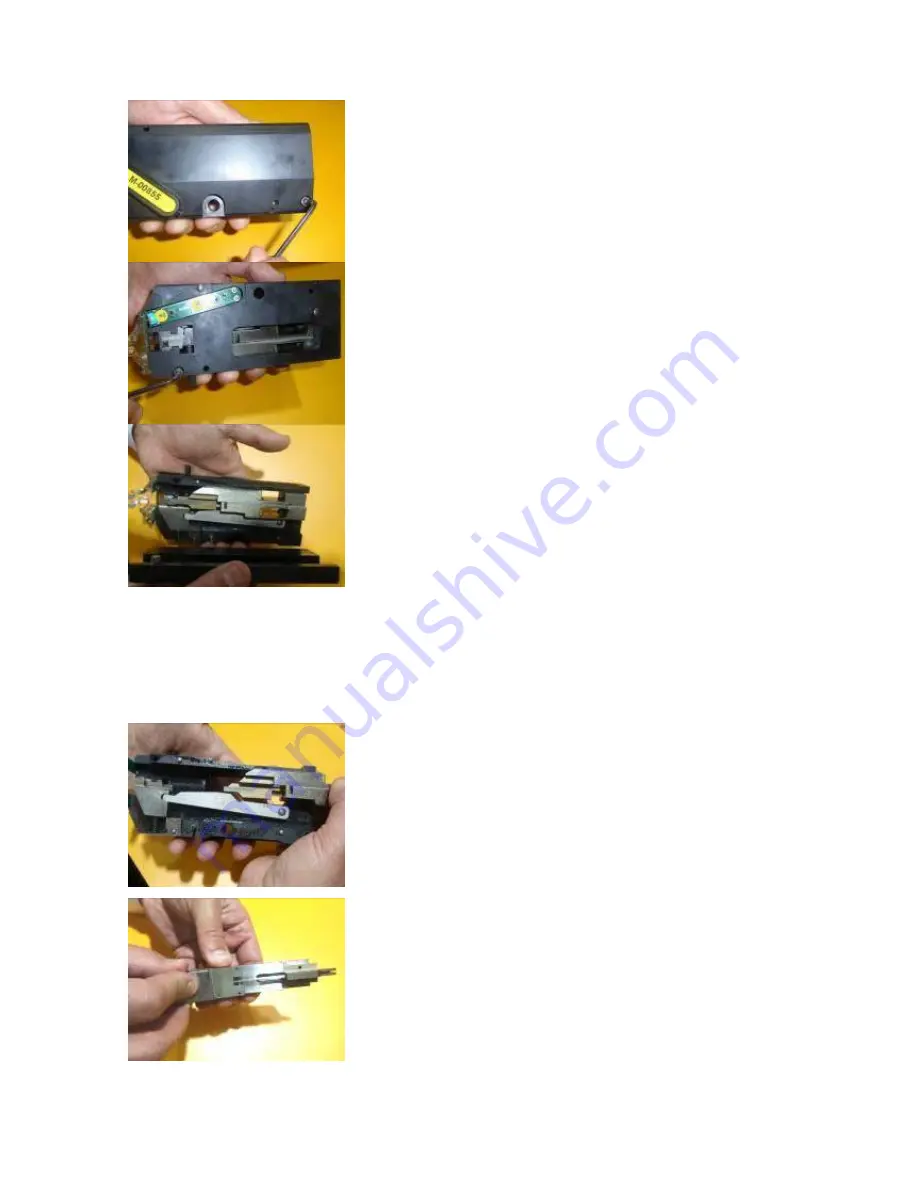
NOTICE SM CRIMP 2000-V8.0 / Mai 2012
17
Remove the front screw on the cover of the
tooling.
Remove the screw located on the rear of the
tooling.
Slowly open the cover of the tooling.
Place all of the components on a clean surface.
5.2
Replacing the punch and/or the guide
To dismantle the tooling, refer to chapter 5.1
Holding the tooling in your left hand, you must
now check that the sliders can easily slide up and
down simultaneity.
Do not turn the tooling; avoid any damage on
cutting-block and anvil.
Separate the punch slider from the punch-guide
slider by rotating the punch slider as shown on
the picture.
Ensure that the punch pin does not fall on the
floor.