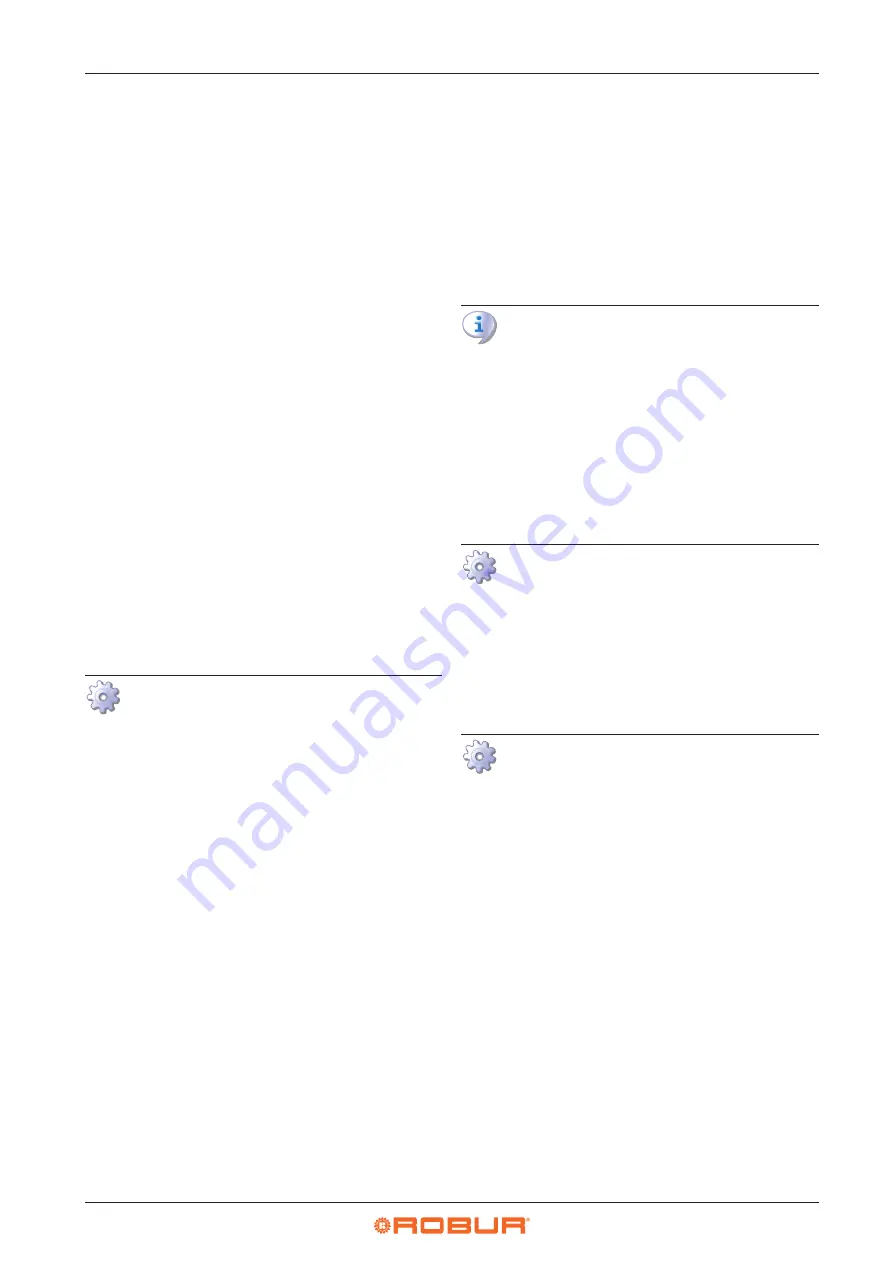
Maintenance
38
7
shown together with water temperature data, blinks.
If it is a permanent error or warning the appliance stops.
(Table 8.1
7.5
RESTARTING A LOCKED-OUT UNIT
Fault signals on the display
In the event of locked-out appliance, an operational code flashes
on the display (first green figure on the left, letter "U" = warning
or "E" = error).
