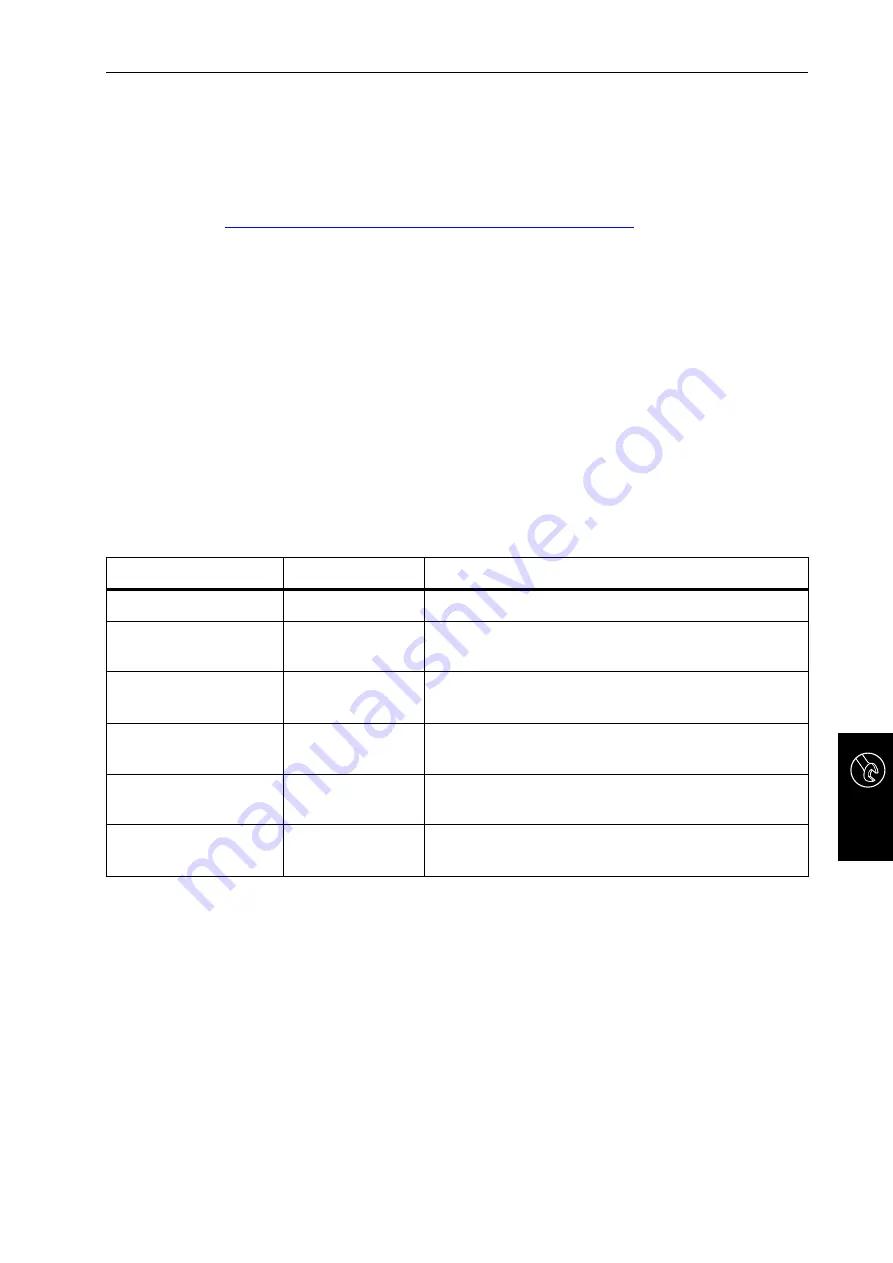
General maintenance and repair (all types)
199
9
AXIS
AXIS
20.1
AXIS
9.4
Cleaning
We recommend cleaning the machine with a light jet of water immediately after
every use in order to maintain the value of your machine.
To facilitate cleaning, fold up the protective grids in the hopper (see chapter
9.3: Opening the protective grid in the hopper, page 197
The following instructions must be observed for cleaning:
Clean the outlets and the area of the slide guide from below only.
Only clean oiled machines at washing points fitted with an oil separator.
When cleaning with high-pressure water, never aim the jet directly at warning
signs, electrical equipment, hydraulic components, and sliding bearings.
After cleaning, we recommend treating the
dry
machine,
especially the coated
spreader vanes and stainless steel parts
, with an environmentally friendly anti-
corrosion agent.
A suitable polishing kit can be ordered from authorised dealers for use in treating
rust spots.
9.5
Lubrication plan
Lubrication points
Lubricant
Description
Drive shaft
Grease
See operator’s manual of the manufacturer.
Metering slide, stop le-
ver
Grease, oil
Ensure smooth movement, and grease regularly.
Spreading disc hub
Graphite grease
Ensure smooth movement of pivot and sliding sur-
faces and grease regularly.
Upper and lower hitch
balls
Grease
Grease regularly.
Joints, bushes (agitator
drive)
Grease, oil
They are designed for dryness but can be slightly lu-
bricated.
Drop point adjustment,
adjustable floor
Oil
Ensure smooth movement and oil regularly from the
outer edge inward and from the base outward.
Содержание AXIS-M 20.2 EMC
Страница 4: ......
Страница 12: ...Table of Contents VIII ...
Страница 44: ...Safety 3 24 AXIS AXIS ...
Страница 51: ...Technical data 31 4 AXIS AXIS 4 2 4 Agitator Figure 4 6 Agitator 1 Metering slide 2 Agitator ...
Страница 64: ...Axle load calculation 5 44 AXIS AXIS ...
Страница 66: ...Transportation without tractor 6 46 AXIS AXIS ...
Страница 68: ...Instructions regarding the spreading operation 7 48 AXIS AXIS ...
Страница 110: ...General commissioning all machine types 8 90 AXIS AXIS ...
Страница 144: ...Maintenance and repair C 124 AXIS AXIS 20 2 ...
Страница 178: ...Maintenance and repair C 158 AXIS AXIS 30 1 AXIS 40 1 ...
Страница 214: ...Maintenance and repair C 194 AXIS AXIS 50 2 ...
Страница 236: ......