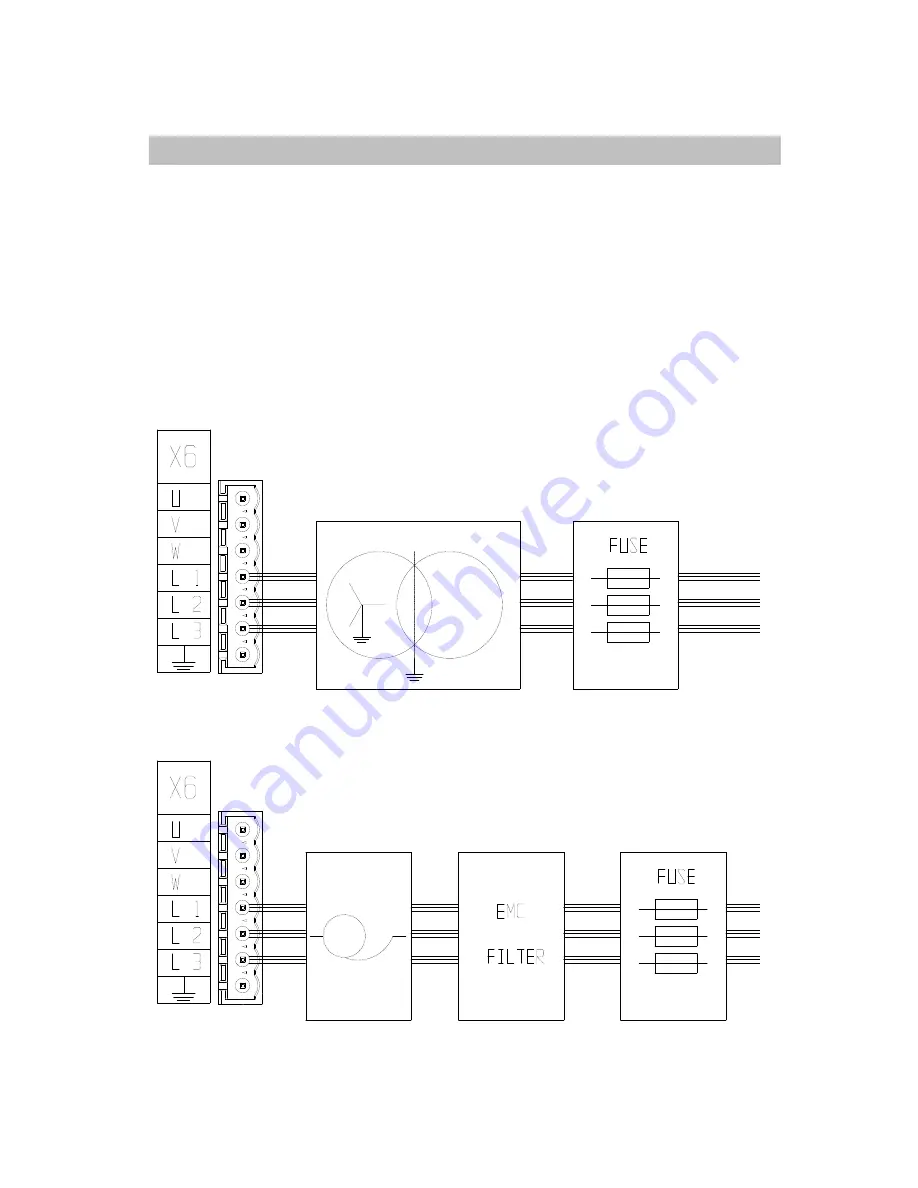
Parker Hannifin S.p.A S.B.C. Division
SLVDN User’s Manual
Page 32 of 181
5.5. Line connection diagrams
The SLVD-N converter can be connected to the power supply in various ways.
If a transformer with an electrostatic shield between the primary and the secondary is used,
EMC filters will not have to be installed. If an auto-transformer, a transformer without
electrostatic shield or a direct connection to the power network is used, EMC filters must be
used.
The converter can be used only in grounded TT and TN industrial networks with a max. short
circuit symmetrical current of 5kA maximum at 230V +10%.
Do not use in ungrounded networks or in networks with asymmetrical grounding (IT)
Use of a transformer connected the secondary in a star configuration with electrostatic
shield
(10, 15 and 17 versions have two PE pins)
Use of the auto-transformer
(10, 15 and 17 versions have two PE pins)
Содержание SLVD1N
Страница 7: ...Parker Hannifin S p A S B C Division SLVDN User s Manual Page 7 of 181 ...
Страница 22: ...Parker Hannifin S p A S B C Division SLVDN User s Manual Page 22 of 181 ...
Страница 23: ...Parker Hannifin S p A S B C Division SLVDN User s Manual Page 23 of 181 ...
Страница 34: ...Parker Hannifin S p A S B C Division SLVDN User s Manual Page 34 of 181 5 6 Motor connection diagrams ...
Страница 35: ...Parker Hannifin S p A S B C Division SLVDN User s Manual Page 35 of 181 5 7 Resolver connection diagrams ...
Страница 36: ...Parker Hannifin S p A S B C Division SLVDN User s Manual Page 36 of 181 5 8 Encoder connection ...
Страница 181: ......