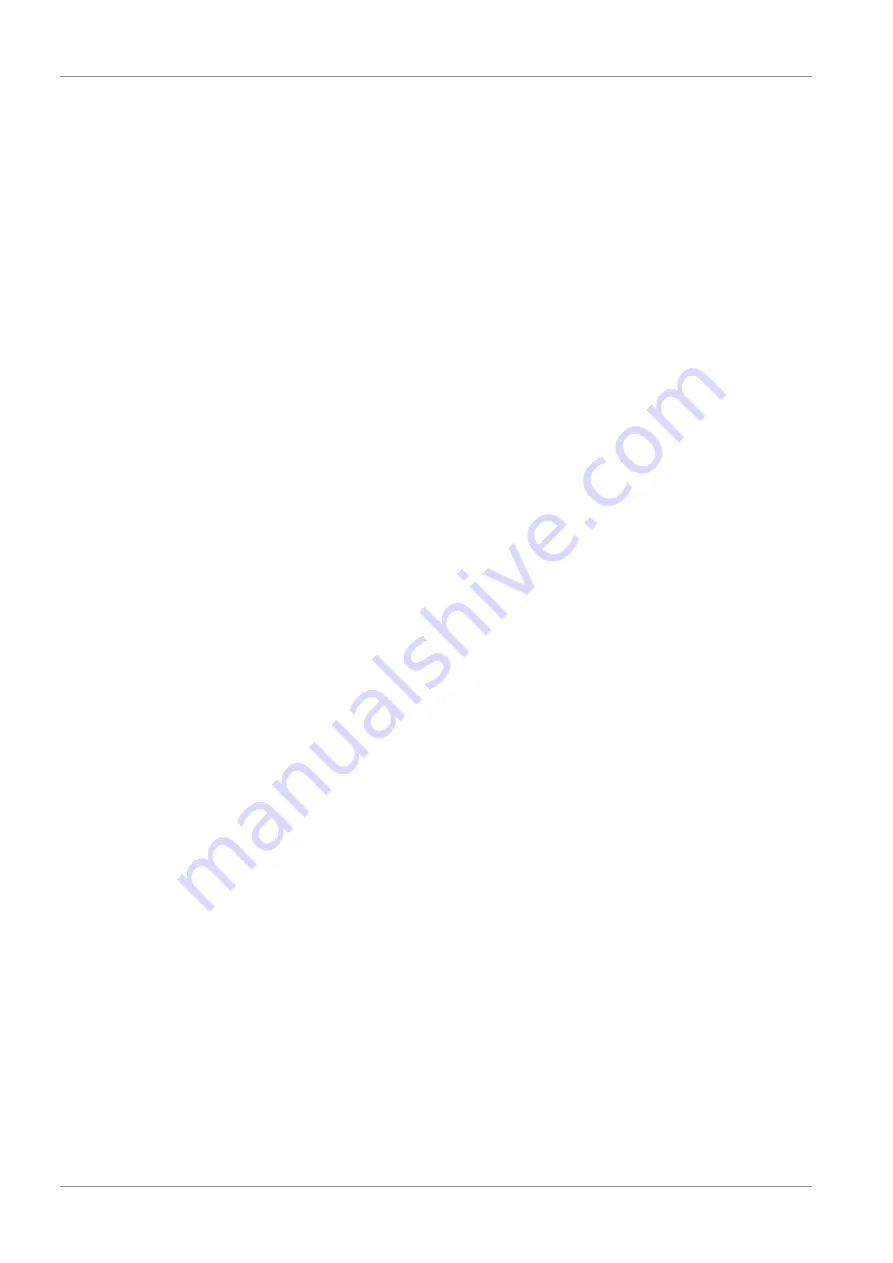
Interfaces
26 / 66
EN-US · 30.30.01.01721 · 01 · 09/19
6 Interfaces
6.1 Basic Principles of IO-Link Communication
The ejector is operated in IO-Link mode to enable intelligent communication with a controller.
The IO-Link communication takes place using cyclical process data and acyclical ISDU parameters.
The ejector’s parameters can be set remotely using IO-Link mode. In addition, the energy and process con-
trol (EPC) feature is available. The EPC is divided into 3 modules:
•
Condition monitoring (CM): Condition monitoring to increase system availability
•
Energy monitoring (EM): Energy monitoring to optimize the vacuum system’s energy consumption
•
Predictive maintenance (PM): Predictive maintenance to increase the performance and quality of the
gripping systems
6.2 Process Data
The cyclical process data is used to control the ejectors and receive current information reported from the
ejector. There is a difference between the input data (Process Data In) and the controlling output data
(Process Data Out).
The input data Process Data In is used to report the following information cyclically:
•
The ejector device status in the form of a status traffic light
•
EPC data
•
Ejector errors and warnings
•
Sensor and actuator supply voltage
•
Air consumption
•
Parameter data, e.g. vacuum data, pressure value (PC variant only), counters, evacuation time, dy-
namic pressure and air consumption.
•
Limit values H1 and H2
The output data Process Data Out is used to control the ejector cyclically:
•
EPC Select is used to define which data is sent.
•
To determine the air consumption, the system pressure can be preset.
•
The ejector is controlled using the suction and blow-off commands.
The exact meaning of the data and functions is described in more detail in the
chapter. A detailed description of the process data can be found in the data dictio-
nary.
The corresponding device description file (IODD) is available for integration into a higher-level controller.
6.3 ISDU Parameter Data
The acyclical communication channel can be used to retrieve what are known as ISDU (Index Service Data
Unit) parameters, which contain further information on the system status.
The ISDU channel can also be used to read or overwrite all the settings, e.g. the limit values, additional
leakage, etc. Further information on the identity of the ejector, such as the part number and serial num-
ber, can be retrieved using the IO-Link. The ejector also provides space for saving user-specific information
here, such as the installation and storage location.
The exact meaning of the data and functions is described in more detail in the “Description of Functions”
chapter.
You can find a detailed diagram of the process data in the data dictionary and IODD.
In order for a control system to access the ISDU parameters, the necessary system functions must be pur-
chased from the manufacturer of the control system and used.
See also
Содержание SXMPi
Страница 1: ...SXMPi IO Link Class B Operating Instructions WWW SCHMALZ COM EN US 30 30 01 01721 01 09 19...
Страница 53: ...Installation EN US 30 30 01 01721 01 09 19 53 66 1 When using a Schmalz connection cable see Accessories...
Страница 66: ...J Schmalz GmbH EN US 30 30 01 01721 01 09 19 Subject to technical changes without notice...