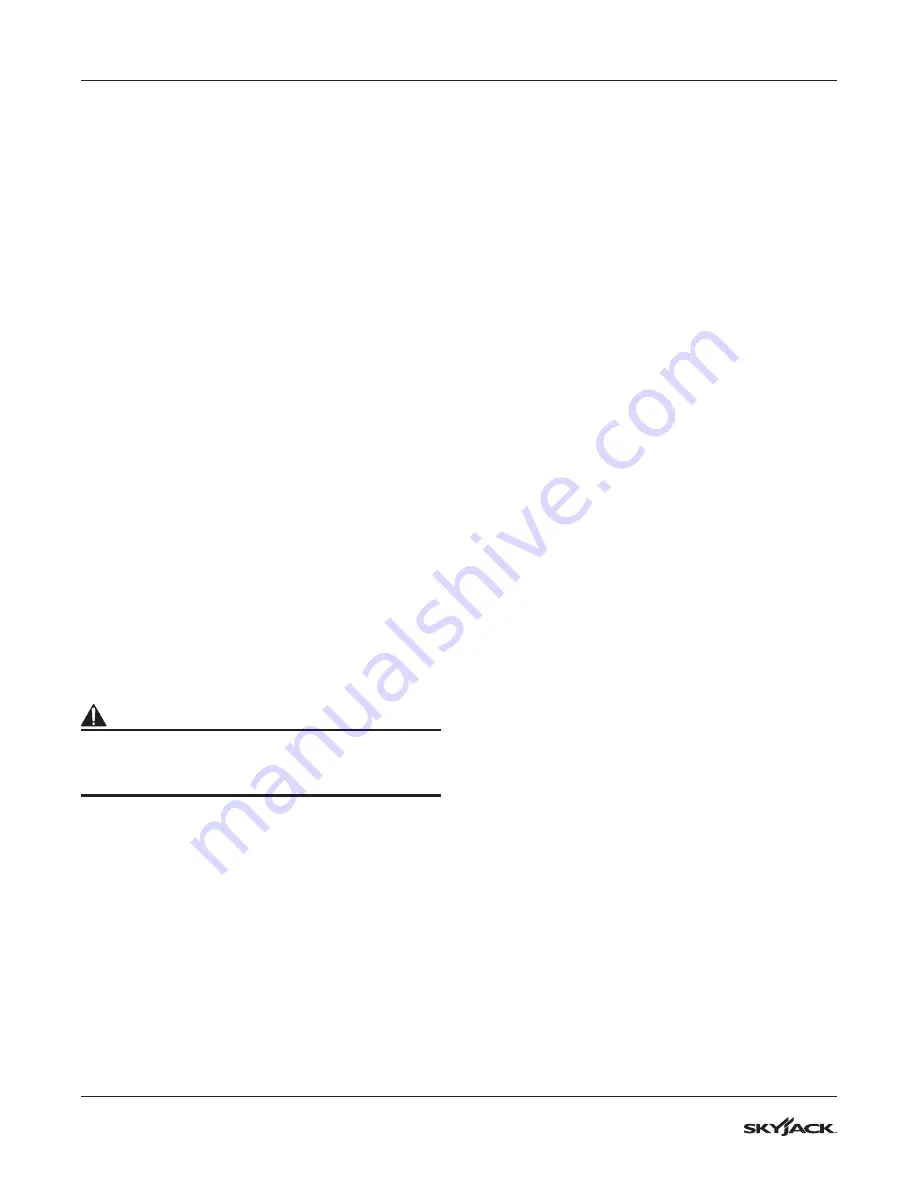
12
SJ6826RT, SJ6832RT
213560ABA
Section 1 – Scheduled Maintenance
Maintenance and Inspection Schedule
1.2 Maintenance and
Inspection Schedule
The actual operating environment of the work platform
governs the use of the maintenance schedule. The
inspection points covered in
1 .4 Frequent/Periodic/
Annual/Pre-Delivery Inspection Checklist
, indicates the
areas of the MEWP to be maintained or inspected and
at what intervals the maintenance and inspections are
to be performed.
1.2-1 Owner’s Annual Inspection Record
It is the responsibility of the owner to arrange
quarterly and annual inspections of the MEWP. (
1 .3
Owner’s Annual Inspection Record
)
. Owner’s Annual
lnspection Record is to be used for recording the
date of the inspection, owner’s name, and the person
responsible for the inspection of the work platform.
1.2-2 Replacement Parts
Use only original replacement parts. Parts such
as batteries, wheels, railings, etc. with weight and
dimensions different from original parts will affect
stability of the MEWP and must not be used without
manufacturer’s consent.
All replacement tires must be of the same size and
load rating as originally supplied tires; to maintain
safety and stability of MEWP.
Consult SKYJACK’s Service Department for optional
tires specifications and installation.
WARNING
Any unit that is damaged or not operating properly
must be immediately tagged and removed from
service until proper repairs are completed.
1.2-3 Maintenance and Service Safety
Tips
Maintenance and repair should only be performed by
personnel who are trained and qualified to service this
MEWP.
All maintenance and service procedures should be
performed in a well lighted and well ventilated area.
Anyone operating or servicing this MEWP must read
and completely understand all operating instructions
and safety hazards in this manual and operating
manual.
All tools, supports and lifting equipment to be used
must be of proper rated load and in good working
order before any service work begins. Work area
should be kept clean and free of debris to avoid
contaminating components while servicing.
Ensure personnel are clear from under unsupported
components/systems that are at risk of movement
during maintenance.
All service personnel must be familiar with employer
and governmental regulations that apply to servicing
this type of equipment.
Keep sparks and flames away from all flammable or
combustible materials.
Properly dispose of all waste material such as
lubricants, rags, and old parts according to the
relative law provisions obtaining in the country.
Before attempting any repair work, disconnect the
main power connectors.
Keep personnel clear of components, systems or
unsupported loads that may move unexpectedly
during maintenance procedures.
Preventive maintenance is the easiest and least
expensive type of maintenance.
To
order
go
to
Discount-Equipment.com