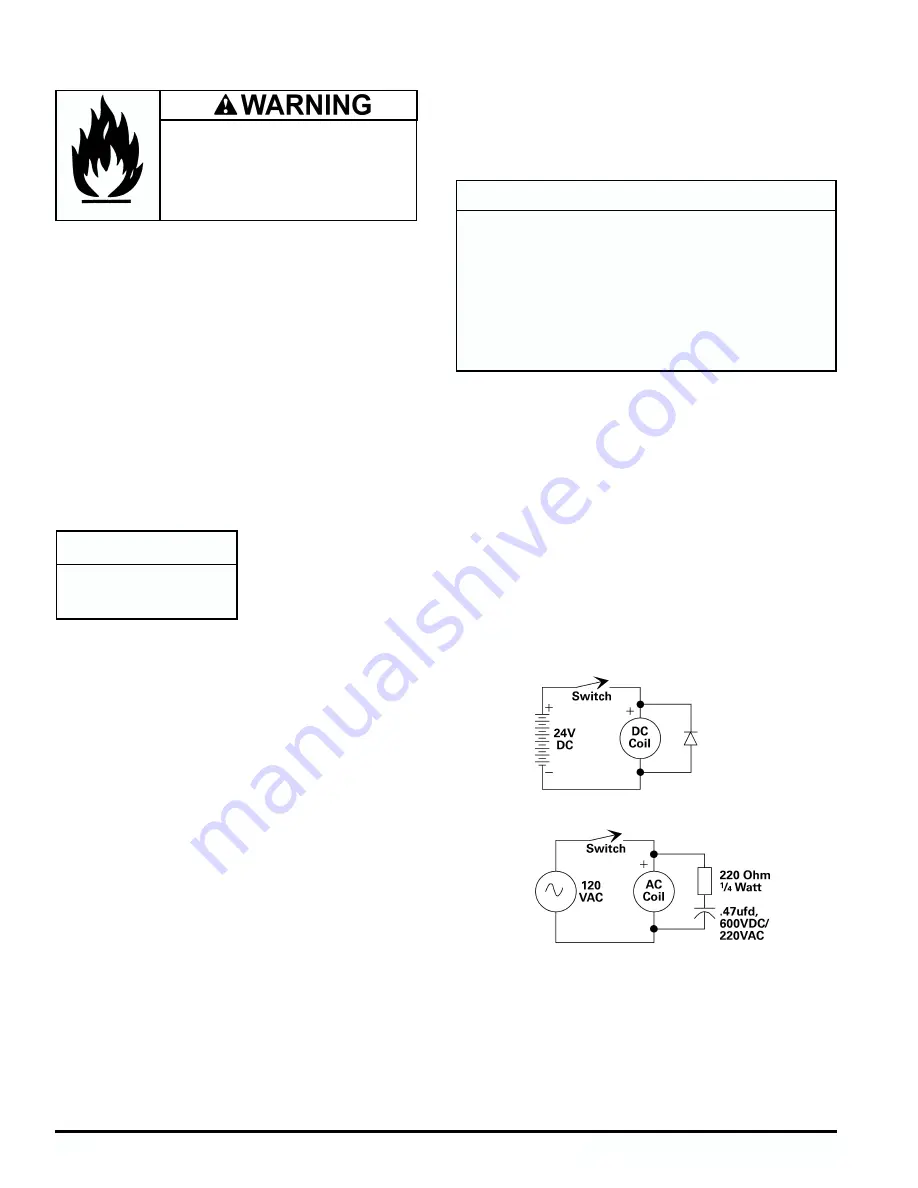
Siemens Energy & Automation, Inc.
14
4.4.1 Power and Motor Wiring
Power supply and motor wiring ampacity should be based on
the current ratings of the motor as specified on the nameplate
and in compliance with NEC and local codes. Power and motor
supply wiring should be routed in its own separate conduit or
wireway.
