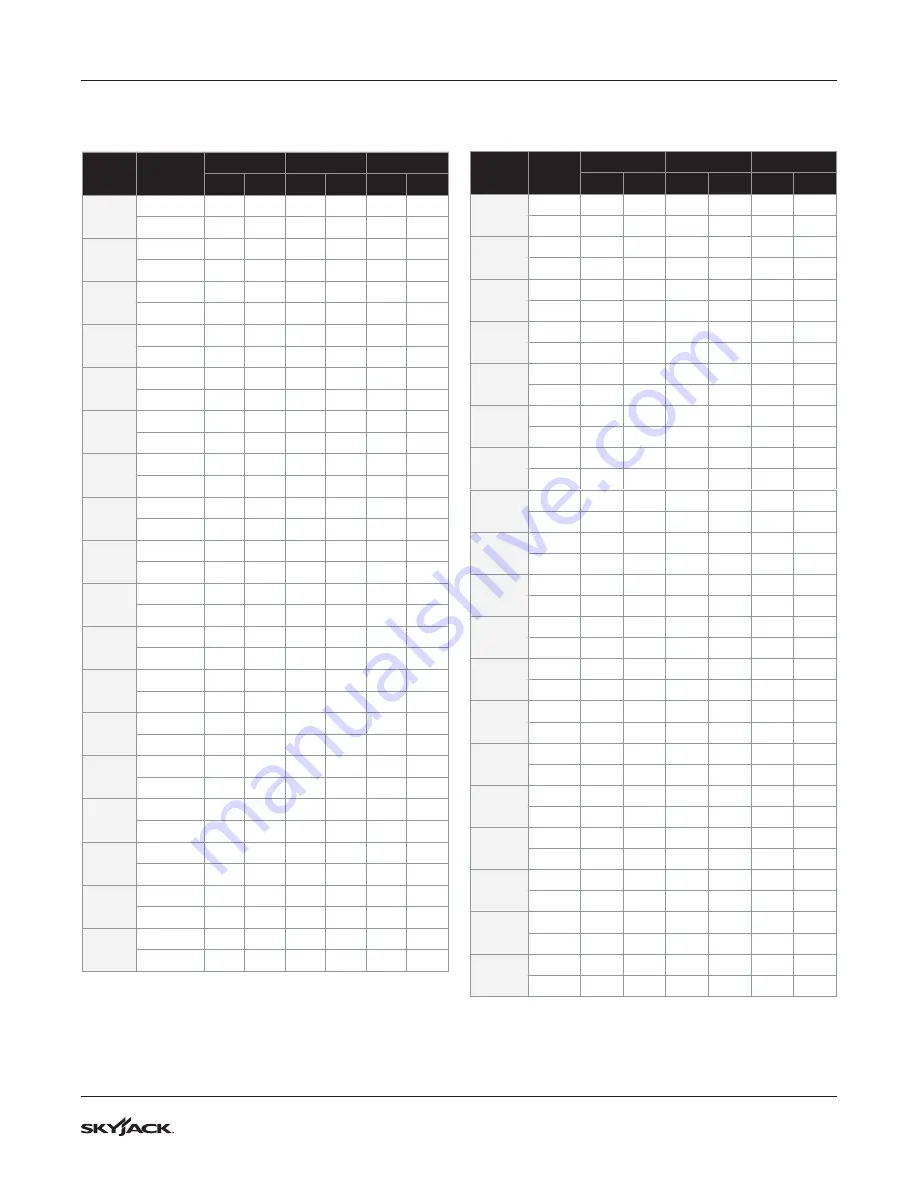
33
SJ6826RT, SJ6832RT
213560ABA
2.2
Torque Specifications for Fasteners (US Imperial)
Table
Size
Torque
Type
SAE2
SAE 5
SAE 8
Dry
Lubed
Dry
Lubed
Dry
Lubed
4-40
(in-lb)
(5)
(4)
(8)
(6)
(12)
(9)
Nm
0.6
0.5
0.9
0.7
1.4
1.0
4-48
(in-lb)
(6)
(5)
(9)
(7)
(13)
(10)
Nm
0.7
0.6
1.0
0.8
1.5
1.1
6-32
(in-lb)
(10)
(8)
(16)
(12)
(23)
(17)
Nm
1.1
0.9
1.8
1.4
2.6
1.9
6-40
(in-lb)
(12)
(9)
(18)
(13)
(25)
(19)
Nm
1.4
1.0
2.0
1.5
2.8
2.1
8-32
(in-lb)
(19)
(14)
(30)
(22)
(41)
(31)
Nm
2.1
1.6
3.4
2.5
4.6
3.5
8-36
(in-lb)
(20)
(15)
(31)
(23)
(43)
(32)
Nm
2.3
1.7
3.5
2.6
4.9
3.6
10-24
(in-lb)
(27)
(21)
(43)
(32)
(60)
(45)
Nm
3.1
2.4
4.9
3.6
6.8
5.1
10-32
(in-lb)
(31)
(23)
(49)
(36)
(68)
(51)
Nm
3.5
2.6
5.5
4.1
7.7
5.8
1/4-20
(in-lb) ft-lb
(66)
(50)
8
(75)
12
9
Nm
7.5
5.6
11
8.5
16
12
1/4-28
(in-lb) ft-lb
(76)
(56)
10
(86)
14
10
Nm
8.6
6.3
14
9.7
19
14
5/16-18
ft-lb
11
8
17
13
25
18
Nm
15
11
23
18
34
24
5/16-24
ft-lb
12
9
19
14
25
20
Nm
16
12
26
19
34
27
3/8-16
ft-lb
20
15
30
23
45
35
Nm
27
20
41
31
61
47
3/8-24
ft-lb
23
17
35
25
50
35
Nm
31
23
47
34
68
47
7/16-14
ft-lb
32
24
50
35
70
55
Nm
43
33
68
47
95
75
7/16-20
ft-lb
36
27
55
40
80
60
Nm
49
37
75
54
108
81
1/2-13
ft-lb
50
35
75
55
110
80
Nm
68
47
102
75
149
108
1/2-20
ft-lb
55
40
90
65
120
90
Nm
75
54
122
88
163
122
NOTE:
Lubed includes lubricants such as lubrizing, oil, grease, or uncured Loctite .
