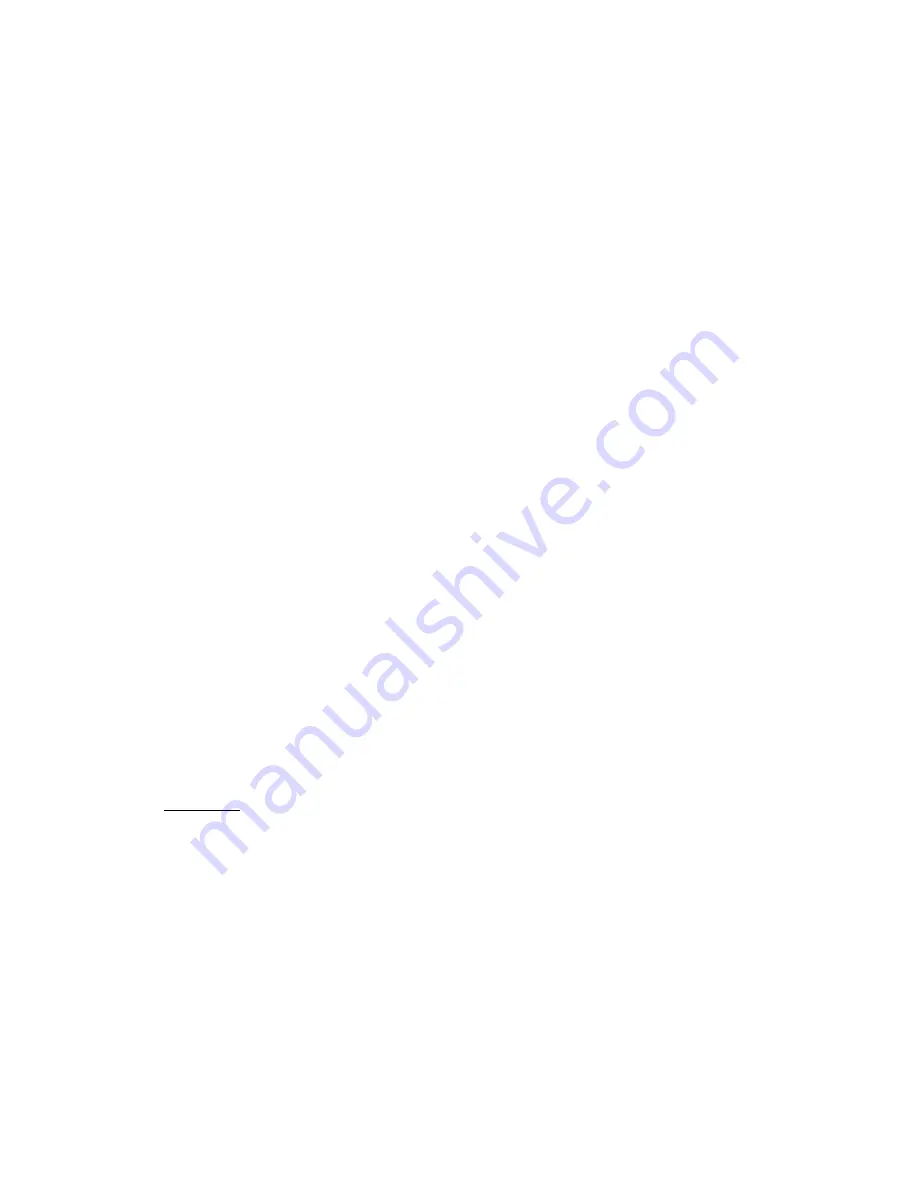
NOTICE SM CRIMP 2000-V8.0 / Mai 2012
37
9.1
Punch guide centring problem
Check that:
The upper cassette, lower-clincher holder, contact surfaces
both on machine side and
on tool side have not been deformed by shock during a disassembly, and have no
burrs on any angle.
The contact surfaces of the tool cassette and the lower-die holder are not
contaminated by splice residues.
The clincher holder is positioned properly and firmly tightened.
The wires at the rear side of the cassette are correctly positioned inside the grooves.
The cutter block is correctly positioned. During a dismantling of the cassette,
someone forgot to press it out of the cassette before the re-fixing of the cassette
cover.
The stop-splice sensor is not correctly adjusted (see Chapter 5.7)
The punch is worn or broken (see Chapter 9.3).
If all the above points are satisfactory, re-adjust the clincher centring. This re-
adjustment is likely to be necessary after 1000 crimps, in particular if the cassette has
been dismantled. (See Section 5.8).
9.2
Punch guide colliding or too far from the top of the clincher
If the two parts are too far from each other at the lower dead centring position, the
splice may not correctly formed, may break, or one side of the splice will be formed
in the wrong direction.
Conversely, in no event should these parts collide.
The clearance between punch guide and clincher top must be approximately 0,01
–
0,1 mm maximum at B.D.C. (Bottom Dead Centre).
If an adjustment is necessary:
Procedure:
Disconnect the power cable.
Remove the Crimp Banding.
Remove safety cover on the left-hand side.
Rotate hand wheel until the guide lever is located in its furthest most bottom
position.
Adjust clearance between guide and clincher by lightly turning the Allen screw below
the guide lever in or out. (Allen key of 2.5 mm). Adjust at 0.1 mm ( make this
adjustment with the cassette and clincher mounted).