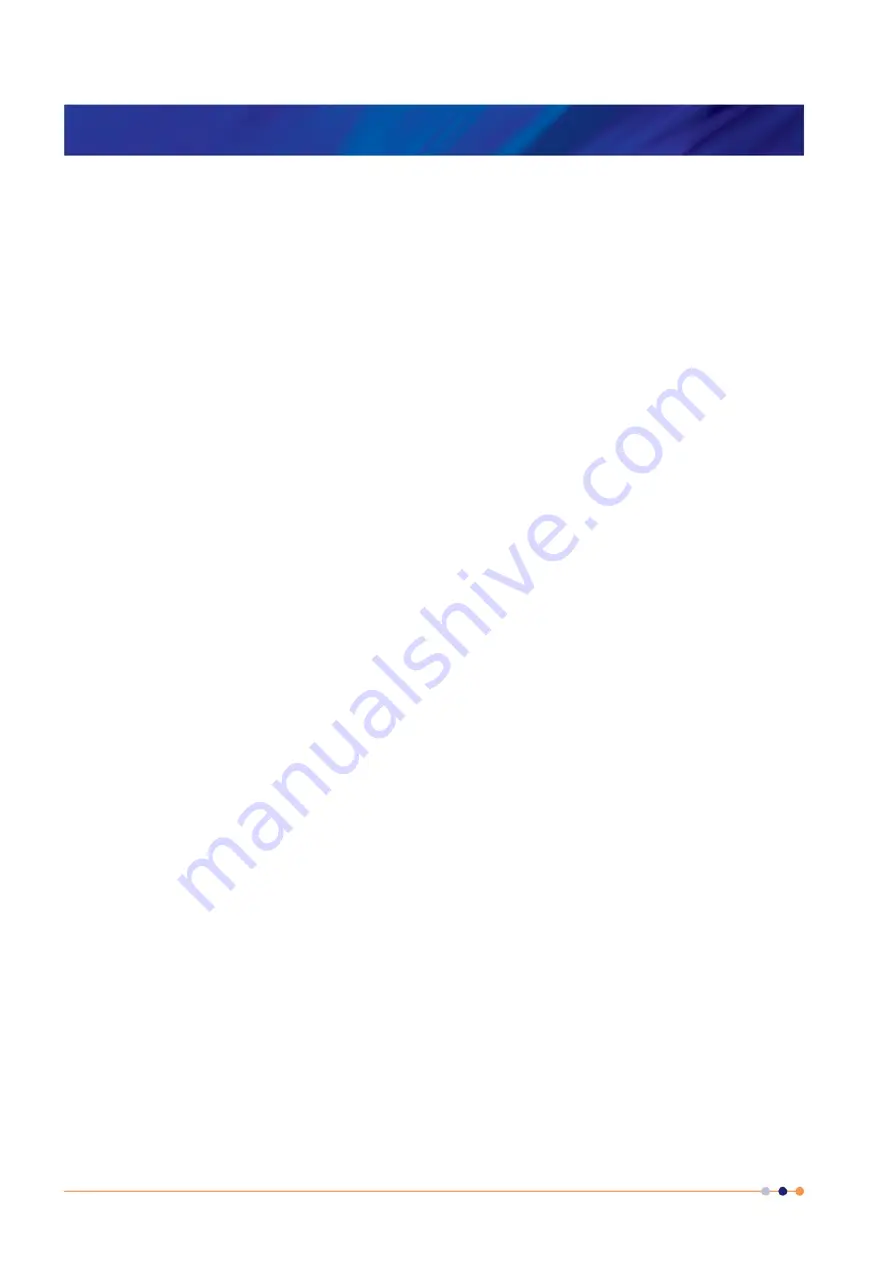
Operator's Manual
Issue 14
/
Mar 2016 / UMC0071
Mercury
iPS
©2016 Oxford Instruments NanoScience. All rights reserved.
Page
132
12 AUXILIARY I/O DAUGHTER BOARD
The auxiliary board combines digital inputs and outputs with a stepper motor drive and a PWM
signal. This board is generally used to operate system valves for flow control of gas and
cryogenic liquids.
12.1 Description of the auxiliary I/O board
12.1.1 Auxiliary I/O board functions
The optional auxiliary board performs the following functions:
It provides a stepper-motor drive and sense input. This can be used to drive an automatic
gas-flow control accessory such as an automatic needle valve on a helium transfer siphon or
variable temperature insert.
It provides digital inputs that can be used for various functions.
It provides digital outputs that can be used for various functions (e.g. control of a refill valve).
It provides a PWM signal proportional to the gas opening.
The auxiliary port connections are made via a 15-way D-socket on the iPS rear panel.
The outputs are open-collector transistors, and each can sink up to 500 mA from a maximum
supply voltage of +25 VDC. If the load is inductive, it is recommended that a diode is connected
across the load to absorb the stored energy.
Low-power loads can be driven directly from pin 15, which is connected to the unregulated 11 V
line via a diode and a fuse. Pin 15 can source a maximum current of 500 mA.
The input lines on the auxiliary port can be driven either by TTL levels or by contact closures
switching to +5 VDC. A 100 kohm pull-down resistor (to 0 V) is fitted to each input.
The AutoGFS sense input must be linked to +5 VDC when an AutoGFS iPS is connected.
If a temperature switch is fitted, it must be connected so that an over-temperature condition
pulls the input above +2.5 VDC. The internal 100 kohm resistor may be shunted by an external
resistor, if required to match the input to a sensor characteristic.