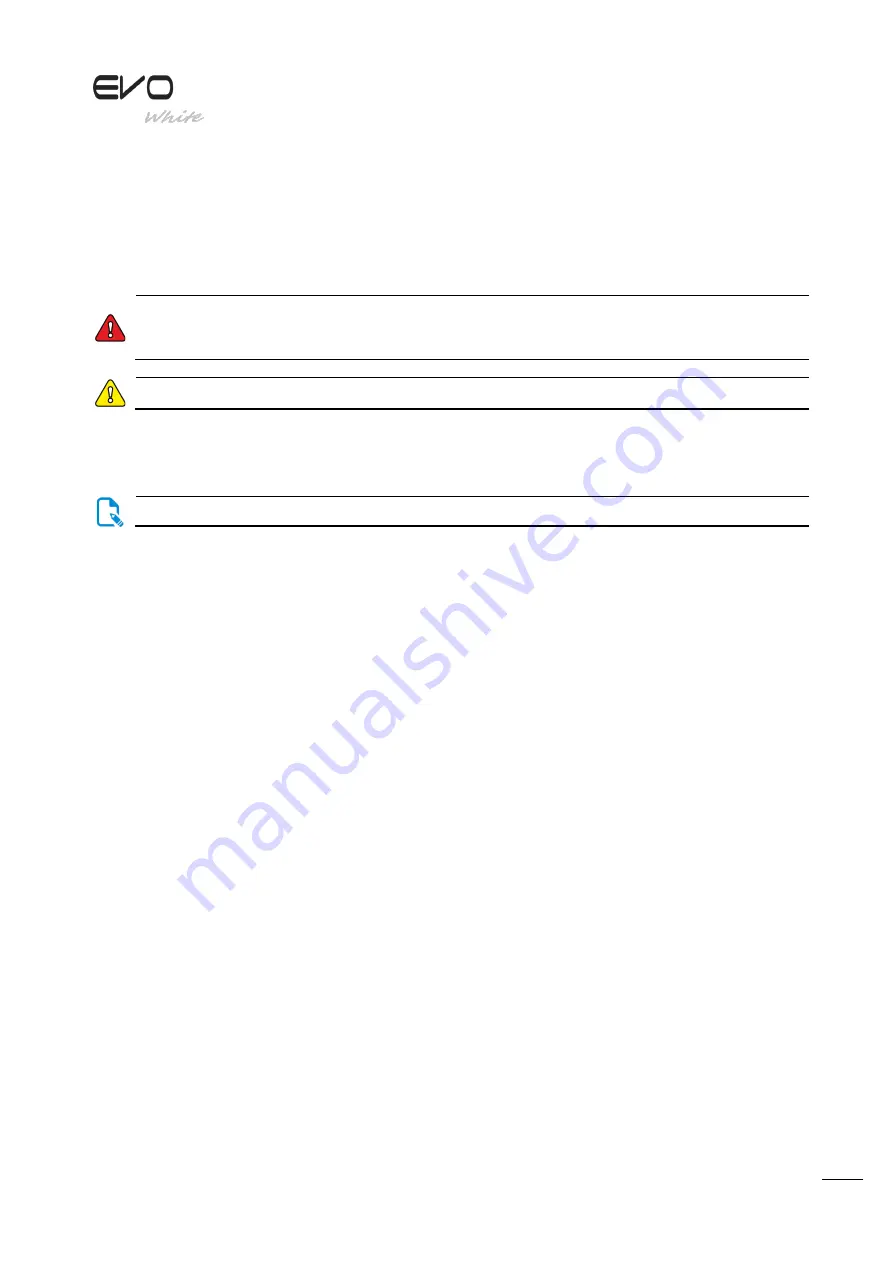
Operator Manual
Cha
pt
er
:
In
st
al
la
tio
n
11
Installation
Transport
The indications contained in this paragraph must be observed when transporting the Laser Welder for:
•
Storage
•
First installation
•
Relocation
The machine is normally supplied complete with special packaging that allows for easy transport and handling.
Crates should be handled with lifting vehicles with due care and strictly respecting the direction indicated on the packaging. Adopt
normal and logical precautions to avoid bumps and tipping.
When storing the welder in its packaging, do not tilt it, do not place it vertically and do not overturn it. If this is not the case, the
coolant may leak.
Protect equipment and any accessories from atmospheric agents. Water and moisture may oxidise some equipment parts,
irreversibly damaging them.
Unpacking
After removing the packaging, make sure the machine is integral by checking that there are no visibly damaged parts. If in doubt
DO NOT USE
THE EQUIPMENT
and contact the manufacturer.
All packaging items should be kept for future use
Positioning
The equipment must be placed in a position and environment suited to its intended use (use in a laboratory protected from atmospheric agents);
such placement must be carried out by qualified personnel.
Permissible temperature
from + 10° C to + 40° C
Permissible relative humidity
from 30% to 95%
Maximum height at sea level
2000 m
When positioning the LASER welder, keep in mind the following recommendations:
•
Position the equipment on a flat, stable surface that extends beyond the base of the machine in all directions, leaving more than 10 cm
between the rear panel and the wall.
•
Guarantee sufficient space to allow for adequate ventilation.
•
Avoid places subject to abrupt changes in temperature and humidity. Keep the device away from direct sunlight, strong light or heat
sources.
•
Do not position it near appliances that produce moisture, dust or heat (sanders, vaporisers, EDMs, ovens etc.).
•
Position it near an electrical outlet at a maximum distance of 1.5 metres.
Preliminary checks
The equipment is delivered with liquid in the cooling circuit. During the winter months, the liquid is not present inside the machinery. Rinsing is
carried out with a 20% alcohol solution for the inspection. This situation is signalled by the presence of a container of liquid coolant (demineralised
water) inside the package.
In this case, it is necessary to:
•
Perform two rinses in the following manner: fill the tank half full with the liquid supplied (with the machine off), turn the machine on
and access the "Test" menu and manually trigger the pump, wait one minute and then empty the tank.
•
Fill the tank completely with the machine off.