▶
To restart the appliance you must know and perform the
procedure concerning the issue signalled and identified by
the code (Paragraph 8.1
p. 39).
▶
Only act if you are familiar with the issue and with the pro-
cedure (technical expertise and professional qualifications
might be required).
▶
If you do not know the code, the problem, or the procedure,
or you do not have sufficient skills, and in any case of doubt,
contact the AT.
Locked-out appliance
An external intervention (reset or repair) is required due to an
appliance fault or problem with the system.
▶
A reset may be enough for a temporary and provisional fault.
▶
For a fault or breakdown, alert the maintenance technician
or AT.
Reset
There are two options for resetting a fault:
1.
If the appliance is connected to a DDC you may act through
the control device, as described in the relevant manual.
2.
You may act directly from the S61 board as described below
(if the appliance is controlled with external request, this is
the only option).
How to perform reset from the S61 board
To perform the reset directly from the S61 board:
1.
Access Menu 2 under Parameter "__0", to reset flame lock-
out (Error E612), or Parameter "__1" for any other generic
reset, turning and pressing the knob; "2.__0"/"2.__1"
must be displayed (procedure Paragraph 5.6
2.
Press the knob to display the flashing reset request (e.g.
"reS1" to reset flame block).
3.
Press the knob again (the second time) to perform the
reset; the reset request stops blinking, then "2._XX" is
displayed again (e.g. "2.__0"). The reset operation has
been performed.
4.
Exit menu 2 and the menu list, by selecting and press-
ing letter "E" twice, and go back to the normal display of
detected temperature data.
If, after these operations have been carried out, the appliance
does not start, first perform the following simple checks:
▶
Check that any external CS request (Paragraph
p. 28) and
the relevant operating mode switch, or that the DDC (if con-
nected and in controller mode) is in a position that requires
the operation of the appliance.
▶
Make sure that the main power supply switch (GS) fitted
by the electrical installation technician on a suitable panel
(Figure 4.1
▶
Check that the gas supply valve is open.
▶
Check that there are no further messages on the display.
At this point, if the appliance still fails to start:
▶
Refrain from proceeding by trials and errors. Instead, ask an
AT to intervene, communicating the operating code report-
ed by the appliance.
▶
Disconnect the appliance from the gas and electric mains,
interrupting the gas supply by means of the tap and the
power supply by means of the main switch/disconnector
switch (Detail GS in Figure 4.1
p. 26).
▶
Wait for the contacted AT to arrive.
7.6
PERIODS OF INACTIVITY
Avoid emptying the installation
Emptying the system may cause damage due to corro-
sion of the water pipes. Assure at least one of the two
following conditions:
1.
sufficient antifreeze glycol (Paragraph 3.6
2.
empty the system, however taking care to fill it again fol-
lowing the instructions in Paragraph 3.8
Prolonged periods of inactivity
▶
Should you foresee to leave the appliance inactive for a long
period of time, disconnect it from the electrical and gas
mains. These operations must be performed by qualified
personnel.
How to deactivate the appliance for long periods of
time
1.
Switch the appliance off (Paragraph 6.2
p. 35).
2.
Only when the appliance is completely off, power it off
with the main switch/disconnector switch (Detail GS in
Figure 4.1
3.
Close the gas valve.
4.
If necessary, add water with glycol (if the appliance is
disconnected from the power and gas mains, the active
antifreeze protection is missing, Paragraph 3.5
How to reactivate the appliance after long periods of
inactivity
Before reactivating the appliance, the operator/mainte-
nance technician of the system must first of all:
Check whether any maintenance operations are required
(contact the AT; see Paragraph 7.2
Check content and quality of the water in the system, and
if necessary top it up (Paragraphs 3.8
and 3.6
Ensure the flue gas exhaust duct is not obstructed, and
that the condensate drain is clean.
After completing the above checks:
1.
Open the gas valve and ensure there are no leaks; should
gas smell be noticed, close the gas valve again, do not
switch any electrical devices on and request intervention
by qualified personnel.
2.
Power on with the main power supply switch (GS, Figure
p. 26).
3.
Switch on the appliance by means of the provided
control device (DDC or external request, Paragraph
p. 26).