1374AA
Size
Torque
Type
SAE2
SAE 5
SAE 8
Dry
Lubed
Dry
Lubed
Dry
Lubed
9/16-12
ft-lb
70
55
110
80
150
110
Nm
95
75
149
108
203
149
9/16-18
ft-lb
80
60
120
90
170
130
Nm
108
81
163
122
230
176
5/8-11
ft-lb
100
75
150
110
220
170
Nm
136
102
203
149
298
230
5/8-18
ft-lb
110
85
180
130
240
180
Nm
149
115
244
176
325
244
3/4-10
ft-lb
175
130
260
200
380
280
Nm
237
176
353
271
515
380
3/4-16
ft-lb
200
150
300
220
420
320
Nm
271
203
407
298
569
434
7/8-9
ft-lb
170
125
430
320
600
460
Nm
230
169
583
434
813
624
7/8-14
ft-lb
180
140
470
360
660
500
Nm
244
190
637
488
895
678
1-8
ft-lb
250
190
640
480
900
680
Nm
339
258
868
651
1220
922
1-12
ft-lb
270
210
710
530
1000
740
Nm
366
285
963
719
1356
1003
1-14
ft-lb
280
210
730
540
1020
760
Nm
380
285
990
732
1383
1030
1 1/8-7
ft-lb
350
270
800
600
1280
960
Nm
475
366
1085
813
1735
1302
1 1/8-12
ft-lb
400
300
880
660
1440
1080
Nm
542
407
1193
895
1952
1464
1 1/4-7
ft-lb
500
380
1120
840
1820
1360
Nm
678
515
1519
1139
2468
1844
1 1/4-12
ft-lb
550
420
1240
920
2000
1500
Nm
746
569
1681
1247
2712
2034
1 3/8-6
ft-lb
670
490
1460
1100
2380
1780
Nm
908
664
1979
1491
3227
2413
1 3/8-12
ft-lb
750
560
1680
1260
2720
2040
Nm
1017
759
2278
1708
3688
2766
1 1/2-6
ft-lb
870
650
1940
1460
3160
2360
Nm
1180
881
2630
1979
4284
3200
1 1/2-12
ft-lb
980
730
2200
1640
3560
2660
Nm
1329
990
2983
2224
4827
3606
To
order
go
to
Discount-Equipment.com