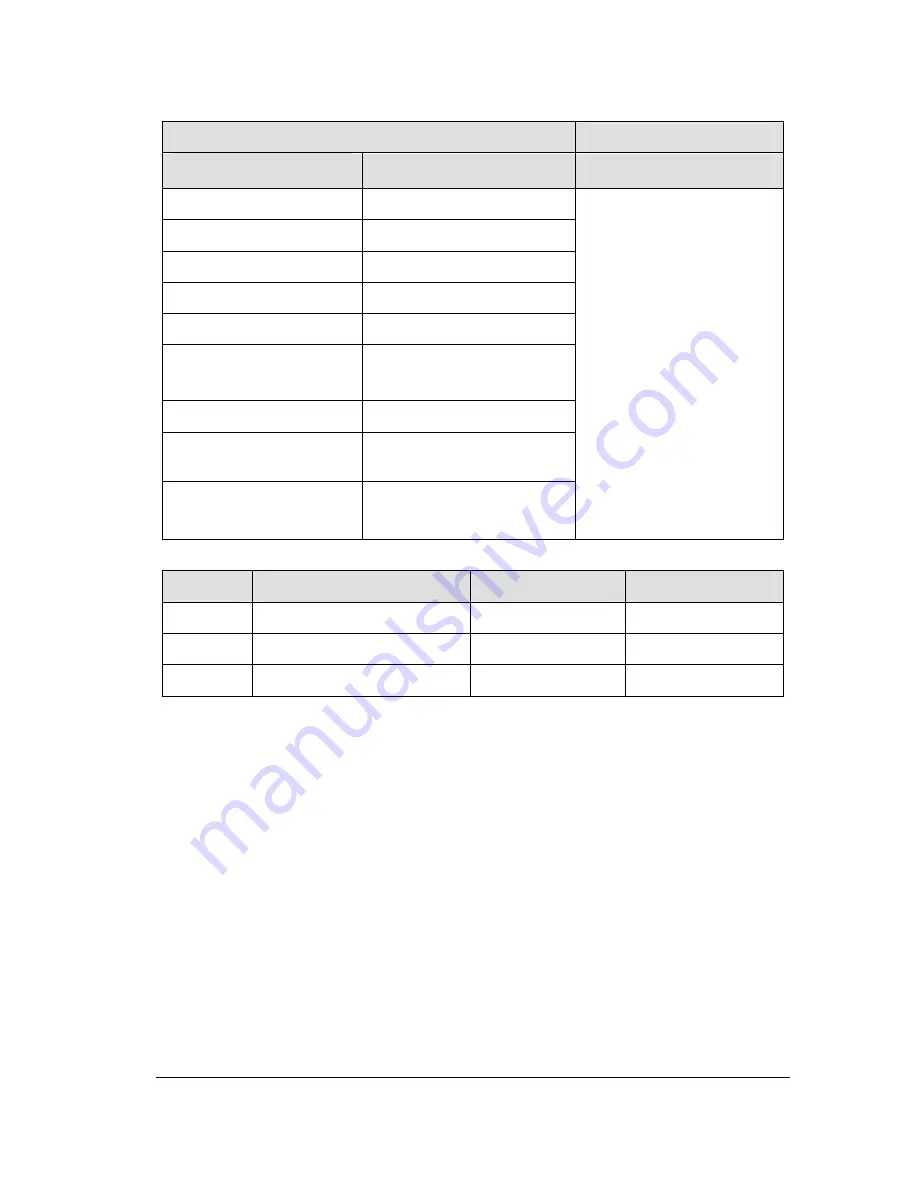
95
Table 2.11 PID setting and PID feedback
Process quantity input data
Feedback input data
f003
(
f005
)
setting
setting method
f900 setting
0
built-in potentionmeter
1
AI1
2
AI2
3
Keypad (frequency)
4
Serial communication
5
UP/DOWN from external
contact
6
-
7
Keypad (percentage term)
(see f830)
-
(
when under remote
control, f002=0
)
Multi-step speed setting
f900=1:
AI1, 0~5VDC or 0~10V
DC or 4~20mA DC.
f900=2:
AI2, 0~10V DC.
NO.
Parameter Name
Setting Range
Default
f901
Proportional gain
0.01~100.0
varies by model
f902
Integral gain
0.01~100.0
varies by model
f903
Differential gain
0.00~2.55
0.00
The control effect of f901: The greater the set point is, the smaller the deviation between
target value and feedback value after stability is. However, excessively large set point
may arouse vibration in the controlled object and make it unstable. Furthermore, if the
set point is small, the deviation between target value and feedback value after stability
becomes greater.
The control effect of f902: Any residual deviation after proportional gain tuning can be
cleared with time through integral gain function. Higher integral gain can realize rapid
response to process deviation, but may result in instability such as oscillation.
The control effect of f903: Differential gain will tune the response time of the inverter
according to the rapid change during the process. Unnecessary raise of of differential
gain value may result in greater fluctuation of the motor speed and make the system
unstable.
Содержание QD100 Series
Страница 1: ...QD100 Series Frequency Inverter USER S MANUAL English Version...
Страница 2: ......
Страница 91: ...89 2 Setting example Parameter setting value...