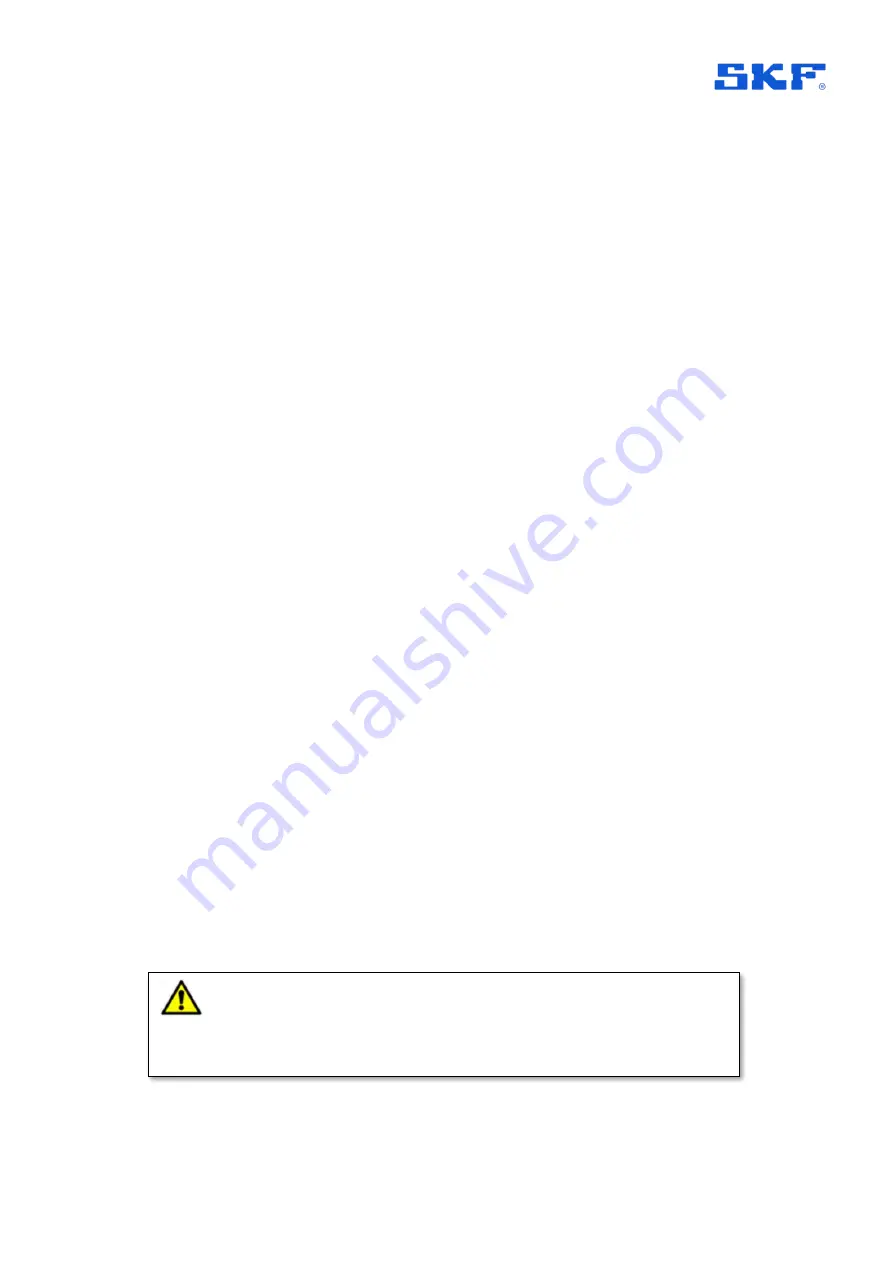
INSTALLATION AND OPERATING INSTRUCTIONS
SKF Multilog On-line System IMx-16Plus
SKF Multilog On-line System IMx-16Plus
User Manual
Revision Letter A
27 (66)
For testing, especially SAT testing, a 1 k
Ω resistor can replace the sensor to give a
known ‘temperature reading’ for the loop (
0
0
C). SKF supply one such SAT test
resistor, colour coded red, with each IMx-16Plus and 8-resistors with CMON 4135
(Set of double deck connectors and resistors for Modbus termination, 4-20mA inputs
and PT1000 inputs for IMx-8/IMx-16Plus).
2.5.11 Connecting tacho/speed signals (D1 to D4)
Connecting a tacho signal to the IMx-16Plus allows an assessment of rotational
speed of the monitored shaft and the operational state of the machine or train. Often
a multi-event target is used as this enables a faster update of speed, but if needed,
both vibration phase and speed data can be obtained by using a single event per rev
target.
The tacho sensor will normally be mounted to detect the changing presence of a
target. For example, a single event per rev target can often be arranged using either,
an existing: key or a key-way.
A sensor with suitable sensing range must be selected and gapped appropriately to
accommodate any movement between sensor and target, that might occur. The IMx-
16Plus supports two-wire, three-wire PNP and pulse sources*.
*The digital input and trigger characteristics are specified in
. Suitable pulse
sources include, for example, a TTL like signal (0 to 5 V, 50% duty cycle) or other
positive pulse sources up to 24 V. To ensure reliable triggering when using
sensor/target systems that tend to produce shorter duration pulses with slower rise
times, ensure that the pulse signal available at the IMx input comfortably crosses the
trigger threshold and aim for pulse heights of 12 to 24 V, where possible.
The digital input connectors are located on the top end cap of the IMx-16Plus (refer
).
For each tacho input, 3-terminals are available:
•
P
•
D
Digital signal in
•
G
Common or return connection
By design, the IMx-16Plus supplies power to all digital input channels (on P1 to P4).
Sensor power at P1 to P4 is always enabled and cannot be controlled or
configured by hardware or software. Trigger level and hysteresis are also fixed,
refer specifications,