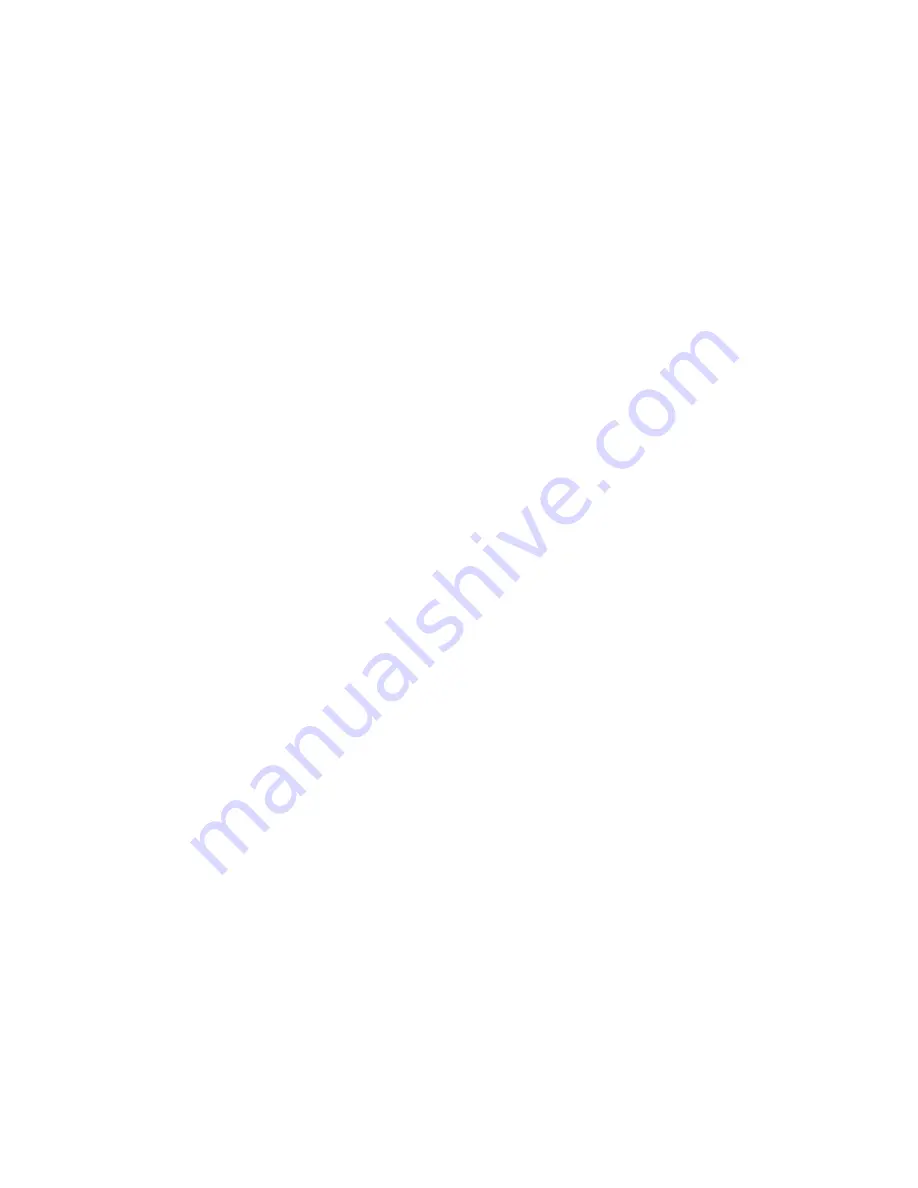
SECTION 3 INSTALLATION
35
3.1 CHASSIS
PLACEMENT
(cont.)
The first step in setting the chassis into place is to remove it from its shipping container. The next
step is to select an appropriate location for the unit. Key points to consider when locating the
chassis are:
1.
PROXIMITY TO THE LOAD - The power source should be located as close to the load as
possible. This helps to reduce distribution losses. These losses become more critical as
the output frequency increases.
2.
