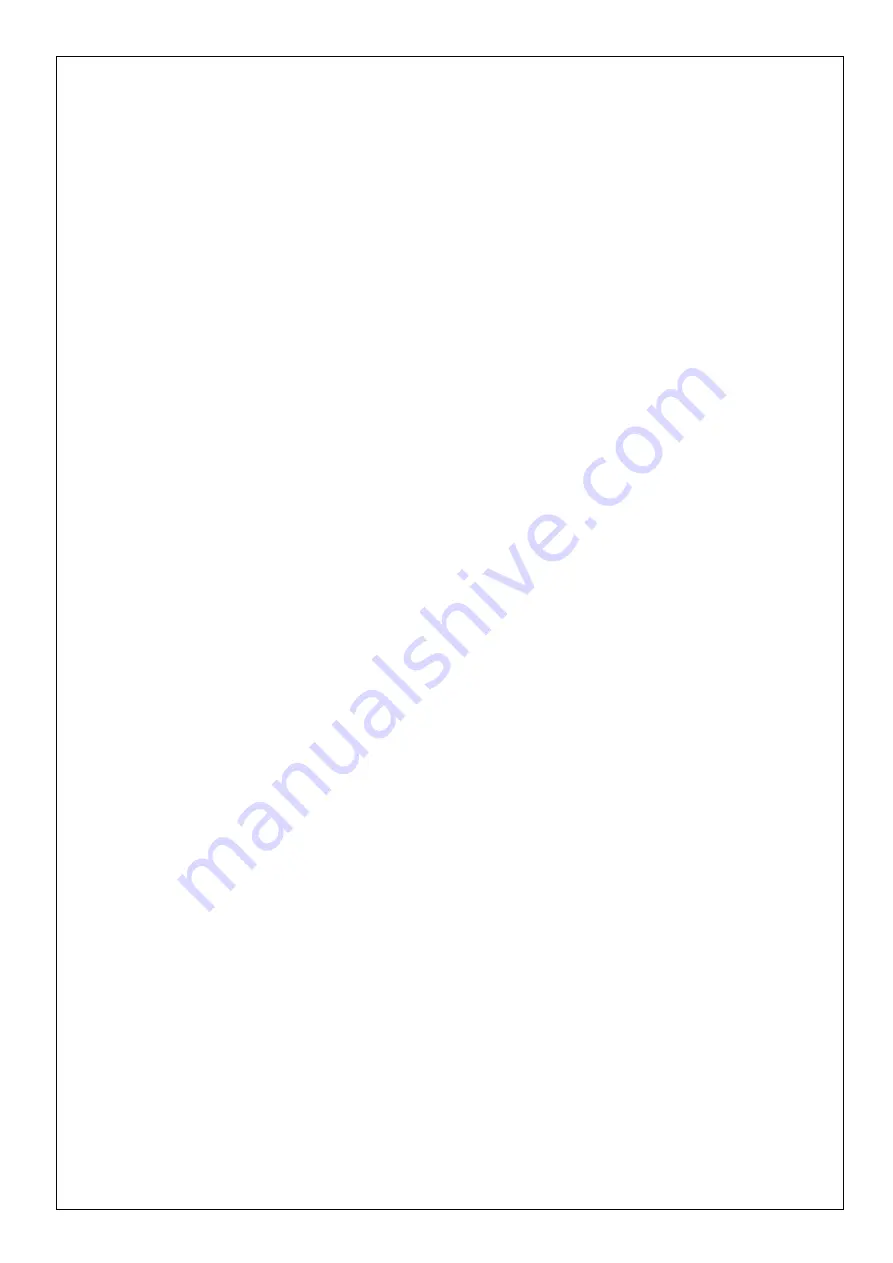
No. SX-DSV02472 -
56-
5)
How to Operate
When Pr 0.02 (Setup of real-time auto-gain tuning mode) is set to a value other than 0, control parameter is
automatically set according to Pr0.03 “Real-time auto-tuning machine stiffness setup”.
When the servo is ON, enter operation command. When the load characteristic is correctly estimated, Pr 0.04
Inertia ratio is updated. With certain mode settings, Pr 6.07 Torque command addition value, Pr 6.08 Positive
direction compensation value and Pr 6.09 Negative direction compensation value will be changed.
When value of Pr0.03 “Real-time auto-tuning machine stiffness setup” is increased, the motor responsiveness
will be improved. Determine the most appropriate stiffness in relation to the positioning setup time and vibration
condition.
Note) CCW direction is positive.
6)
Other cautions
[1] Immediately after the first servo-on upon start up; or after increasing Pr0.03 “Real-time auto-tuning machine
stiffness setup”, abnormal sound or oscillation may be generated until the load characteristics is stabilized. If
such abnormality lasts or repeats for 3 or more reciprocating operations, take the following countermeasures.
1) Lower the setting value of Pr0.03 “Real-time auto-tuning machine stiffness setup”.
2) Set Pr 0.02 Real-time auto-tuning setup to 0 to disable the real-time auto-tuning.
3) Set Pr 0.04 Inertial ratio to the calculational value of the equipment and set Pr 6.07 Torque command
addition value, Pr 6.08 Positive direction compensation value and Pr 6.09 Negative direction compensation
value to 0.
[2] When abnormal noise and oscillation occur, Pr 0.04 (Inertia ratio) or Pr 6.07 (Torque command additional
value), Pr 6.08 (Positive direction torque compensation value), Pr 6.09 (Negative direction torque
compensation value) might have changed to extreme values. Take the same measures as described in the setp 3)
above in these cases.
[3] Among the results of real-time auto-gain tuning, Pr 0.04 (Inertia ratio) and Pr 6.07 (Torque command
additional value), Pr 6.08 (Positive direction torque compensation value), Pr 6.09 (Negative direction torque
compensation value) will be written to EEPROM every 30 minutes. When you turn on the power again, the
auto-gain tuning will be executed using the latest data as initial values. If power is turned off within 30 minutes
after the end of tuning process, the result of the real-time auto-tuning is not saved. If the result is not saved,
manually write parameters to EEPROM and then turn off power.
[4] The control gain is updated when the motor is stopped. Therefore, if motor is not stopped because gain is
excessively low or commands are given continually in one direction, the change in Pr0.03 “Real-time
auto-tuning machine stiffness setup” may not be reflected. In this case, abnormal sound or oscillation may be
generated depending on the stiffness setting that is reflected after the motor stops.
After the stiffness setting is changed, be sure to stop the motor and check that the stiffness setting is reflected
before performing next operation.
Note) CCW direction is positive.
R1.05
Motor Business Division, Appliances Company, Panasonic Corporation