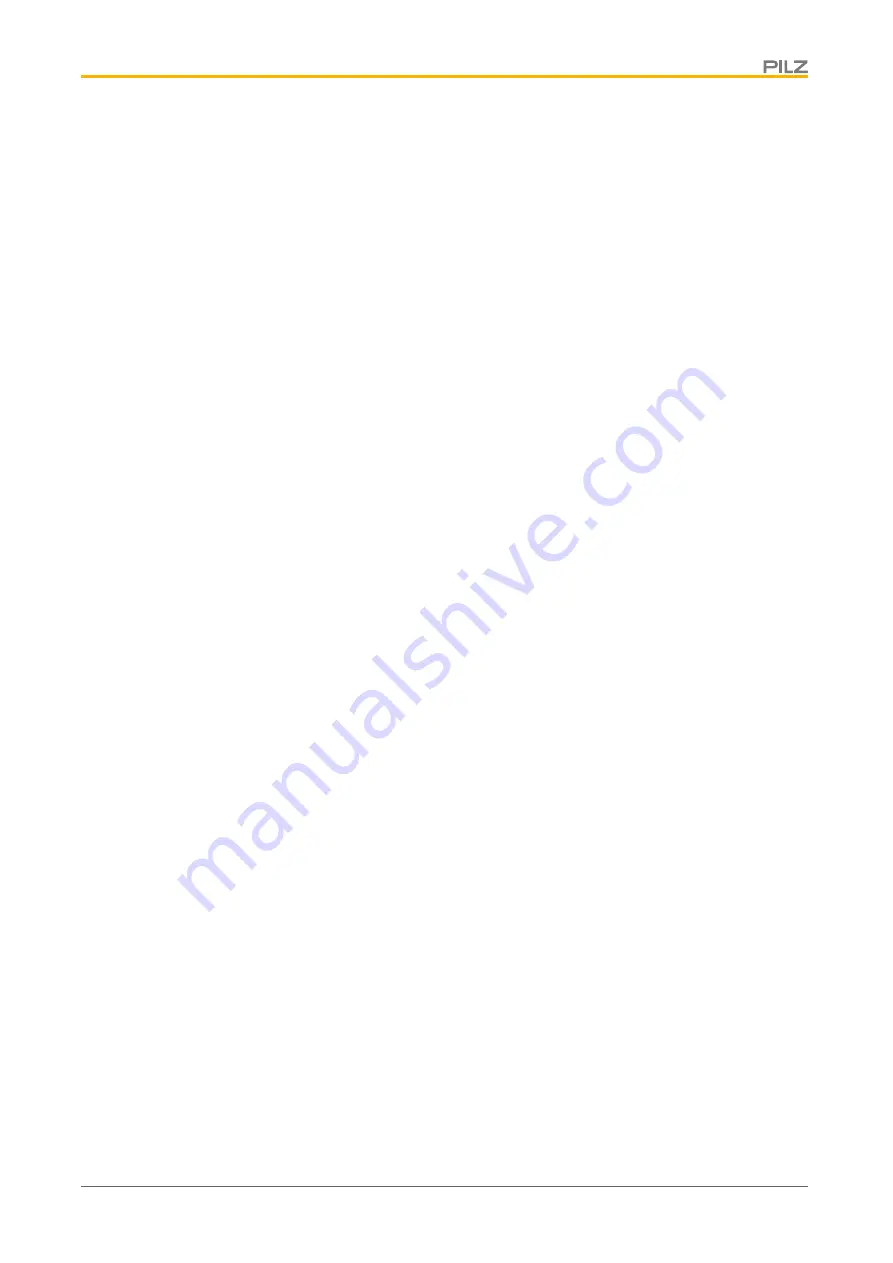
Function description
Operating Manual PMI 6 primo
1004647-EN-02
18
4.4.2
CANopen
The CANopen interface is suitable for networking drive components at field level. It meets
the requirements defined in the communications protocol DS-301.
The following device classes with CANopen device profiles are supported:
}
I/O modules DS-401
}
Electrical drives DS-402
}
Encoder DS-406
The CAN network is designed as a linear structure. The CANopen communication protocol
is based on CAN.
}
CAN networking with the motion control software is suitable for applications with a max-
imum subscriber number of ≤ 16 and a cycle time ≥ 1 ms.
}
Only CAN devices that are known to the controller or support a corresponding device
profile can be operated in the motion control software's CAN network.
}
CAN devices detected by the motion control software are ready for operation immedi-
ately after the initial network run-up. No complex configuration of the CAN devices is re-
quired.
}
The overall cable length and the length of the stub lines depend on the transmission
rate.
}
Process data objects (PDO) are defined for each CAN device type and cannot be cus-
tomised by the user.
}
For servo amplifiers, the "FS" command can be used to set which process data is to be
exchanged between the motion control software and the servo amplifier (see "PM-
Cprimo Programming Manual").
}
The signal lines must be terminated with resistors (120 Ohm) on the first and last sub-
scriber. The resistors are generally integrated within the connected devices and can be
activated there. For a PMI 6 primo a terminating resistor can be activated in the fieldbus
junction box.
4.4.3
PROFIBUS DP
PROFIBUS is an open fieldbus standard. Communication is defined in IEC 61158 and IEC
61784. Further provisions have been defined in specifications published by the PROFIBUS
User Group. These specifications are available from PROFIBUS International.
On a certain unit type, the PROFIBUS interface is available together with a CANopen inter-
face on an RJ45 socket (X7).
Properties:
}
The PROFIBUS is configured using the CD command: Slave address, address range,
see PMCprimo Programming Manual.
}
A total of up to 108 bus variables can be read and written (see PMCprimo Programming
Manual):
– Address space of bus variables: $B1 to $Bx108 (can be set using the CD com-
mand).
– Data width: 16 Bit including sign
– Value range: -32768 to 32767 (Hex: 0x0000 bis 0x7FFF).