VENTILATION - The chassis requires good ventilation to adequately cool the internal
components. Airflow ranges from 100 to 600 CFM. A minimum of 12 inches front and
back clearance is recommended for proper operation of the Models 140-ASX, 160-ASX,
345-ASX, 360-ASX, 3120-ASX, and the 3120-ASX Magnetics Module. The air intake for
the Models 115-ASX, 120-ASX, 315-ASX, 320-ASX, and the 140/160/345/360-ASX
Magnetics Module is located on both sides near the front. A minimum clearance of two
inches on each side and 12 inches to the rear is required for proper operation of these
models.
When the chassis is placed in a 19 inch rack, it must be supported by either chassis slides or full
depth angle brackets. The front panel alone will not support the weight of the chassis. Chassis
slides are available from Pacific Power Source as a cost option. Call factory service for details.
After the location for the chassis is selected, verify that the input voltage of the power source is
correct (Input voltage is stated on the system ID label). If it requires changing, refer to Paragraph
3.3 for instructions.
Also check that the output voltage range is that which is desired. If not, reconfigure to the desired
form as directed by Paragraph 3.2.
After the input voltage form and output voltage range have been verified as correct, slide the
chassis into the rack or set it into its final position. Make input and output connections as stated in
paragraphs 3.3 and 3.4, respectively.
If either the Remote Interface (GPIB or RS-232) or External Sense feature is to be used, refer to
paragraphs 3.6 and 3.8 for connection
Содержание ASX series
Страница 2: ......
Страница 8: ......
Страница 21: ...SECTION 2 SPECIFICATIONS 13 2 1 2 OUTPUT POWER cont FIGURE 2 1 2 A MODEL 115 ASX OUTPUT DERATING CURVES ...
Страница 22: ...SECTION 2 SPECIFICATIONS 14 2 1 2 OUTPUT POWER cont FIGURE 2 1 2 B MODEL 120 ASX OUTPUT DERATING CURVES ...
Страница 23: ...SECTION 2 SPECIFICATIONS 15 2 1 2 OUTPUT POWER cont FIGURE 2 1 2 C MODEL 140 ASX OUTPUT DERATING CURVES ...
Страница 24: ...SECTION 2 SPECIFICATIONS 16 2 1 2 OUTPUT POWER cont FIGURE 2 1 2 D MODEL 160 ASX OUTPUT DERATING CURVES ...
Страница 25: ...SECTION 2 SPECIFICATIONS 17 2 1 2 OUTPUT POWER cont FIGURE 2 1 2 E MODEL 315 ASX OUTPUT DERATING CURVES ...
Страница 26: ...SECTION 2 SPECIFICATIONS 18 2 1 2 OUTPUT POWER cont FIGURE 2 1 2 F MODEL 320 ASX OUTPUT DERATING CURVES ...
Страница 27: ...SECTION 2 SPECIFICATIONS 19 2 1 2 OUTPUT POWER cont FIGURE 2 1 2 G MODEL 345 ASX OUTPUT DERATING CURVES ...
Страница 28: ...SECTION 2 SPECIFICATIONS 20 2 1 2 OUTPUT POWER cont FIGURE 2 1 2 H MODEL 360 ASX OUTPUT DERATING CURVES ...
Страница 29: ...SECTION 2 SPECIFICATIONS 21 2 1 2 OUTPUT POWER cont FIGURE 2 1 2 I MODEL 3120 ASX OUTPUT DERATING CURVES ...
Страница 69: ...SECTION 3 INSTALLATION 61 3 4 2 SPLIT PHASE OUTPUT cont FIGURE 3 4 2 1 SPLIT PHASE OUTPUT CONNECTION ...
Страница 70: ...SECTION 3 INSTALLATION 62 3 4 2 SPLIT PHASE OUTPUT cont FIGURE 3 4 2 2 SPLIT PHASE OUTPUT CONNECTION ...
Страница 72: ...SECTION 3 INSTALLATION 64 3 4 3 THREE PHASE OUTPUT cont FIGURE 3 4 3 1 THREE PHASE OUTPUT CONNECTION ...
Страница 73: ...SECTION 3 INSTALLATION 65 3 4 3 THREE PHASE OUTPUT cont FIGURE 3 4 3 2 THREE PHASE OUTPUT CONNECTION ...
Страница 76: ...SECTION 3 INSTALLATION 68 3 5 CONNECTION OF SYSTEM CONTROL UNIT SCU cont FIGURE 3 5 1 SCU CONNECTION ...