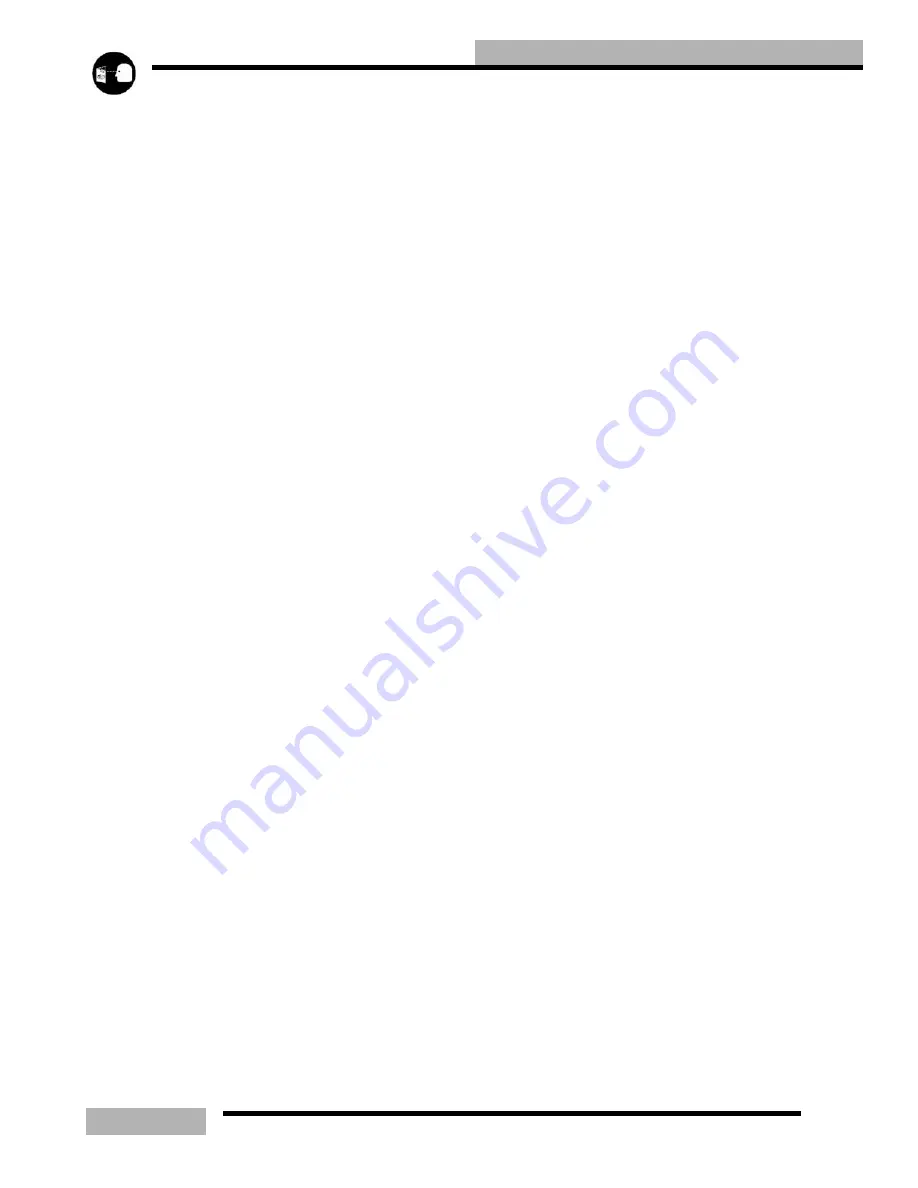
11.25
REAR SUSPENSION
loosen and remove cylinder head assembly.
13. Pour the oil out of the shock body. Discard old oil into an
approved storage container and dispose appropriately.
Never reuse damper oil during shock rebuild.
14. Using the I.F.P extraction tool thread the tool into the I.F.P
and pull upwards, removing the I.F.P from the shock body.
Account for wear band and an O-ring. Note: Not
applicable for emulsion shock
15. Clean the inside of the shock body using clean parts-
cleaning solvent and blow dry using compressed air.
16. Place the shock piston rod upper mount in bench vise,
begin piston and valve removal. Arrange parts removed in
the sequence of disassembly. The piston should have the
flat slots facing the nut end (as highlighted in black).
17. Items to inspect: Piston rod for straightness, nicks or burrs.
Cylinder Head Assembly / DU Bearing clean, inspect, or
replace. Inside of shock body for scratches, burrs or
excessive wear. Teflon piston and I.F.P wear band for cuts,
chipped or nicked edges, or excessive wear. O-rings for
nicks, cuts, or cracks. Cap and rod seals for nicks, cuts or
cracks. Valve discs for kinks or waves. Compression
bumpers (ski shocks only) for chipping, cracking or
missing. Should any of these items be in question
replacement is recommended.
RYDE FX MONO-TUBE SHOCK ASSEMBLY
1.
Place the piston rod upper mount into the vise. Reassemble
damper rod assembly in the reverse order of disassembly.
Special attention should be paid the order of the Rebound
and Compression disc (shim) stacks, ensuring that they are
in the same order prior to disassembly. Tighten the lock
nut to 15-20 ft-lb. of torque. DO NOT OVER-TORQUE.
If excessive torque is applied, damage to the piston and
valves will occur.
2.
Secure the shock body by its lower mount in vise. The use
of soft jaws is recommend to prevent damage or marks to
the shock. It is important that the gas shock be retained in
the vice by the lower mount. Any other method of securing
the shock body during these procedures may deform the
shock body cylinder.
