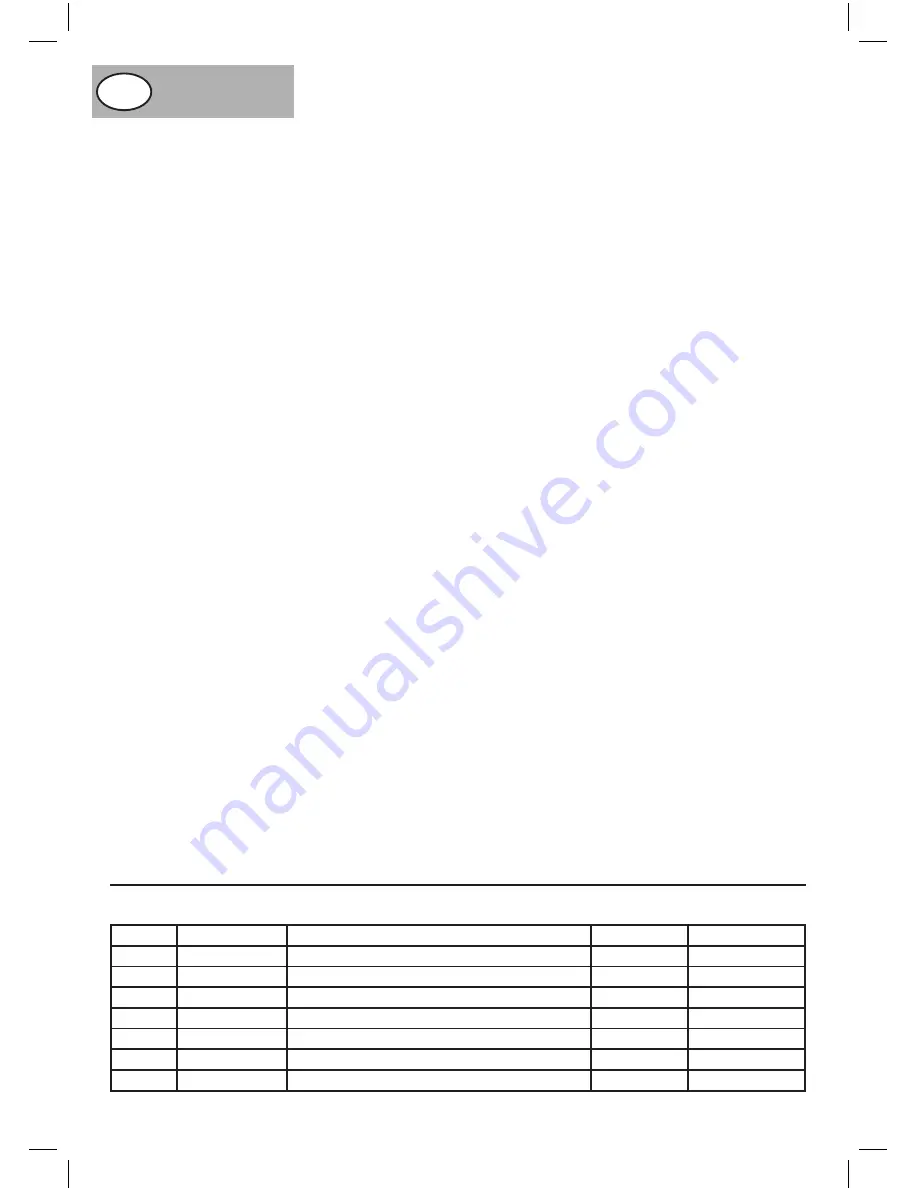
22
GB
found to be missing, the machine and its accessories should be
returned together in their original packaging to the retailer.
Do not throw the packaging away, keep it safe throughout the
guarantee period, then recycle if possible, otherwise dispose
of it by the proper means. Do not let children play with empty
plastic bags due to the risk of suffocation.
LOCATING THE MACHINE.
When determining where to locate or permanently fix the
machine, consideration must be given to the following points.
Is there a suitable mains outlet socket near by.
This machine must be permanently mounted and firmly secured
onto a bench that is at a suitable height, and that is strong and
stable enough to carry the weight of the machine. During this
process the machine must be levelled in all planes using a spirit
level.
PREPARING THE MACHINE.
This machine has been supplied with all bare metal surfaces and
accessories treated with an anti rusting protective coating which
must be removed before use. The ideal method of removing this
protective coating is to use a water based degreasing agent.
