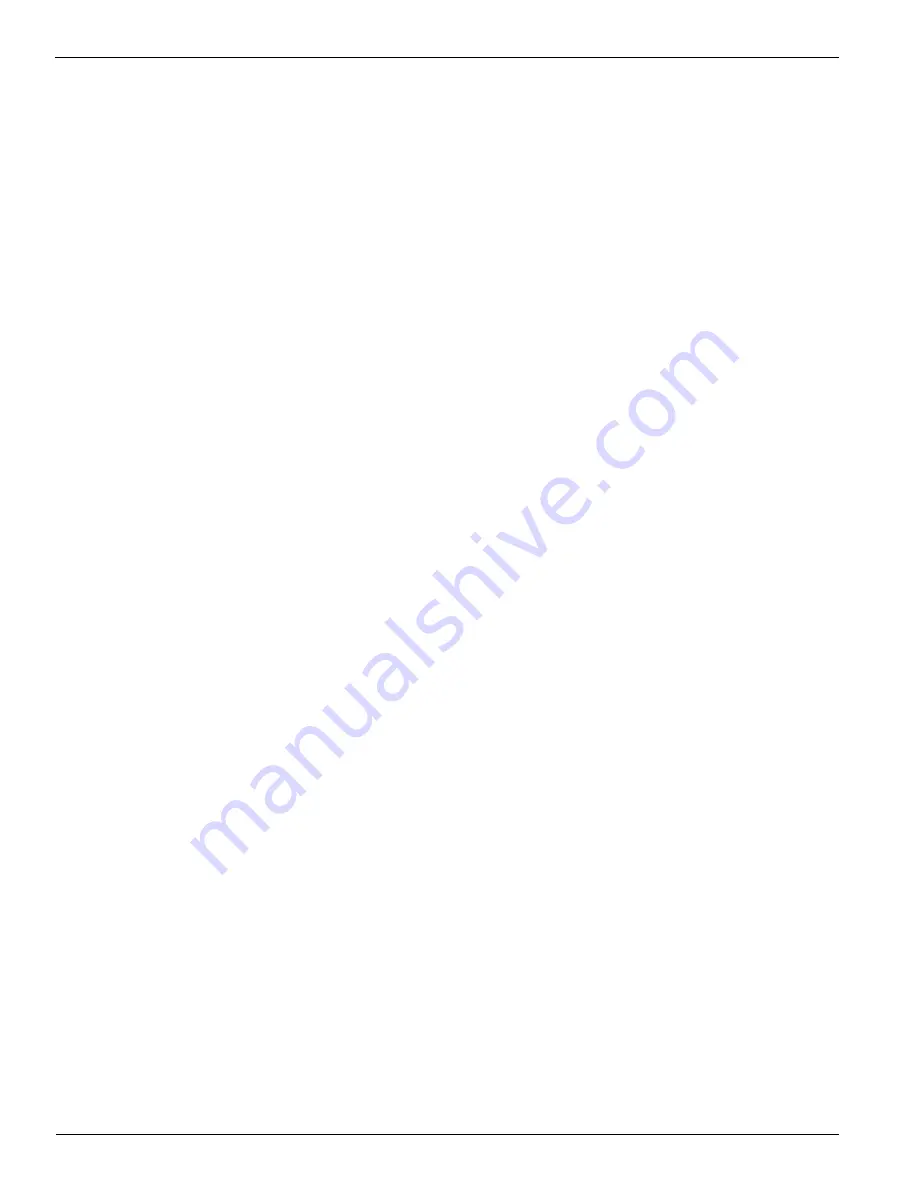
Océ |
-iv-
3010100686-A
US and Canadian Customers:
Océ Display Graphics Systems
Service: 1-800-456-3473
13231 Delf Place, Building #501
Fax: 604-232-3154
Richmond, British Columbia, Canada
Spares Orders: 1-800-295-6433 ext. 4
V6V 2C3
European Customers:
Océ Display Graphics Systems
Service: 44 (0) 1628-519720
6 Waltham Park
Service Fax: 44 (0) 1628-519589
Waltham Road
Spares Enquiries: 44 (0) 1628-519736
White Waltham
Spares Orders Fax: 44 (0) 1628-519751
Berkshire SL6 3TN
England
Asia Pacific Customers:
Océ Display Graphics Systems
Service:
81-3-5472-3066
Grand Palace Tamachi 601
Fax
: 81-3-5484-2071
4-9-18 Shibaura, Minato-ku
Tokyo, Japan 108-0023
Other:
Your regional distributor.
Customer Service Procedure:
When you call one of our customer service numbers you will be provided with telephone
technical support. Outside of office hours, you can leave a message and your call will be
returned the next working day. When you call, identify yourself as an Arizona T220
customer and provide the following information:
•
The serial number of your Arizona T220
•
Your company name and your name
•
Your telephone number
•
Nature of the problem
If we are unable to resolve your problem over the telephone, field engineers can be
dispatched to your site to conduct repairs. Service visits are paid for by the customer, either
under a maintenance agreement, by purchase order or prepayment. Time and material rates
are charged for any service not covered under a maintenance agreement. Before calling to
report a problem, gather as much information about the problem as possible and have it
ready to provide to the customer care center engineer. The more information you can
provide initially, the more quickly the problem can be corrected.
Содержание Arizona T220
Страница 1: ...Oc Arizona T220 User Guide Revision A March 2003...
Страница 2: ...Oc Display Graphics Systems 2002 All Rights Reserved...
Страница 6: ...Oc iv 3010100686...
Страница 10: ...Oc vi 3010100686 A...
Страница 32: ...Oc Media 3 22 3010100686 A...
Страница 37: ...Menu Structure 3 10 03 4 27 Figure 14 Maintenance Menu Tree...
Страница 67: ...Maintaining Print Quality 3 10 03 5 57...
Страница 79: ...Oc Printer Maintenance 6 68 3010100686 A...