NOTE: The next points on IFP are not applicable for
emulsion shocks. Proceed to assembly of the
pressure valve.
3.
Thread the positioning head onto the I.F.P locator tool and
adjust the top of the value indicator to the appropriate
measurement. Depending on which shock absorber is
being worked on, adjust the piston location tool to the
specified depth indicated in the shock specification chart.
4.
Apply a thin film of oil onto the floating wear band and O-
ring and install the floating piston into the top of the shock
body, positioning it below the counterbore.
5.
Using the tool as a handle, push the floating piston down
into the shock body, being careful not to damage I.F.P
wear band and O-ring, until the value indicator knob
comes in contact with the shock body. The piston should
now be located correctly.
6.
Screw the pressure valve assembly into the valve port by
hand with a slotted head screwdriver; and tighten to 100-
110 in.lb of torque.
7.
Fill the shock body with shock oil. Internal Floating Piston
Shocks: Fill the shock body with shock oil to the bottom of
the thread within the cylinder. Emulsion Shocks: Fill
shock body with 110cc's of oil. This will allow for the
required air space to properly gas charge the shock with
nitrogen gas.
NOTE: After filling the shock body with oil, allow a
couple of minutes for all air bubbles to rise to the
top.
8.
With the cylinder head assembly pushed down against the
piston, carefully, insert the piston rod and assembly into
the cylinder; Slightly oscillating the piston rod to allow
piston to enter shock body bore. A light coating of oil on
the piston wear band will ease installation.
9.
Slowly push the piston rod and assembly into shock body
until the cylinder head assembly bottoms on the cylinder
counterbore. Slight up and down movement may be
required to allow all air to pass through piston assembly.
10. During installation, some shock oil will overflow. Wrap a
shop cloth around shock body to catch possible oil
overflow. Fast installation of the piston rod and assembly
may displace the floating piston from its original position.
This must not occur if the damper is expected to perform
as designed.
11. Using an open face spanner wrench tighten cylinder head
securely into the shock cylinder.
12. Pressurize the shock, through the pressure valve, with
nitrogen gas to the specified pressure.
13. If using RydeFX inflation tool Refer to Procedures for use
of replaceable inflation needle instruction manual found in
the RydeFX inflation tool case.
14. After being compressed, the piston rod should fully extend
from the shock body once the shock has been pressurized.
15. Install the small button head screw in the pressure valve
assembly and tighten securely.
16. Reinstall sleeve and bushings in lower shock mount.
FOX PS-5 DISASSEMBLY
1.
Remove the shock from the vehicle.
2.
Remove the steel sleeve from the eyelet using the mallet
and an appropriate sized socket.
3.
Pry the polyurethane bushings out using the flat blade
screwdriver, being careful not to scratch the body cap.
4.
Clean the entire shock assembly with soapy water. Try to
Содержание SUPERSPORT 2006
Страница 48: ...NOTES SPECIFICATIONS 1 48...
Страница 55: ...2 7 GENERAL SAE TAP DRILL SIZES METRIC TAP DRILL SIZES DECMIAL EQUIVALENTS...
Страница 60: ...2 12 GENERAL SPECIAL TOOLS...
Страница 61: ...2 13 GENERAL...
Страница 62: ...2 14 GENERAL...
Страница 106: ...4 18 CARBURETION...
Страница 139: ...6 27 ENGINE 340 550 ENGINE REBUILDING 10 11 3 4 12 13 5 2 14 1 16 15 16 9 17 6 7 8...
Страница 156: ...7 12 CLUTCHING 1 1 2 3 4 5 6 7 18 17 10 8 9 13 12 11 15 16 14...
Страница 192: ...8 20 FINAL DRIVE...
Страница 200: ...10 2 FRONT SUSPENSION STEERING FUSION IQ RMK 600 RMK Fusion 14 78...
Страница 201: ...10 3 FRONT SUSPENSION STEERING EDGE RMK Apply Polaris All Season Grease to all zerks...
Страница 202: ...10 4 FRONT SUSPENSION STEERING 42 5 EDGE Apply Polaris All Season Grease to all zerks...
Страница 203: ...10 5 FRONT SUSPENSION STEERING WIDETRAK Apply Polaris All Season Grease to all zerks...
Страница 244: ...11 28 REAR SUSPENSION...
Страница 256: ...12 12 CHASSIS HOOD...
Страница 282: ...13 26 ELECTRICAL...
Страница 288: ...13 32 ELECTRICAL...
Страница 289: ...14 1 WIRE DIAGRAM 2006 600 FUSION HO HOOD...
Страница 290: ...14 2 WIRE DIAGRAM 2006 HO RMK HOOD...
Страница 291: ...14 3 WIRE DIAGRAM 600 HO FUSION RMK CHASSIS...
Страница 292: ...14 4 WIRE DIAGRAM 600 HO FUSION RMK CHASSIS CALL OUTS...
Страница 293: ...14 5 WIRE DIAGRAM 700 900 ENGINE...
Страница 294: ...14 6 WIRE DIAGRAM 700 900 ENGINE AND ENGINE CALL OUTS...
Страница 295: ...14 7 WIRE DIAGRAM 700 900 CHASSIS...
Страница 297: ...14 9 WIRE DIAGRAM 340 550 FUJI FAN ENGINE CHASSIS...
Страница 298: ...14 10 WIRE DIAGRAM 500 FUJI ENGINE CHASSIS...
Страница 299: ...14 11 WIRE DIAGRAM 500 600 IBERTY ENGINE CHASSIS...
Страница 300: ...14 12 WIRE DIAGRAM WIDETRAK ENGINE CHASSIS...