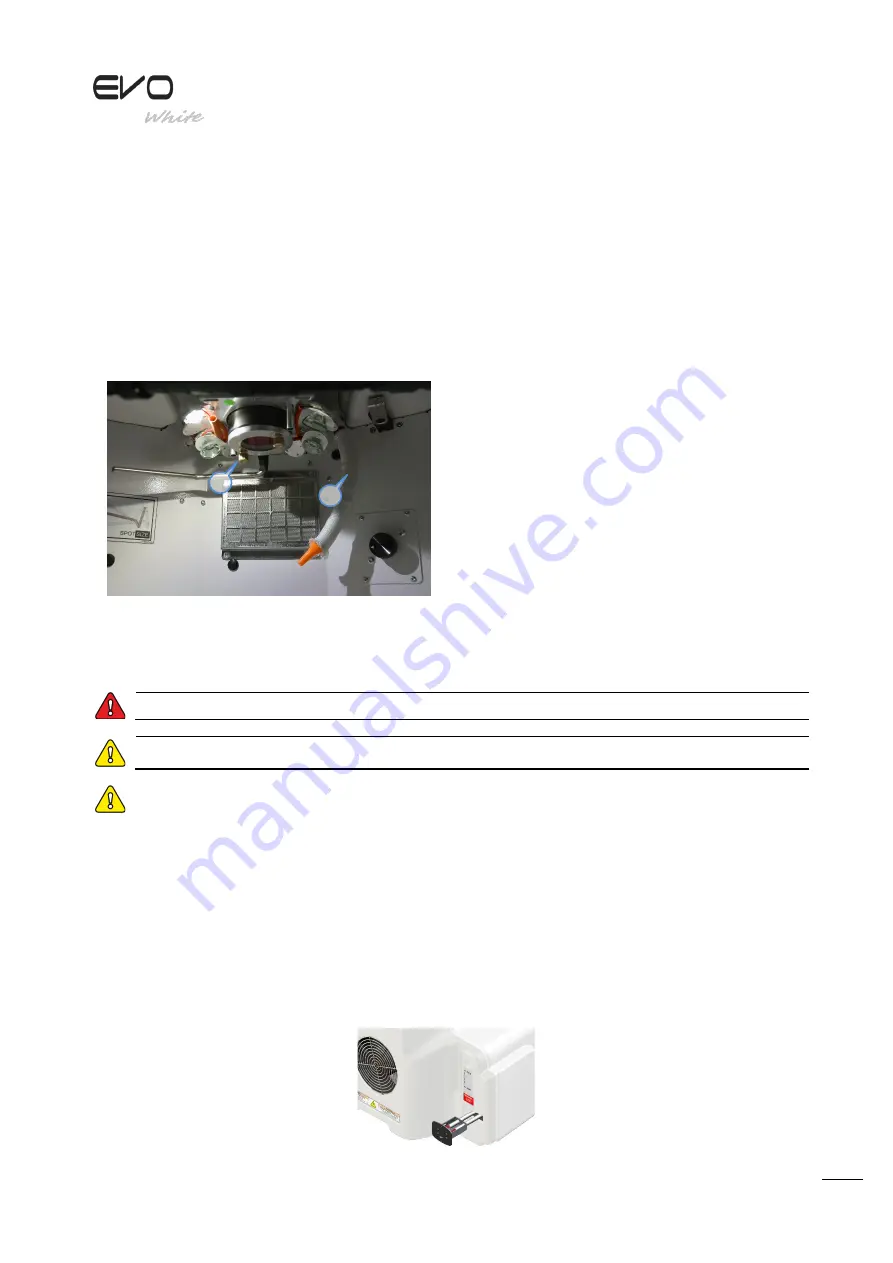
Operator Manual
Cha
pt
er
:
M
ai
nt
ena
nc
e
22
Operation of the accessories
Using the protection air/gas supplier
All of the Laser Welders are supplied with:
•
A flexible pipe to direct the protection air or gas (1).
•
A glass slide-holder without dispenser (2).
It is possible to use one system or the other for the supply of the protection gas or cooling air.
The outlet of the gas/air is controlled by a solenoid valve, which is activated by pressing the pedal if the "GAS" parameter present in the work
menu has a value set different to 0. (See "Work Menu" paragraph).
The maximum inlet pressure is 4 Bar. Over-pressure can damage the control solenoid valve.
Figure 1 – Example of use of the glass slide-holder without dispenser
This configuration is recommended for welding Silver or Gold
objects. It is advised to connect compressed air (maximum 4 bar) in
order to cool the metal during prolonged welding phases.
Maintenance
See the
Safety Information
chapter before proceeding.
Every maintenance operation, even small, relative to the Laser Welder and electric plant, requires the intervention of qualified
personnel.
Only original spare parts can be used. Using non-original spare parts exempts the manufacturer from any liability.
Periodic inspections
Check the integrity of the LASER radiation safety glass on the KG3 inspection window and the leather curtains for hand access to the welding
chamber daily; if they need replacement, contact the manufacturer. Use of the equipment with broken glass or without the curtains is
DANGEROUS and can damage health. Check the status and integrity of the safety labels and the data plate every six months. Contact the
manufacturer if they are discoloured or legible.
Checking the coolant
The machine has a liquid coolant system (double-distilled water). The liquid must be replaced at least once every 12 months, to prevent the
formation of alga and/or lime scale.
Open the rear compartment. Remove the caps present on the 2 small pipes. Prepare a recipient that can contain at least 2 litres of liquid.
2
1