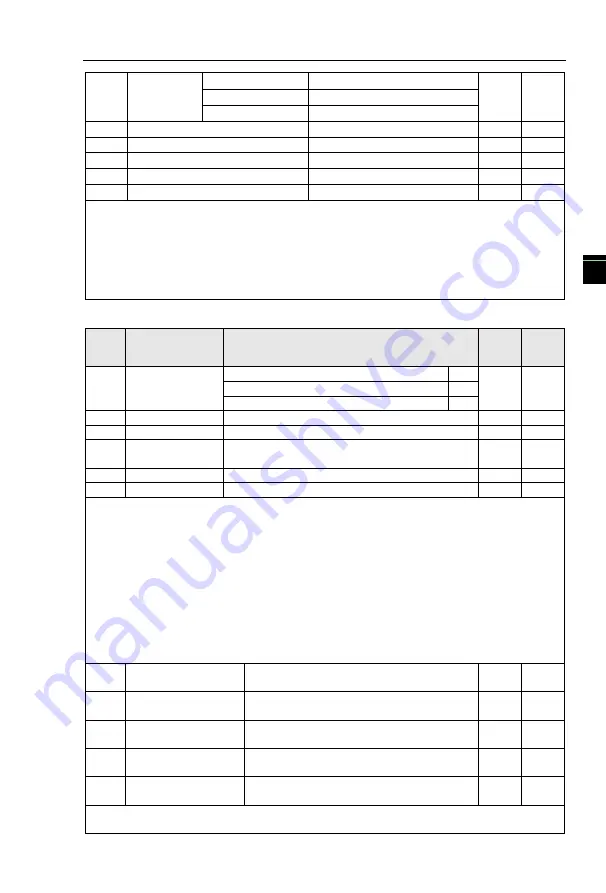
Chapter 5 Function parameter
113
Ch
ap
ter 5
Hundreds digit
VDO3(0 to 1
,
same as above)
Thousands digit
VDO4(0 to 1
,
same as above)
Ten thousands digit
VDO5(0 to 1
,
same as above)
E3.17 VDO1 output delay time
0.0s to 3600.0s
0.0s
☆
E3.18 VDO2 output delay time
0.0s to 3600.0s
0.0s
☆
E3.19 VDO3 output delay time
0.0s to 3600.0s
0.0s
☆
E3.20 VDO4 output delay time
0.0s to 3600.0s
0.0s
☆
E3.21 VDO5 output delay time
0.0s to 3600.0s
0.0s
☆
VDO and DO output function is similar
,
can be used in conjunction with VDIx
,
to achieve
some simple logic control .
When VDOx output function is 0, output status is decided by DI1~DI5 input status on the
control board, VDOx and Dix one-to-one correspondence.
When the output function selection is not 0, VD0x function setting and using method is same
as D0 in F2 output parameter, please read F2 group parameter description.
The VDOx output valid status can be set by E3.16 setting, select positive logic or anti-logic.
5-2-19.
Motor parameters: b0.00-b0.35
Code
Parameter
name
Setting range
Factory
setting
Change
limits
b0.00
Motor type
selection
General asynchronous motor
0
0
★
Asynchronous inverter motor
1
Permanent magnet synchronous motor
2
b0.01 Rated power
0.1kW to 1000.0kW
-
★
b0.02 Rated voltage
1V to 2000V
-
★
b0.03 Rated current
0.01A to 655.35A(inverter power≤55kW)
0.1A to 6553.5A(inverter power >55kW)
-
★
b0.04 Rated frequency
0.01Hz to F0.19(maximum frequency)
-
★
b0.05 Rated speed
1rpm to 36000rpm
-
★
Above b0.00 to b0.05 are the motor nameplate parameters, which affects the accuracy of the
measured parameters. Please set up according to the motor nameplate parameters. The excellent
vector control performance needs the accurate motor parameters. The accurate identification of
parameters is derived from the correct setting of rated motor parameters.
In order to guarantee the control performance, please configure your motor according to the
inverter standards, the motor rated current is limited to between 30% to 100% of the inverter rated
current. The motor rated current can be set, but can not exceed the inverter rated current. This
parameter can be used to determine the inverter's overload protection capacity and energy
efficiency for the motor.
It is used for the prevention of overheating caused by the self-cooled motor at low speed , or
to correct for protecting the motor when the little change of the motor characteristics may affect
the changes of the motor capacity.
b0.06
Asynchronous motor
stator resistance
0.001Ω to 65.535Ω(inverter power≤55kW)
0.0001Ω to 6.5535Ω(inverter power>55kW)
-
★
b0.07
Asynchronous motor
rotor resistance
0.001Ω to 65.535Ω(inverter power≤55kW)
0.0001Ω to 6.5535Ω(inverter power>55kW)
-
★
b0.08
Asynchronous motor
leakage inductance
0.01mH to 655.35mH(inverter power≤55kW)
0.001mH to 65.535mH(inverter power>55kW)
-
★
b0.09
Asynchronous motor
mutUal inductance
0.01mH to 655.35mH(inverter power≤55kW)
0.001mH to 65.535mH(inverter power>55kW)
-
★
b0.10
Asynchronous motor
no-load current
0.01A to b0.03(inverter power≤55kW)
0.1A to b0.03(inverter power>55kW)
-
★
b0.06 to b0.10 are the asynchronous motor parameters, and generally these parameters will
not appear on the motor nameplate and can be obtained by the inverter auto tuning. Among which,