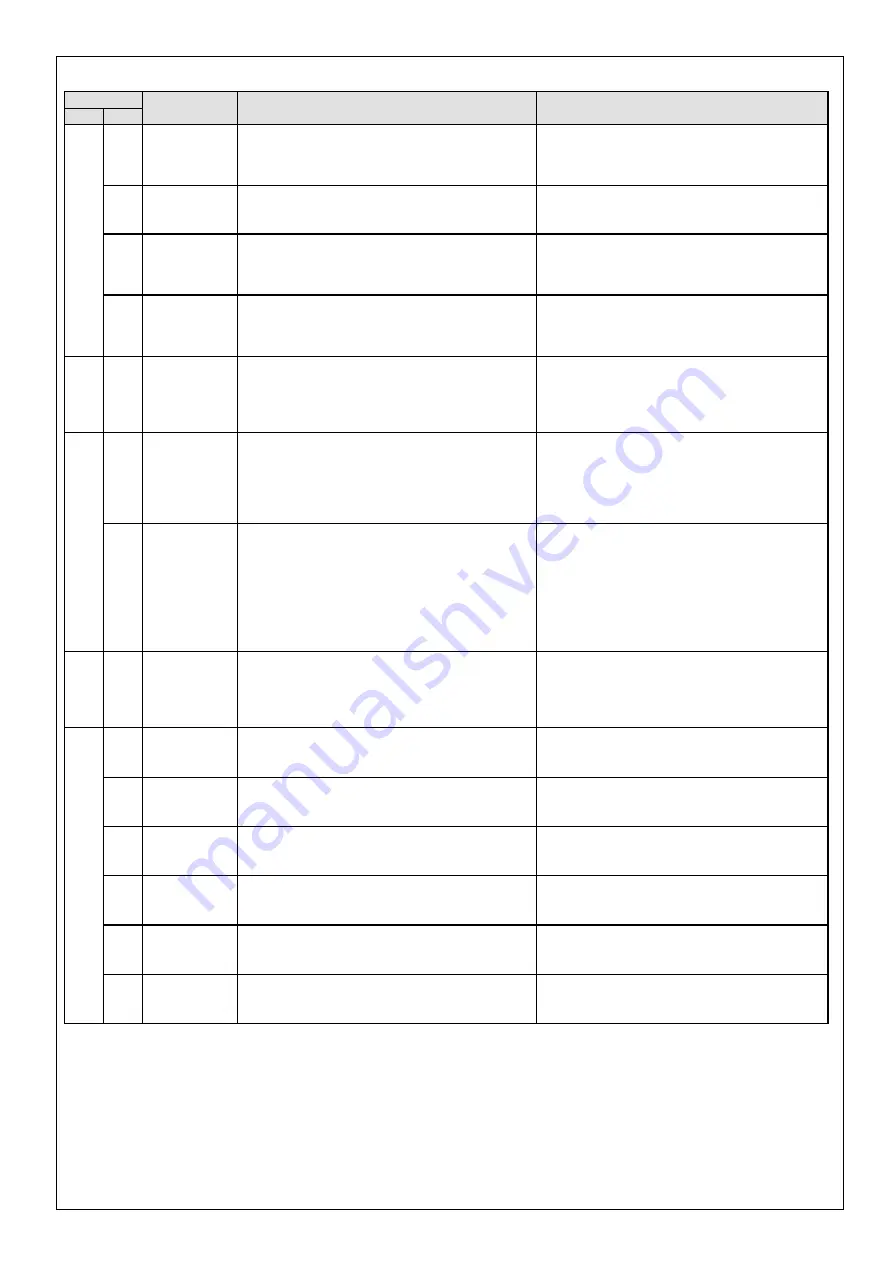
No. SX-DSV02472 -
108-
Error No.
Protective
function
Causes
Measures
Main
Sub
27
1
Absolute clear
protection
Multi-turn clear of absolute encoder is made through USB
communication (PANATERM).
Check if multi-turn clear of absolute encoder has been
made through USB communication.
Note: Checking is for the purpose of safety and not the
cause of error.
4
directive error
protection
Position command change amount exceeds a
predetermined value.
It checks whether the variation is not large, such as
the position command operation by the cyclic
synchronous position control (CSP).
6
Operation
commands
contention
protection
EtherCAT communication was established FFT which
operates with an amplifier simple substance, or during test
run execution.
Check whether EtherCAT communication has not been
established during FFT or test run execution.
7
Position
information
initialization error
protection
Servo-on was performed during reset processing.
It is checked whether it is servo-off during reset
processing.
28
0
Pulse regeneration
limit protection
(Not supported)
The output frequency of pulse regeneration has exceeded the
limit.
• Check the setup value of Pr0.11 (Output pulse counts per
motor revolution) and Pr5.03 (Denominator of pulse
output division).
• To disable the detection, set Pr5.33 (Pulse regenerative
output limit setup) to 0.
29
1
Counter overflow
protection 1
After turning on of control power in absolute mode, after
execution of attribute C parameter validation mode, after
FFT or after trial run: during position information
initialization process, absolute encoder (absolute scale)
position (pulse unit)/electronic gear ratio exceeded
±
2
31
(2147483648).
Check the operation range at the position of absolute
encoder (absolute scale) and electronic gear ratio.
2
Counter overflow
protection 2
Position deviation in unit of pulse has exceeded
±
2
29
(536870912).
• Check that the motor runs as per the position command
pulses.
• Check that the output toque has not saturated in torque
monitor.
• Make a gain adjustment.
• Set up maximum value to torque limit setting.
• Make a wiring connection of the encoder as per the
wiring diagram.
30
0
Safety input
protection
[Only special
product supports
this feature.]
Input photocoupler of both or one of safety input 1 and 2
is OFF.
Check wiring of safety input 1 and 2.
33
0
Input duplicated
allocation error 1
protection
Input signals (SI1, SI2, SI3, SI4) are assigned with two
functions.
Allocate correct function to each connector pin.
1
Input duplicated
allocation error 2
protection
Input signals (SI5, SI6, SI7, SI8) are assigned with two
functions.
Allocate correct function to each connector pin.
2
Input function
number error 1
protection
Input signals (SI1, SI2, SI3, SI4) are assigned with undefined
number. Or, logical setup is not correct.
Allocate correct function to each connector pin.
3
Input function
number error 2
protection
Input signals (SI5, SI6, SI7, SI8) are assigned with undefined
number. Or, logical setup is not correct.
Allocate correct function to each connector pin.
4
Output function
number error 1
protection
Output signals (SO1) are assigned with undefined number.
Allocate correct function to each connector pin.
5
Output function
number error 2
protection
Output signals (SO2) are assigned with undefined number.
Allocate correct function to each connector pin.
(To be continued)
R1.05
Motor Business Division, Appliances Company, Panasonic Corporation