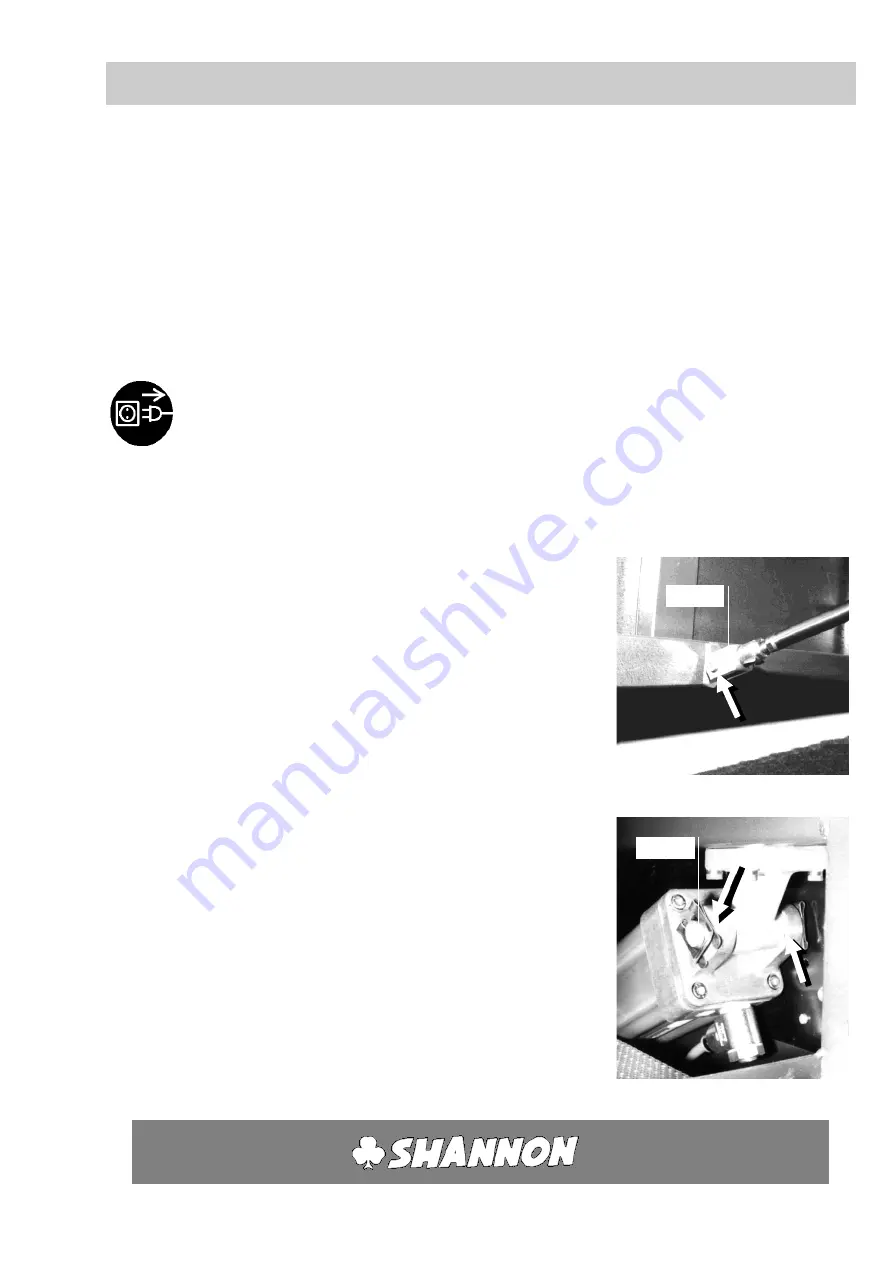
User’s guide
HRP/D
-
30
-
HS
Maintenance
The machine requires very little maintenance. Occasionally
remove loose dirt from the machine and brush it clean.
10.1
SAFETY MEASURES
1.
Switch off the main switch (switch
A
).
2.
Clear the working surface.
3.
Disconnect the compressed air..
4.
Remove the plug from the socket.
10.2
LUBRICATION POINTS
The following points should be lubricated with a drop of oil or
grease once a year:
10.2.1
Cylinder bearing: bottom.
To reach the lubrication point remove a frame plate on the rear
or side of the machine.
10.2.2
Cylinder bearing: top.
To reach the lubrication point remove the control units next to
the central support.
(See Section
12
.)
10
Bearing
Bearing
Содержание HRP/D
Страница 1: ...User s Guide English Plastic bending machine HRP D...
Страница 5: ...User s guide HRP D 4 HS Equipment 51 H Service and warranty 53...
Страница 45: ...User s guide HRP D 44 HS Annex DIAGRAM CONTROL UNIT B...
Страница 46: ...User s guide HRP D 45 HS Annex DIAGRAM TIMER UNIT C...
Страница 47: ...User s guide HRP D 46 HS Annex DIAGRAM SWITCH UNIT D...
Страница 48: ...User s guide HRP D 47 HS Annex DIAGRAM PNEUMATIC SYSTEM E...
Страница 49: ...User s guide HRP D 48 HS Annex DIMENSIONS F 1300 3390 1550 1720...