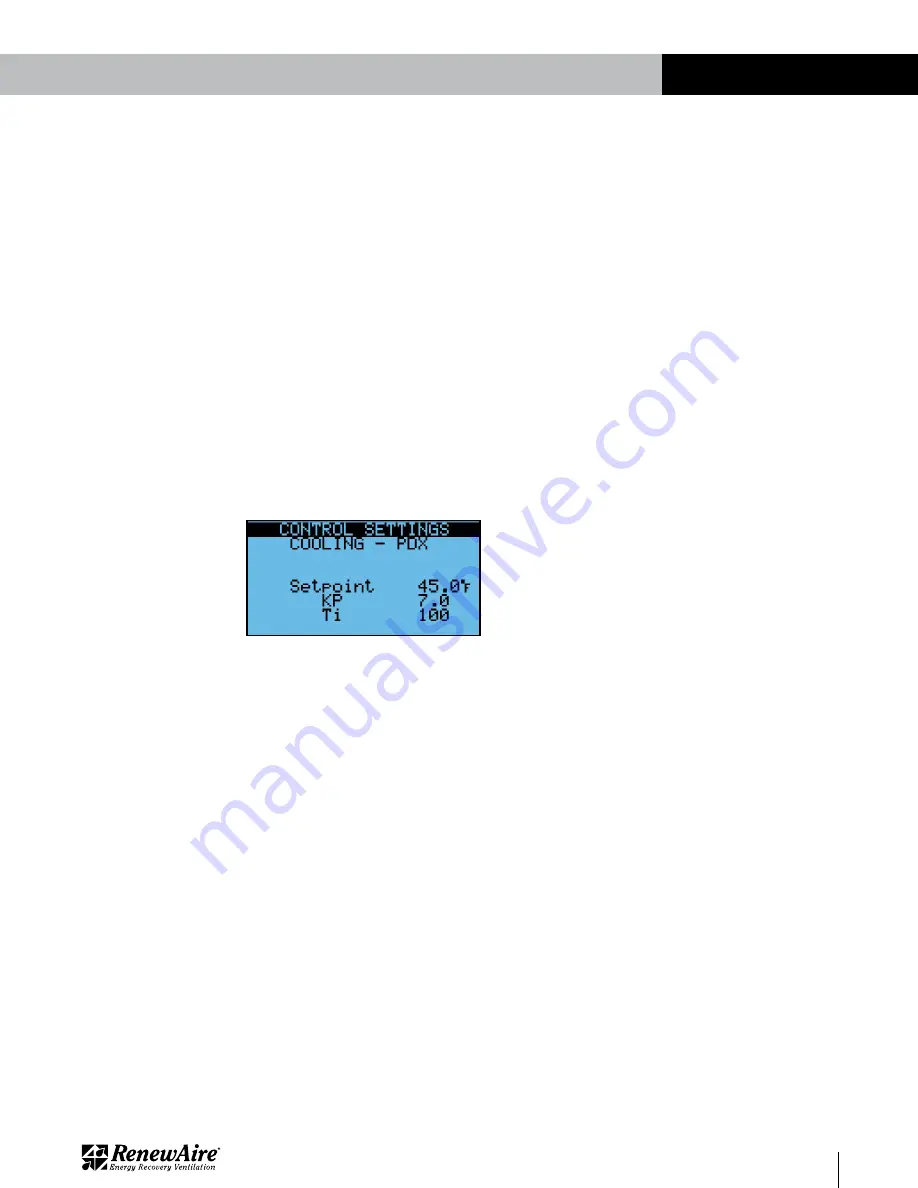
135
1.800.627.4499
DN-Series Integrated Programmable Controls
DOAS
16.1 TUNING PI CONTROL LOOPS
16.0 REFERENCE
For any heating or cooling device that has a variable output and uses a variable control signal
(including HGRH), the desired action is for the heating/cooling device to reach the setpoint
quickly and smoothly. The controller monitors a selected temperature sensor and any variation
from the setpoint is considered “Error.” The controller senses the Error and sends a control
signal (call for heat or call for cooling) to the heating/cooling device. This control signal is
referred to as a “command.” For most variable output hardware, the command will be an analog
0–10VDC signal.
This controller uses PI programming to control the response to Error. PI programming uses two
different types of settings to control the command; KP and Ti
KP = proportional gain
u
Responds directly to difference between setpoint and actual
u
Larger KP values will cause a greater output response and eventually will oscillate.
Ti = integral band
u
Responds to the accumulated difference between setpoint and actual
u
Larger Ti values will cause a slower output response, very small values eventually
will oscillate.
REFERENCE
16.1.1 Proportional Constant (KP)
The Proportional Constant (KP) determines the strength of the command for any given error.
Example:
the setpoint in a heating system is 72°F. The actual temperature is 71°F so the Error
is 10°F, which requires very little heat from the heater. The controller sees there is an error and
immediately sends a call for heat that starts at 0.1% strength and ramps up as needed, but the
rate of increase tapers off as the Error decreases. The rate of increase is proportional to the
amount of Error. When the controller senses that the Error is decreasing, it will slow the rate of
increase of the command.
u
When the Error is small, the rate of increase of the command is slow.
u
When the Error is large, the rate of increase is greater (the command responds proportionally
to the amount of Error).
The factory default KP setting for most heating and cooling devices is 1, which produces a low
and slow response. If the response is too slow, the KP setting can be increased so that the
command will be stronger and faster.
Example:
when the KP setting is 1 and Ti is set for 30 (the factory defaults) and there is a
1°F Error, it takes about 50 seconds for the command to change by 10%. If the KP setpoint
is changed to 10, it takes about 5 seconds for the command to change by 10%. For most
installations, the KP value will have to be increased to speed up changes in the command
signal to an acceptable level. Setting the KP value too high will result in the heater/cooler over-
shooting the setpoint constantly.
u
If the KP value is too low, the command will change too slowly and the setpoint may take too
long to reach.
u
If the KP value is too high, the command will change to 100% too quickly and the
setpoint will be over-shot. This results in the heating/cooling device switching “ON” and
“OFF” constantly.