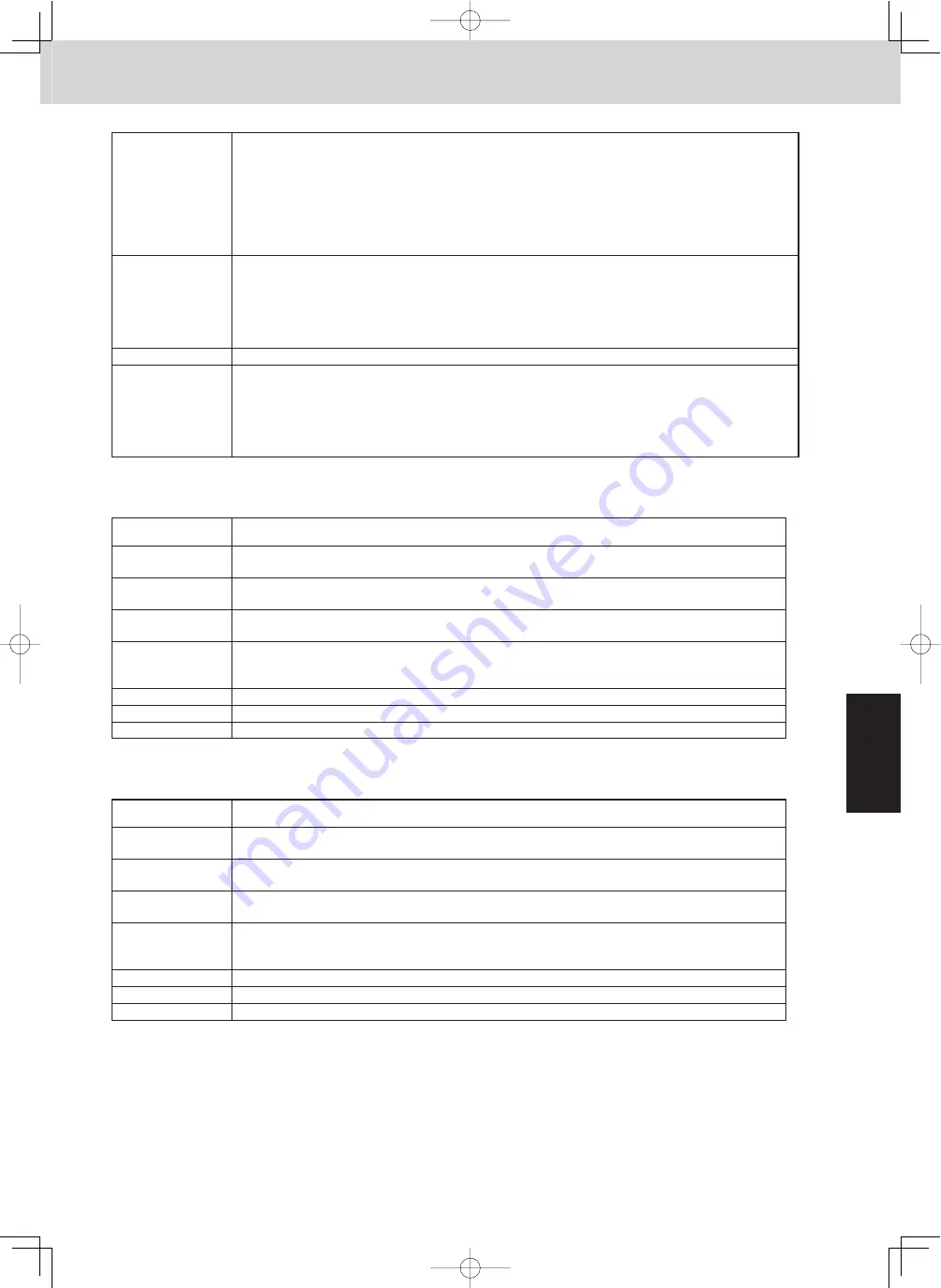
5
5
- 13
W-2WAY ECO-i SYSTEM
Trouble Diagnosis
4. W-2WAY ECO-i Alarm Codes
Check
(3) Leakage from the discharge tube check valve
Trouble:
Although the other compressor is operating and this compressor is stopped, the
discharge temperature of this compressor rises together with the temperature of the
other compressor.
(4) The ambient temperature around the outdoor unit when it is stopped is 43 °C or higher.
(5) If the cause is still unknown after checking the above, then it is possible that electrical noise is
the cause of the trouble. It is necessary to provide a line fi lter or carry out other noise
countermeasures.
Correction
(1) Replace the sensor.
(2) Replace the outdoor unit PCB.
(3) Carry out noise countermeasures.
(4) Repair the refrigerant tubing.
(5) Adjust the amount of refrigerant.
(6) Correct the trouble.
Example
(1) Sensor wiring is partially cut.
Notes
This alarm does not indicate that the sensor is disconnected.
In order to prevent overheating during operation, the outdoor units in this system will not allow a
compressor to start if the discharge temperature does not decrease while the compressor is
stopped. If a sensor malfunction results in continuous detection of a high discharge temperature,
then the compressor may stop for no apparent reason. The purpose of this alarm is to facilitate
identifi cation of the problem in this case.
F06, F23, F25 Alarm
Alarm code
F06, F23, F25
Alarm meaning
Gas temperature sensor trouble at outdoor heat exchanger 1; Gas temperature sensor trouble at
outdoor heat exchanger 2; Gas temperature sensor trouble at outdoor heat exchanger 3
Alarm conditions
(1) A/D step is 10 steps or less (short circuit).
(2) A/D step is 1014 steps or more (open circuit).
Probable cause
(1) Sensor malfunction (including connector)
(2) PCB malfunction
Check
(1) Measure the sensor resistance. Check that the sensor is operating normally.
(2) Use a remote controller monitor or PC monitor to check the temperature that is recognized by
the microcomputer.
Correction
—
Example
—
Notes
—
F07, F24, F26 Alarm
Alarm code
F07, F24, F26
Alarm meaning
Liquid temperature sensor trouble at outdoor heat exchanger 1; Liquid temperature sensor trouble
at outdoor heat exchanger 2; Liquid temperature sensor trouble at outdoor heat exchanger 3
Alarm conditions
(1) A/D step is 10 steps or less (short circuit).
(2) A/D step is 1014 steps or more (open circuit).
Probable cause
(1) Sensor malfunction (including connector)
(2) PCB malfunction
Check
(1) Measure the sensor resistance. Check that the sensor is operating normally.
(2) Use a remote controller monitor or PC monitor to check the temperature that is recognized by
the microcomputer.
Correction
—
Example
—
Notes
—
W-2WAY ECO-i SYSTEM̲Eng5.indd 13
W-2WAY ECO-i SYSTEM̲Eng5.indd 13
2008/09/02 17:46:43
2008/09/02 17:46:43