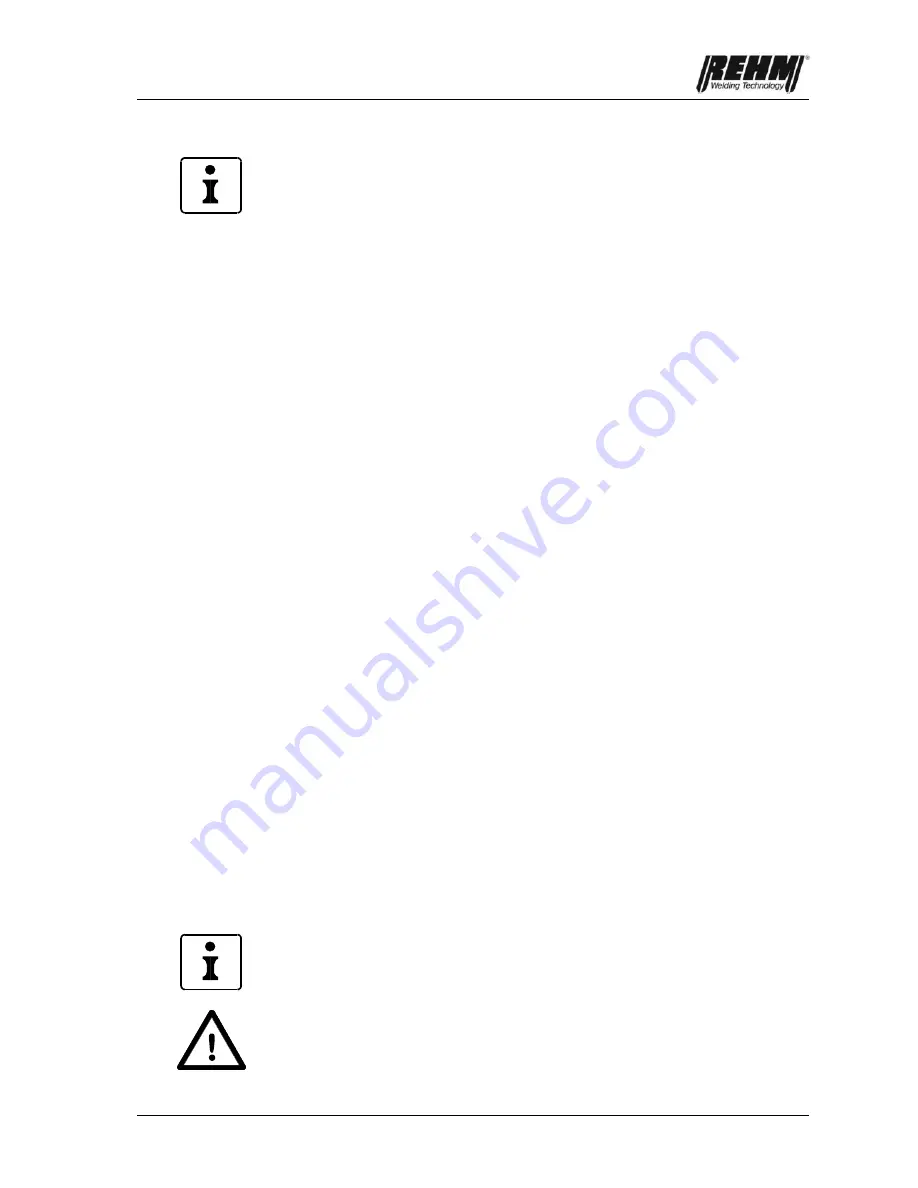
Description of function
17
3.2.3
Special characteristics relating to the operating panel
The microprocessor controller supports the function of the control panel ensuring
that simplicity and speed are the result.
All of the parameters, which have been set on the machine and last used for
welding, remain stored even after the mains switch has been switched off.
When the machine is switched on again the settings that will be displayed
are those that were last use for welding. NOTE: In order to ensure that the
parameters are saved after switching off, the arc must be ignited with those
settings.
Only those parameters that are relevant to the process can be set. E.g. in the
stick-welding mode the setting for 2/4 step, H.F. on/off etc. cannot be set. In
the same way when in the DC mode the parameters for balance and
frequency cannot be set.
After machine is switched on the display runs through all of the settings one
after the other, showing the values set on the display. This enables the
operator to see how the machine is set up. Either by pressing the turn and
set knob, or the torch trigger then this sequence can be interrupted at any
time.
If the turn and set knob is not depressed for 20 seconds then the display
automatically returns to the I1 welding current setting. Thereby the start
setting on the display is the value of the current I1, which is also important for
the orientation for the operator.
If the turn and set knob is not pressed for 20 seconds, then the display
automatically returns to the I1 welding current setting. As a result, you always
have as the start setting the display of the most important value, current I1,
and the same starting point for the operator. The exception to this is the
selection of the welding current I1 (LED I1 flashing), which remains selected
until the knob is pressed again. This makes it easier
–
for example
–
to
quickly find and set the suitable welding current I1 by means of welding tests.
In the interests of safety, and to prevent incorrect operation by mistake, the
turn and set knob must be pressed for more than 2 seconds in order to
activate the special mode or to save or load a program.
3.3 The function of the REHM operators panel
The functions are described in sequence as per Fig. 3.1. and Fig. 3.2.
3.3.1
The welding current setting I1
The setting of the welding current I1 is performed as described in sections 3.1
and 3.2.3. The setting of welding current I1 is done as described in section 3.1,
and is dependant upon the welding process and the power source, either the
Tiger 170 or Tiger 210.
The setting of the welding current I1 can also be done quickly without selecting it
on the operating panel. This is done by depressing the torch button whilst at the
same time alter the current setting to the required value by using the turn and set
knob.
WARNING: Care must be taken when setting the current in this manner, as the
high voltage generator, open circuit voltage, and gas solenoid will be switched on
for 3 seconds; this results in danger for the operator. Furthermore the operator
must also take care that the torch does not come in contact with the workpiece
when using this function as he may strike the arc accidentally.
Содержание 150 3310
Страница 1: ...GB OPERATING INSTRUCTIONS TIG welding units TIGER 170 210 DC AC DC SET...
Страница 7: ...Introduction 7 1 2 General description Fig 1 1 TIGER 170 DC and Tiger 210 AC DC...
Страница 57: ...Spare parts 57 10 2 Machine components photographs 2...
Страница 58: ...Spare parts 58...
Страница 63: ......