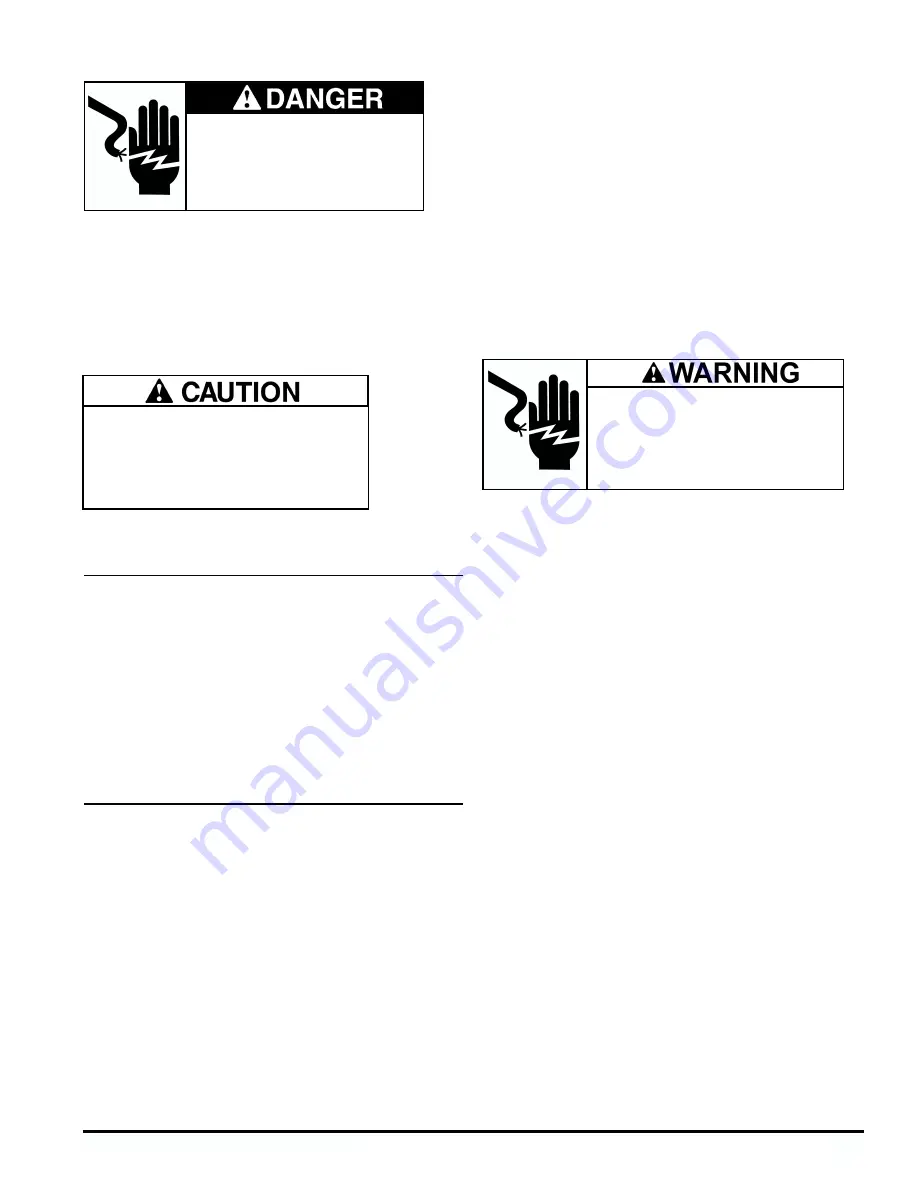
Siemens Energy & Automation, Inc.
17
4.5 Power and Motor Connections
The controller input terminals L1, L2 and L3, are at the top of
the unit and the output terminals T1, T2 and T3 are at the bot-
tom of the unit (figure 10). Observe the following:
1. Torque the power and motor terminal set screws according
to the wire size as indicated in table 3. Lug kits are listed in
Section 10, Spare and Optional parts, of this manual.
2. Torque the ground stud nut according to controller opera-
tional current as indicated in table 3.
Table 3
Terminal Screw and Ground Stud Nut Torque
Threaded
Torque
Item
lb-in. [N-m]
Terminal Screw
Wire Size (AWG or MCM)* mm
2
6 to 4 [13.3 - 27.27].....................................100 [11]
3 to 2 [? - 33.6]...........................................125 [14]
1 [42.41] .....................................................135 [15]
1/0 to 2/0 [53.51] ........................................150 [17]
3/0 to 4/0 [85.03 - 107.22] ..........................225 [25]
250 to 400 [126.68 - 202.68] .....................290 [33]
500 to 600 [253.35 - 300 ...........................335 [38]
Nut on Ground Stud
Controller Operational Current
<= 240A.........................................................75 [8]
>= 360A......................................................110 [12]
* for 75
v
C Aluminum or Copper Wire
4.5.1 Power Connections
1. Connect the proper capacity 3-phase 50/60 Hz voltage
source to the controller input terminals L1, L2, and L3. These
terminals are not phase sensitive.
The voltage source must be correct because:
a. Connecting the controller to a line voltage higher than its
rating will open the protective resistor in the snubber
board and prevent controller operation; repair will be
required before the controller can be put into operation.
b. Connecting the controller to a line voltage lower than its
rating will: 1) cause erratic controller operation resulting
in damage to the motor, or 2) prevent controller opera-
tion due to the low control voltage lockout protective fea-
ture.
2. Connect the ground terminal (labeled with ground symbol)
to earth ground.
4.5.2 Motor Connections
1. The NEC motor overload protection requirement can be met
with an optional overload relay.
2. The controller can be used for wye or delta motors with con-
nections to the motor as either In Line wiring or Inside Delta
wiring (paragraph 2.3.3). Be sure the power ratings are cor-
rect for the type of connection required for the application;
refer to section 3.
3. For a dual voltage 9-lead wye motor (represented in figures
12 and 13), the 3-lead controller-to-motor terminal connec-
tions are listed in Table 4.
Hazardous voltage.
Will cause death or serious injury.
To avoid electrical shock or burn, turn off
main and control voltages before perform-
ing installation or maintenance.
Wrong power rating may cause injury or
property damage.
Confirm that the correct HP rating for the controller
corresponds to the type of connections being
used; e.g. don’t use Inside Delta rating for a con-
troller wired In Line.
Hazardous voltage.
Can cause death, serious injury or
property damage.
The controller case must be grounded to
earth for operator’s safety.
Содержание SIKOSTART 3RW34
Страница 15: ...Siemens Energy Automation Inc 15 Figure 10 SIKOSTART Power and Motor Connections ...
Страница 16: ...Siemens Energy Automation Inc 16 Figure 11 SIKOSTART Control Connections ...
Страница 42: ...Siemens Energy Automation Inc 42 Figure 27 for 3RW345 Figure 28 for 3RW346 Figure 29 Typical configurations ...