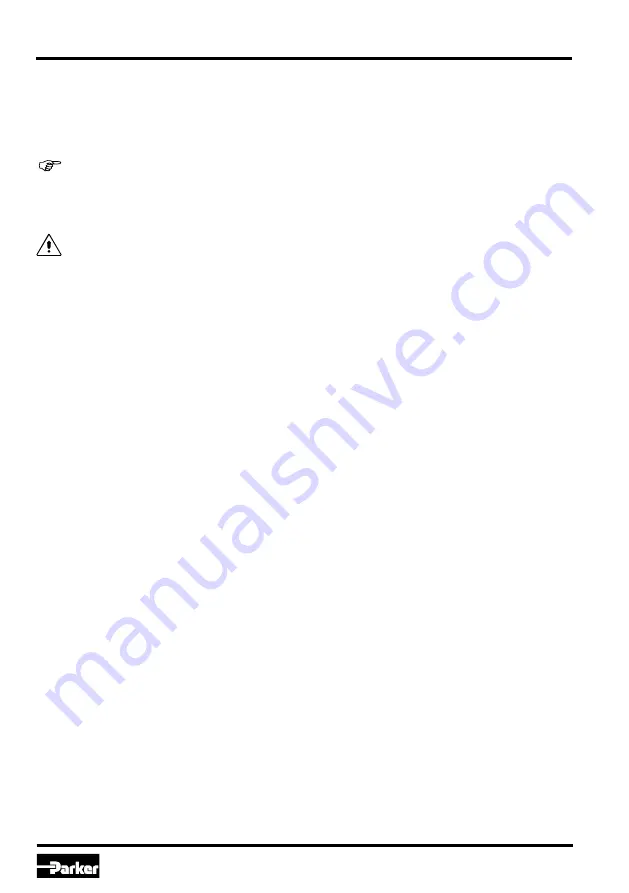
26
PWDXXA-40X_20 5715-677 UK.indd 26.01.17
Electronic for proportional DC valves
Series PWDXXA-40X
Operation Manual
Parker Hannifin Corporation
Hydraulics Group
Parker Hannifin Corporation
Hydraulics Group
5.5. Guideline for closed loop applications
Practical guidelines for the adjustment of the con-
trol parameters are summarized below. They are
divided into different application categories and
include common rules of thumb.
The commissioning of a closed loop systems
requires detailed knowledge of process
control technology. Therefore on-site works
support is recommended.
An incorrect wiring resp. parameter setting
may lead to malfunction and permanent
damaging of electronics and drive system!
5.5.1. Application: Closed loop systems for
position
Introduction
The electronics uses a feedback control loop which
automatically adjusts the electrical input to the
valve amplifier to move the drive to a commanded
position. At the heart of this feedback loop is a
digital controller which computes and updates the
signal output (set value output) every one milli-
second. The controller has adjustable coefficients,
which must be set by the user for the particular
application.
The controller provides a standard PID control ca-
pability plus extra features you can use to improve
the performance beyond the limits of PID.
Basic information for the control algorithm
Why tuning?
The controller can be used with valves that vary
greatly in flow capacity, frequency response, satu-
ration and deadband, with different kinds of load,
and with cylinders of any area and stroke. The
user must adjust the control coefficients for the
specific system. There are no fixed sets of values
for the controller coefficients that will handle every
situation well.
The electronics utilizes a “PID” controller for its
basic control action. The name PID comes from
the fact that the controller output is the sum of
three terms, called proportional (P), integral (I)
and derivative D), each with a user adjustable co-
efficient. The user software provides therefore the
parameters P16 (P), P17 (I) and P18 (D).
P - P16
This term provides an immediate output signal,
proportional to the error between commanded and
measured position. If this parameter is set too high,
sustained oscillations may occur. If it is set too low,
accuracy and speed of response may be poor.
I - P17
This term causes the output to change at a rate pro-
portional to the error in measured position over time
(integration time), in a direction to drive the steady
state error to zero. P17 is active within a window,
which might be adjustable by parameter P26. P26
shall be adjusted in the way that the window lies
near the final position or in the stationary range of
the drive. A too higher value of P17 causes oscil-
lations, in addition to which the selection of a too
lower value may result in a slow action.
D - P18
The D-term provides an output proportional to the
rate of change of the measured drive position. De-
pending on the polarity of the parameter prefix, this
term causes damping or acceleration. For hydraulic
drives this term should be set to a low value.
Parameter ranges
The controller provides two parameter ranges of
BASIC and EXPERT. The BASIC mode serves
for adjustment of the fundamental function param-
eters, while the application specific setting of the
control coefficients may be made via the
EXPERT
mode. The operating mode is selected via the
menu
OPTIONS.
Simple tuning of a position control loop
Before trying anything complicated, you should
adjust the proportional gain, accessible by P16.
In many cases this coefficient will be all you need,
and you will not have to bother with any of the other
control features. If you do need the other features,
you cannot adjust them properly without first ad-
justing the P-gain. Adjusting the P-gain is done by
setting all the other control coefficients P13 – 19 as
well as P26 and P27 to zero and increasing P16 to
the highest value that does not result in sustained
oscillations of the drive position.
Содержание PWD Series
Страница 38: ......