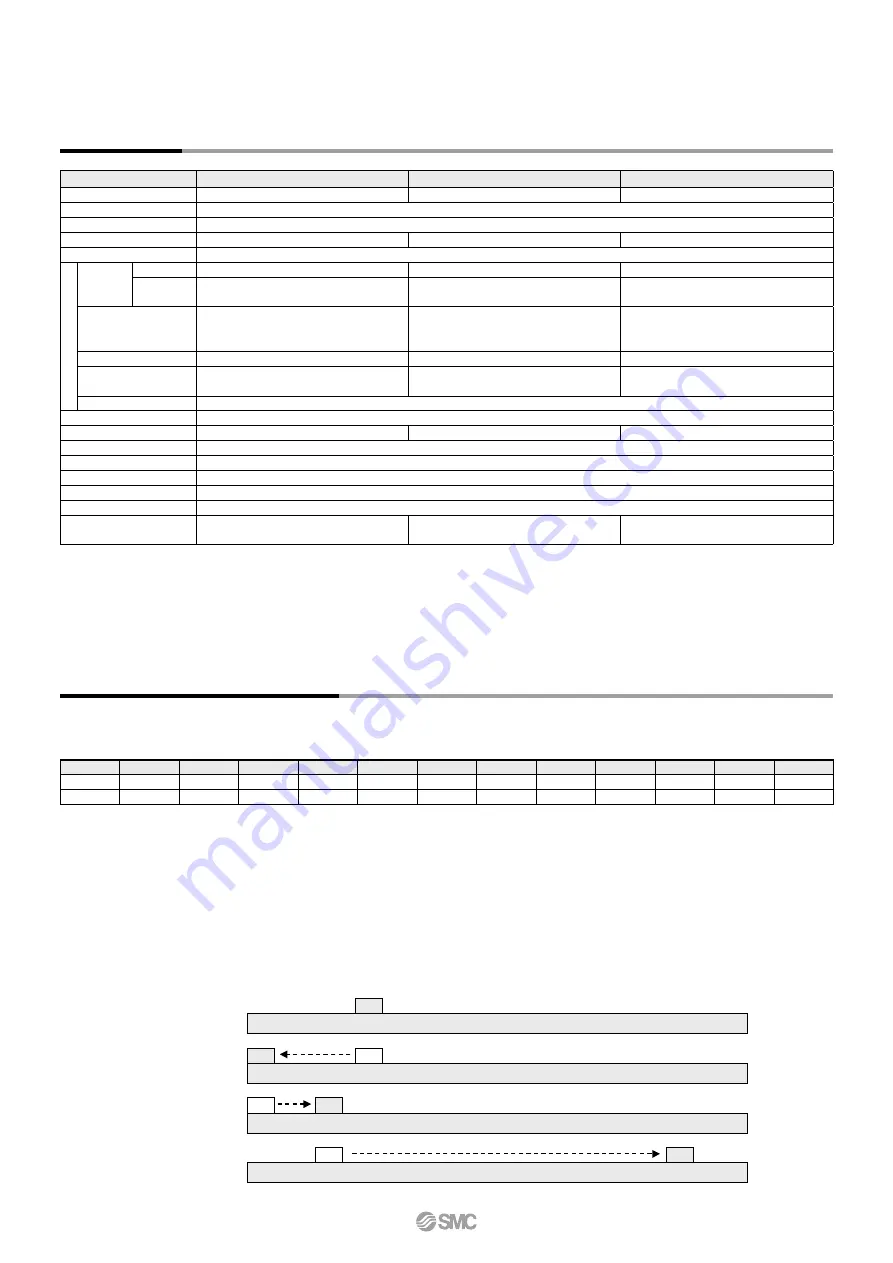
*
Numerical values other than “Moving force,” “Area 1,” and “Area 2” can be used to perform operation under numerical instructions from JXCL1.
Specifications
Model
JXCEH
JXC9H
JXCPH
Network
EtherCAT
EtherNet/IP™
PROFINET
Compatible motor
Step motor (Servo/24 VDC)
Power supply
Power voltage: 24 VDC
±
10%
Current consumption (Controller)
200 mA or less
200 mA or less
200 mA or less
Compatible encoder
Battery-less absolute
Communication specifications
Applicable
system
Protocol
EtherCAT
*
2
EtherNet/IP™
*
2
PROFINET
*
2
Version
*
1
Conformance Test
Record V.1.2.6
Volume 1 (Edition 3.14)
Volume 2 (Edition 1.15)
Specification
Version 2.32
Communication
speed
100 Mbps
*
2
10/100 Mbps
*
2
(Automatic negotiation)
100 Mbps
*
2
Configuration file
*
3
ESI file
EDS file
GSDML file
I/O occupation area
Input 20 bytes
Output 36 bytes
Input 36 bytes
Output 36 bytes
Input 36 bytes
Output 36 bytes
Terminating resistor
Not included
Memory
EEPROM
LED indicator
PWR, RUN, ALM, ERR
PWR, ALM, MS, NS
PWR, ALM, SF, BF
Cable length [m]
Actuator cable: 20 or less
Cooling system
Natural air cooling
Operating temperature range [
°
C]
0 to 40 (No freezing)
*
4
Operating humidity range [%RH]
90 or less (No condensation)
Insulation resistance [M
W
]
Between all external terminals and the case: 50 (500 VDC)
Weight [g]
260 (Screw mounting)
280 (DIN rail mounting)
250 (Screw mounting)
270 (DIN rail mounting)
260 (Screw mounting)
280 (DIN rail mounting)
*
1 Please note that versions are subject to change.
*
2 Use a shielded communication cable with CAT5 or higher for the PROFINET, EtherNet/IP™, and EtherCAT.
*
3 The files can be downloaded from the SMC website.
*
4 The operating temperature range for both controller version 1 products and controller version 2 products is 0 to 40
°
C.
M
Trademark
EtherNet/IP
®
is a registered trademark of ODVA, Inc.
EtherCAT
®
is registered trademark and patented technology, licensed by Beckhoff Automation GmbH, Germany.
Example of Operation Command
In addition to the step data input of 64 points max. in each communication protocol, the changing of each parameter can be performed in real time via numerical data defined operation.
<Application example> Movement between 2 points
No.
Movement mode
Speed
Position Acceleration Deceleration Pushing force Trigger LV Pushing speed Moving force
Area 1
Area 2
In position
0
1: Absolute
100
10
3000
3000
0
0
0
100
0
0
0.50
1
1: Absolute
100
100
3000
3000
0
0
0
100
0
0
0.50
<Step no. defined operation>
Sequence 1: Servo ON instruction
Sequence 2: Instruction to return to origin
Sequence 3: Specify step data No. 0 to input the DRIVE signal.
Sequence 4: Specify step data No. 1 after the DRIVE signal has been temporarily turned OFF to input the DRIVE signal.
<Numerical data defined operation>
Sequence 1: Servo ON instruction
Sequence 2: Instruction to return to origin
Sequence 3: Specify step data No. 0 and turn ON the input instruction flag (position). Input 10 in the target position. Subsequently the start flag turns ON.
Sequence 4: Turn ON step data No. 0 and the input instruction flag (position) to change the target position to 100 while the start flag is ON.
The same operation can be performed with any operation command.
0
10
100
Sequence 1
Sequence 2
Sequence 3
Sequence 4
37
JXCEH/9H/PH
Series