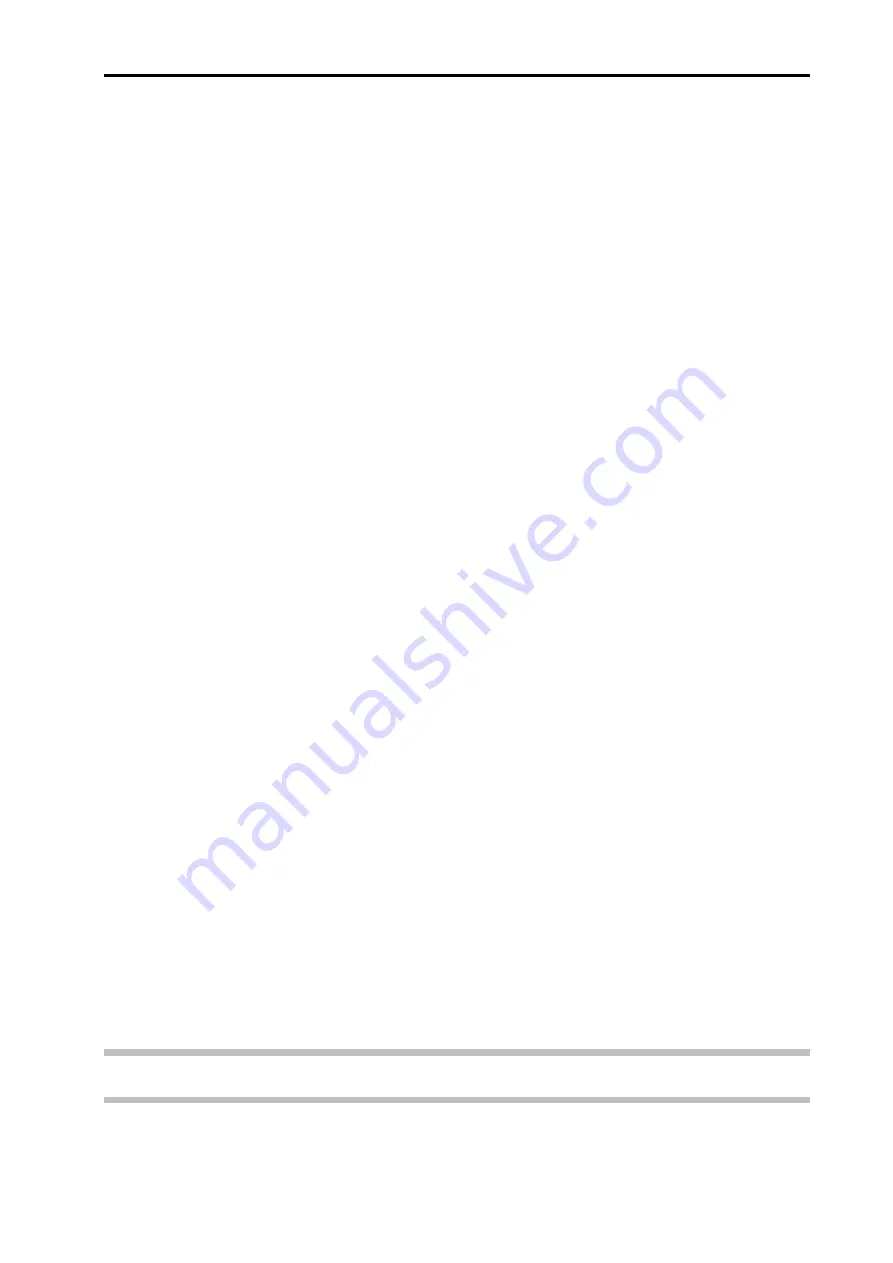
System description
9
1 System
description
The
SPA
2
is a digital servo power amplifier solution designed specifically for use with the Renishaw
UCC
2
or
UCC
lite
controller.
The
SPA
2
is capable of controlling up to seven axes of movement but is customer configurable to the
requirements of the installation.
The features offered by the
SPA
2
are:
•
Two base units
•
SPA
2
3-axis: This is the basic 3-axis configuration suitable for conventional CMMs fitted with
brushed dc motors. It can accommodate both tacho and tacholess velocity feedback systems
and, with the addition of an encoder interface card, it can also accommodate encoder velocity
feedback. An additional axis card can be fitted to extend this unit to a 4-axis system.
•
SPA
2
6-axis: This configuration is suitable for installations requiring between 5 or 6 axis
amplifiers. Like the 3-axis version it can accommodate both tacho and tacholess velocity
feedback systems and, with the addition of encoder interface cards, it can also accommodate
encoder velocity feedback. An additional axis card can be fitted to extend this unit to a 7-axis
system.
•
Two
SPA
2
units can be combined in a single system permitting a servo power amplifier solution
with an overall power rating of 1200 W.
•
Configurable motor voltage
•
The
SPA
2
motor voltage can be configured by software to support a wide range of motor
voltages within the range of 12 and 60 V. The current limit can also be configured up to a
maximum of 5 A continuous, 10 A peak.
•
The voltage setting of each axis is independent and therefore it is possible to have each
machine motor driven by a different voltage.
•
DC analogue tacho or tacholess compatibility
•
The
UCC
2
or
UCC
lite
and
SPA
2
control solution has the ability to support different types of
velocity control loop based on the feedback to the controller.
•
Two control loop feedback methods are integrated into the standard design of the system, these
are either an analogue tacho based feedback system from the motor or obtaining the feedback
from the scales of the CMM.
•
Optional encoder (digital) tacho compatibility
•
The
SPA
2
offers the ability to support encoder tacho based feedback to close the velocity
control loop as an optional interface card.
NOTE:
The
UCC
lite
product only permits 3-axis of machine control.
Содержание apply innovation SPA2
Страница 1: ...Installation guide H 1000 5234 03 A SPA2 servo power amplifier...
Страница 3: ...SPA2 Installation guide...
Страница 15: ...System description 13 1 2 7 SPA2 and UCC2 system layout 1 2 8 SPA2 and UCClite...
Страница 34: ...32 Interconnection schemes 6 2 UCClite DC motor and tacho connection...
Страница 35: ...Interconnection schemes 33 6 3 Dual SPA2 DC motor and tacho configuration...