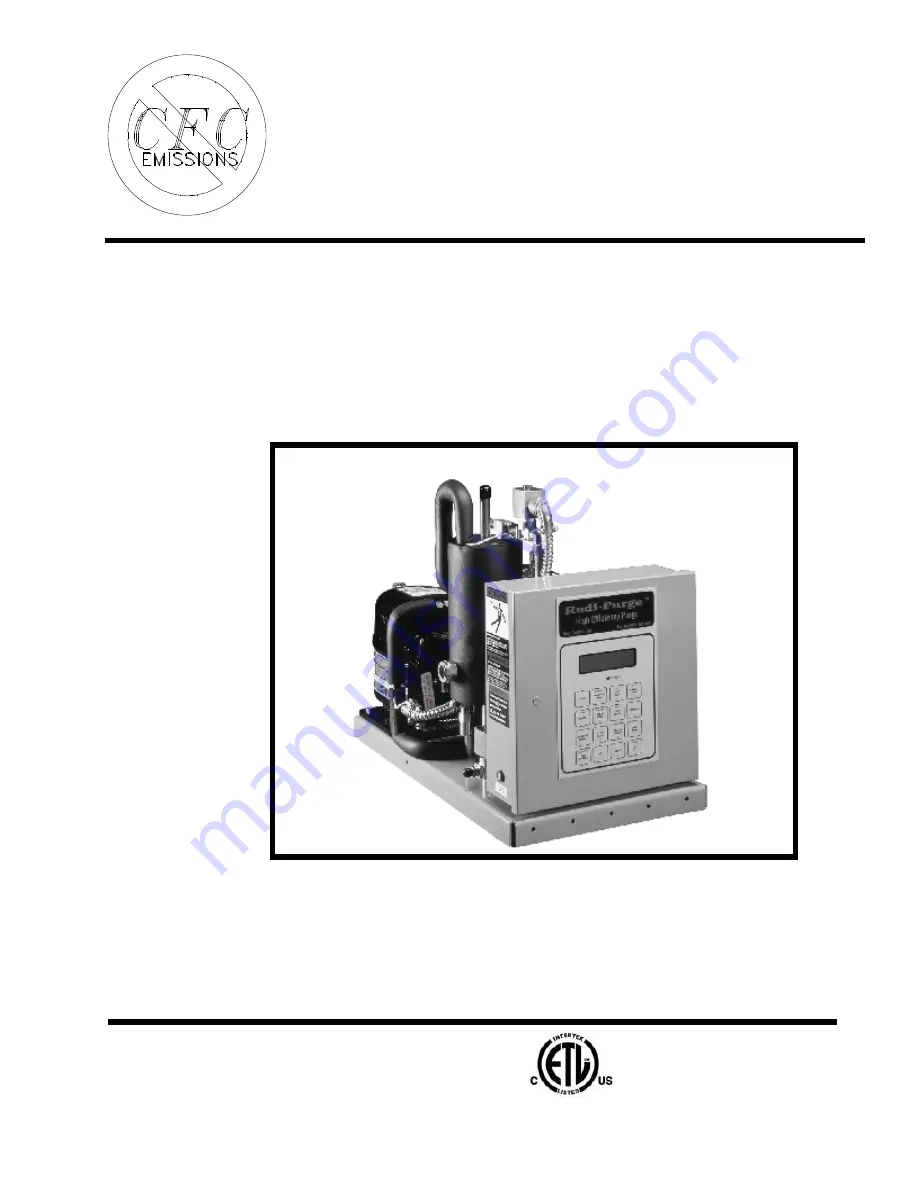
Redi-Purge
™
Model PRG-113-C3 & C4
Microprocessor Controlled
Ultra High Efficiency
Purge Unit
for
Low Pressure Chillers
Manufactured in accordance with
ASHRAE Guidelines 3-1990 Sec. 4.7 and
Standard 15-1992 Sec. 8.3, 8.7 and 10.4
REDI CONTROLS, INC.
Installation, Operation & Maintenance Manual
Literature File No. 1117-02
ETL Listed
3104248
Содержание Redi-Purge PRG-113-C3
Страница 2: ...2 Revised Technically as of October 11 2013 1994 REDI CONTROLS INC GREENWOOD INDIANA...
Страница 4: ...4...
Страница 67: ...67...