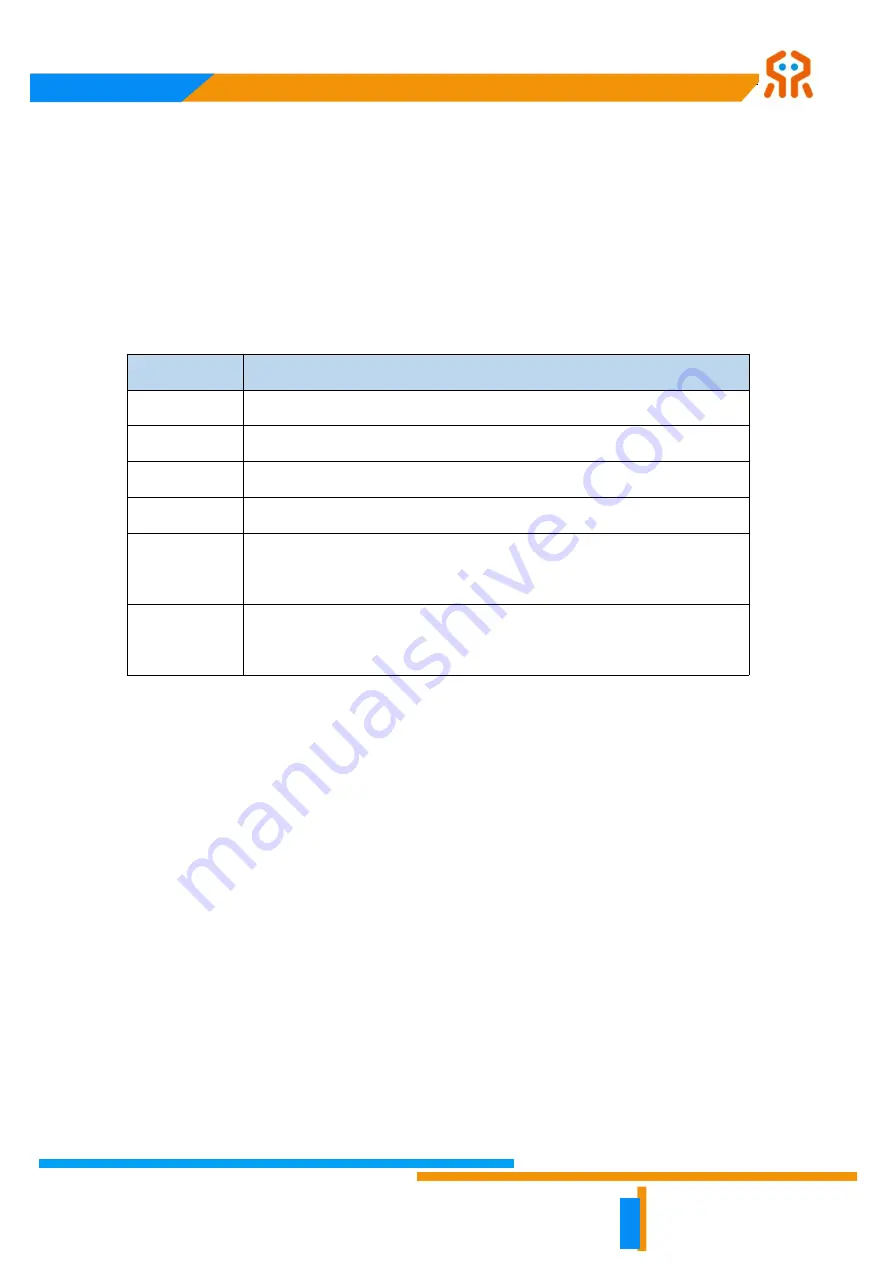
生活美好,臂不可少
http://www.realman-robotics.com
95
completed, it will be sent back to the teach pendant software and displayed in the tool
list. In addition, due to the memory limitation of the robot controller, only 10 tool
coordinates can be saved, so please make sure that the limit will not be exceeded
before calibration. After the calibration is successful, the robot enters the tool
coordinate system whose center is the center of the flange.
The calibration rules of six-point method are shown below.
Table 9 The content of the six-point calibration method.
#
Name
1
Any pose, tool end in contact with reference end.
2
Any pose, tool end in contact with reference end.
3
Any pose, tool end in contact with reference end.
4
Tool end in vertical pose, and in contact with reference end.
5
Keeping the pose of #4 and moving from #4 to some position along
the negative x-axis of the Base coordinate system.
6
Keeping the pose of #4 and moving from #4 to some position along
the positive z-axis of the Base coordinate system.
3. Manual Setting of the Tool End Coordinate System
When the user knows the accurate relative pose of the tool with respect to the center
of the flange at robot end, the tool coordinate system can be set directly by manually
entering the information. After selecting this feature, enter the name and pose of the
new tool, and click the “Add Tool” button to send the new tool information to the
robot controller and display it in the tool table. After the calibration is successful, the
robot operates in the tool coordinate system of the center of the end flange.
4. Payload at the End
After the tool calibration, we need to enter the weight and center of gravity position of
the end tool to make the tool parameters at the end of the robot more durable.