Each SIKOSTART controller is available in several power supply
voltage range models. Ensure that the supply voltage and fre-
quency are within the rated range of the controller.
When welding cable or other fine wire cables are used for
power wiring, use crimp type solderless terminals due to the
fine strand characteristic of this cable. Screw type compression
terminals are not recommended. The fine wires can jam the
threads of the terminal and prevent sufficient compression of
the wire strands. In addition, the fine wires can relax in the ter-
minal, which can lower the compression of the cable. If the con-
tact ends of the cable are not properly compressed, arcing can
occur with the risk of a fire.
4.4.2 Grounding
The controller enclosure and the motor frame must be properly
grounded in a manner that meets all applicable wiring codes. A
ground stud at the line and motor terminals on the controller
frame is provided for connecting the SIKOSTART controller to
system earth ground.
A complex system must have only one ground point to common
power supplies, signal returns, etc. to prevent ground loops. In
most cases a large grounded metal object, such as a control
cabinet, may be considered a single point. Using a short ground
wire to a cabinet is better than using a long ground wire to a ter-
minal barrier bussing point.
4.4.3 Control Wiring
The control wiring is connected at the logic board terminals
shown in figure 11.
Control Voltage.
Each SIKOSTART controller is available in sev-
eral control voltage models. Ensure that the control voltage and
frequency supplied match the controller model.
Wire Specifications.
Each control terminal can accept a maxi-
mum of two 14-AWG stranded wires. Be sure ring tongue ter-
minals are sized correctly for the wire.
Labeling.
Each wire should be appropriately labeled using
tape, shrink-tubing, or other dependable method.
Routing.
All control wiring must be kept separate from power
and motor wiring and run in its own separate conduit. Keep con-
trol wire bundles physically separated from power wiring by at
least 6 inches. Where control and power wiring must cross,
they should intersect at right angles.
4.4.4 Coil Suppression
Relay, electromechanical brake, or solenoid coils produce elec-
trical noise transients (especially when being de-energized)
which can be coupled into the controller circuitry and cause
erratic operation. For all such devices connected to or near the
controller or its wiring, see figure 9 and observe the following.
24V DC Coils.
Connect a diode directly across each DC coil. A
1N4004 diode is acceptable for most 24V DC applications up to
1.0A. A varistor or surge suppressor can also be used in place
of the diode.
120V AC Coils.
Use an R-C circuit (0.47 mfd, 600V capacitor in
series with a 1/4 watt 220 ohm resistor) across each 120V AC
coil. An appropriately rated varistor or surge suppressor can be
used in place of the R-C circuit, however, R-C circuits are rec-
ommended because they limit the rate of rise of noise and thus
help eliminate high frequency components.
CAUTION
Only use flexible connectors to
connect power wires to con-
troller busbar.
CAUTION
The control outputs are semiconductor (solid state) out-
puts. Applying improper control voltage and/or frequen-
cy can damage the control circuits.
Use control circuits only at the rated voltage and frequency. DC24V
models have solid state FET outputs and should not be used on AC
circuits. Alternately, AC120V & AC230V models have triac outputs
and should not be used on DC circuits.
For
technical data,
see the Low Voltage Control Catalog
NKS1999/2000, see the Instruction Manual or contact your nearest
Siemens Sales Office.
Figure 9
- Inductive Load Suppression
Fire hazard.
Can cause death, serious injury, or
equipment damage.
Welding cable requires crimp type solderless
terminals to prevent arcing and possible fire,
Содержание SIKOSTART 3RW34
Страница 15: ...Siemens Energy Automation Inc 15 Figure 10 SIKOSTART Power and Motor Connections ...
Страница 16: ...Siemens Energy Automation Inc 16 Figure 11 SIKOSTART Control Connections ...
Страница 42: ...Siemens Energy Automation Inc 42 Figure 27 for 3RW345 Figure 28 for 3RW346 Figure 29 Typical configurations ...