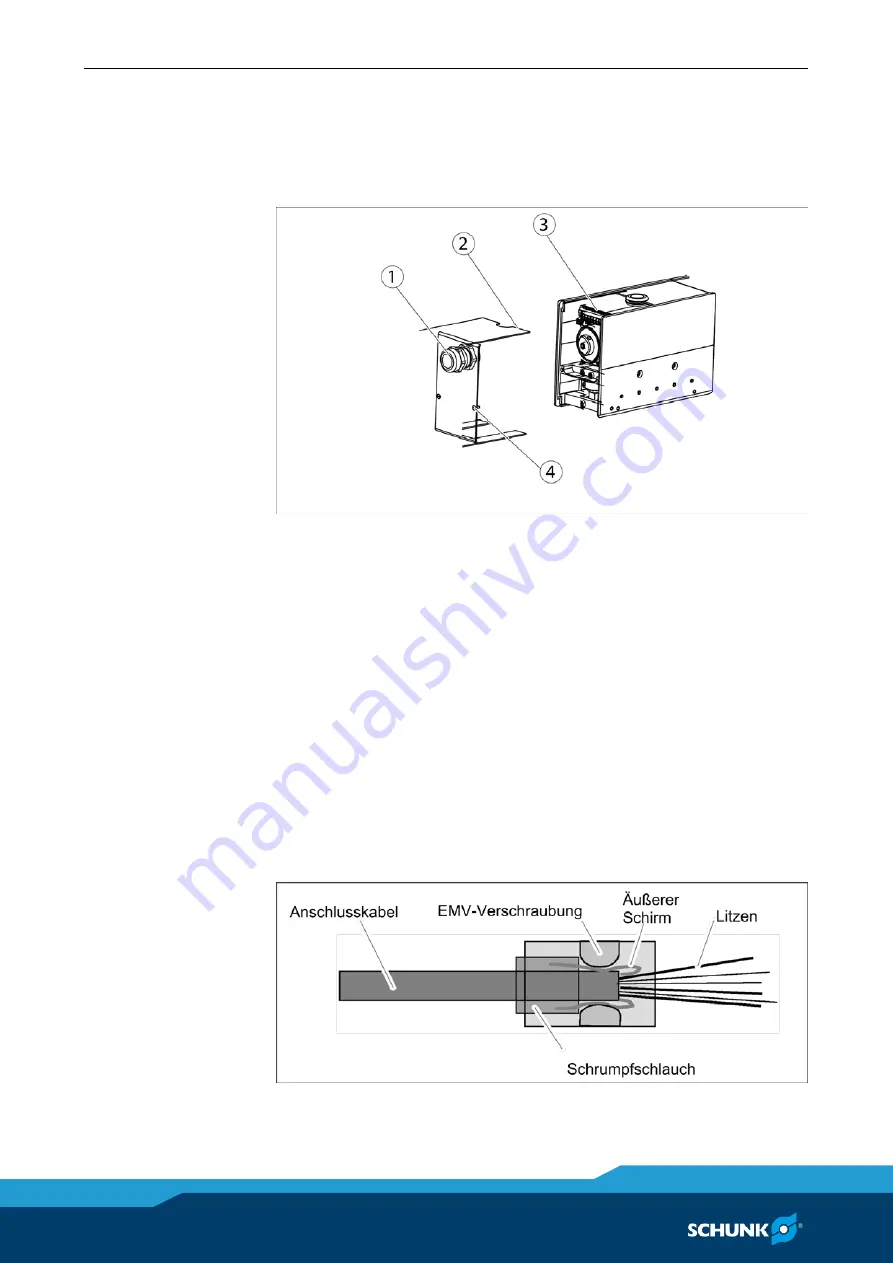
Assembly and installation
32
05.00|EVG 55|en
EMV fitting of connection cable to the gripper
Signal and power lines of the controller (MCS-06) are connected to
the gripper's connection board.
1 Loosen countersunk screws (4) and remove the cover (2).
2 Pull the connection cable through the EMV-fitting (1).
3 Isolate the connection cable and the single conductors (ca. 90
mm from the outer sheath of the MCS-06 connection cable and
the single conductors ca. 5 mm, corresponding to the spring
terminals).
4 Fold the outer shielding over the sheath of the connection cable
and fix the shrink hose (
☞
figure below). The shielding remains
visible at the end of the sheath.
5 Connect the connection cable directly to the connection board
(3). Extending the connection board is not necessary. (
☞
Fig. and
tab. connection board with terminals and configuration of ter-
minals).
EMC-fitting
5.3.2