When all the protective coating has been removed the exposed
metal surfaces should be given a light coating of a general
purpose light machine oil.
FILLING THE GEARBOx.
To fill the gearbox, remove the four socket cap screws that
secure the gearbox cover plate (Pic.2) (2.1). Note that the
mating surfaces are coated with grease which acts as a seal.
Fill the gearbox with enough mineral based multigrade oil to be
visible half way up the sight glass (Pic.2) (2.2).. Replace the
gearbox cover plate ensuring that the mating surfaces are not
contaminated with swarf or other debris, apply a light coating of
grease and secure with the four socket cap screws.
Important Note:
Check the oil level in the oil reservoir by
viewing the oil level in the sight glass and top up when the oil
level is visible at the bottom of the sight glass.
RUNNING IN
Before using the machine it must be “Run In”, to ensure that
after transit and filling the gear box with oil, the oil is fully
distributed onto the gears. At the same time the “V” drive belt will
be conditioned and adjustment may be required to compensate
for any stretching of the “V” drive belt.
Set the gearbox selector levers to give the slowest spindle
speed (Pic.3) (3.1)., if difficulty is experienced in ensuring that
the gears are fully engaged, turn the chuck by hand until the
gears have fully meshed.
Ensure that the lead screw automatic drive selector lever is in
the dis-engaged position.
Plug the mains supply lead into a suitable mains supply socket
and switch on. Switch on the lathe. If any unusual noise or
vibration is experienced switch off the machine and investigate
the cause.
Allow the machine to run at slow speed for twenty minutes
checking for any abnormal conditions including unusual noise
or vibration. Increase the speed progressively until the machine
has run at all speeds for a minimum of five minutes.
Turn the machine off and remove the mains lead from the mains
supply socket. Allow the machine to stand for approximately
fifteen minutes. After this time check the machine for oil leaks
and areas of excessive temperature.
Check the movement of all the slide ways by turning the hand
wheels, ensuring that the slide ways travel over their full range
of movement. If movement is stiff or obstructed re-lubricate
the lubrication points and make any required adjustments to
the slide ways. To adjust the slide ways (see example Pic.4)
slacken the appropriate locking nuts (Pic.4) (4.1) and turn the
adjustment screws until the movement of the slide way is free
and without any play. Re-tighten the lock nut ensuring that the
adjustment screws do not move.
CHECKING THE “V” DRIVE BELT.
To check that the “V” drive belt is correctly tensioned, using
moderate pressure, press your finger onto the centre of the
drive belt between the two pulleys. The drive belt should move
approximately 13mm (Pic.5) (5.1).. If the “V” drive belt has
stretched during the running in period and moves more than
13mm adjustment will be required. Adjustment of the belt
tension is achieved via the adjusting screw and nuts located at
the top of the motor mounting plate (Pic.6) (6.1).
LUBRICATION.
When the running in period has been successfully completed,
lubrication of all other moving parts must be completed. using
mineral based multigrade oil. For lubrication requirements see
(Pic.7) and the lubrication chart 1.
CHART 1.
Ref:
Description
Lubricate
Method
Frequency
7.1
Gearbox
Gears & Bearings
Spray
Every 60 days
7.2 x 4
Saddle
Longitudinal slide ways
Oil can
Every day
7.3 x 3
Compound slide
Slide ways & operating screw thread
Oil can
Every day
7.4 x 2
Tail stock
Screw thread and barrel
Oil can
Every day
7.5 x 3
Lead screw
Head & tail stock supports & lead screw thread
Oil can
Every day
7.6 x 2
Cross slide
Slide ways and operating screw thread.
Oil can
Every day
7.7
Thread gears
Gears
Light spray
Every day
Содержание MC550
Страница 7: ...7 10 8 7 4 35 36 11 1 2 3 21 5 6 19 20 26 22 23 25 24 16 9 14 12 13 27 30 31 33 34 27 32 28 1 ...
Страница 8: ...8 4 2 2 5 3 7 6 2 1 2 2 3 1 4 1 4 1 5 1 6 1 7 5 7 5 7 5 7 4 7 3 7 2 7 2 7 7 7 1 7 6 ...
Страница 10: ...10 1 6 01 0 5 0 15 15 2 15 15 2 15 1 15 3 15 4 15 5 ...
Страница 41: ...41 PL ...
Страница 89: ...89 ...
Страница 90: ...90 ...