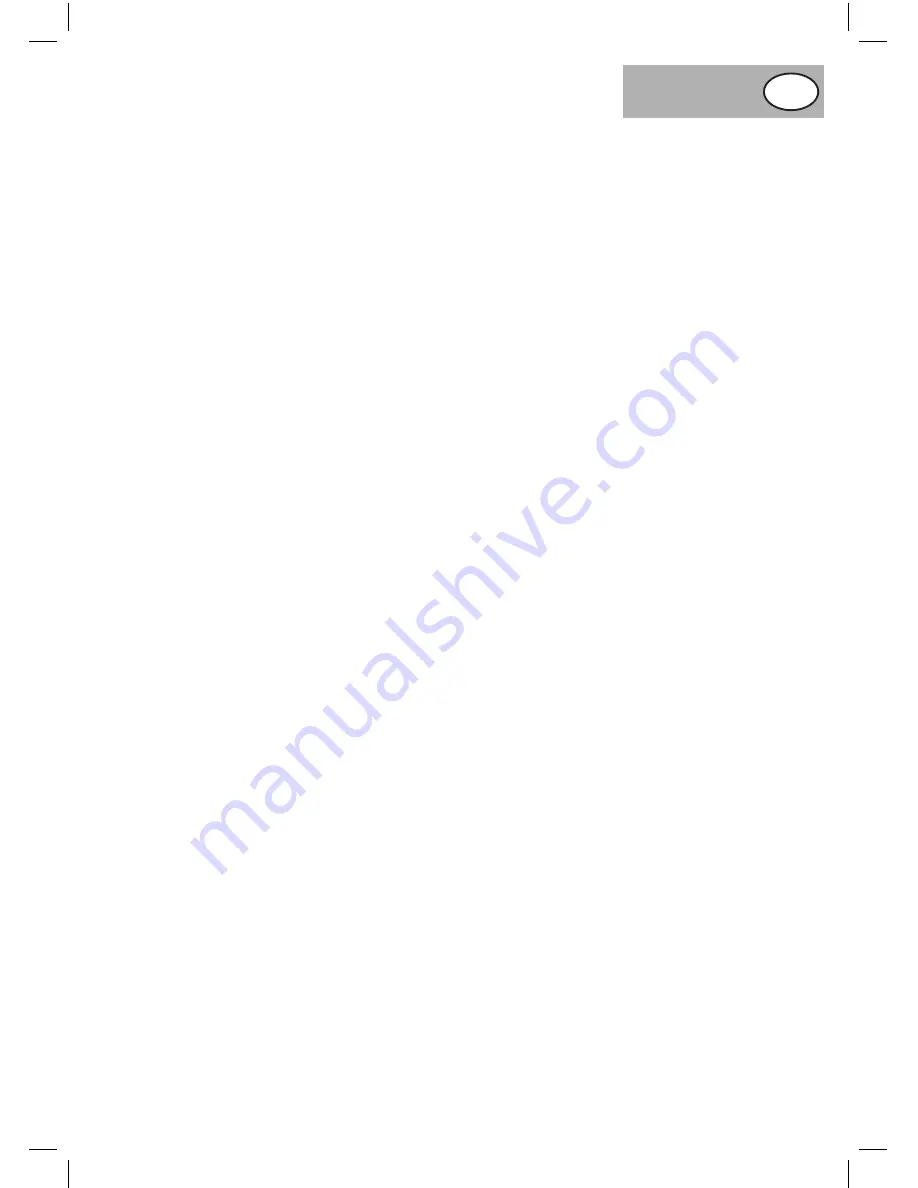
23
GB
OPERATING INSTRUCTIONS.
CHUCK FITTING AND REMOVAL (PIC.8)
The chuck supplied with the machine is a three jaw self centring
chuck. The chuck is secured to the face plate with three socket
cap screws (Pic8) (8.1). Protect the lathe bed with a cloth or
a piece of wood. Because the space between the back of the
face plate and the head stock is restricted you will need to
use a cut down hex key. Remove the three socket cap screws
and remove the chuck. Re-fitting the chuck is a reversal of the
removal procedure.
CHUCK JAW CHANGING (PIC.9).
There are two types of chuck jaw that can be used with the three
jaw self centring chuck, for gripping the work piece externally
or for hollow work pieces internally. The jaws are located into
the chuck body by a “Tee” slot (Pic9) (9.1) and are operated
by a spiral gear (Pic9) (9.2) locating into a number of grooves
machined into the back face of each jaw (Pic9) (9.3). As the
chuck key is rotated the spiral gear rotates opening or closing
the jaws. When changing the jaws it is important that they
are removed in the correct order. Each jaw is identified with a
number stamped into its surface and corresponds with numbers
stamped into the jaw the locating groove in the body of the chuck
(Pic9) (9.4). When removing the jaws they must be removed in
the sequence (3-2-1). When fitting the jaws they must be fitted
in reverse order (1-2-3). When the jaws have been fitted, fully
close the jaws and check that they are all correctly located. If the
gripping surfaces do not meet together, remove the jaws and
repeat the procedure.
COMPOUND SLIDE (PIC.10).
The compound slide can be adjusted to allow the turning of
angled surfaces and to allow the correct positioning of the
turning tool in relationship to the work piece. To set the angle
required, slacken the two securing nuts (Pic10) (10.1), set the
required angle using the graduated scale (Pic10) (10.2) and re-
secure the two nuts.
TOOL POST (PIC11)
The tool post is mounted on top of the compound slide and can
accommodate up to four different turning tools (Pic11) (11.1).
The tool post can be rotated and locked into any position to
change to a different turning tool and to allow the correct
positioning of the turning tool in relationship to the work piece by
using the clamping lever located on top of the tool post (Pic11)
(11.2).
LEAD SCREW OPERATION (PIC.12).
The lead screw (Pic12) (12.1) performs two functions. It is
primarily used when turning screw threads. When the screw
thread gear train is set up for a chosen thread size engagement
of the lead screw using the lead screw engagement lever (Pic12)
(12.2) allows the longitudinal fed to operate automatically at the
correct speed to cut the chosen screw thread.
Note:
The lead screw requires manual dis-engagement at the
end of each screw thread cutting pass.
The second function is to provide automatic longitudinal drive to
the saddle when performing parallel turning. The speed of travel
will be determined by the screw cutting gear train set up and the
rotational speed of the main spindle.
TAIL STOCK (PIC13).
The tail stock is used to support long or thin work pieces, the
spindle is machined with an internal Morse taper.
and can accommodate a number of different types of Morse
taper centres, drilling chucks and other attachments that have a
Morse taper fitting (Pic13) (13.1). Centres and other accessories
can be removed by turning the hand wheel to fully retract the
tail stock barrel, additional pressure may be required at the end
of travel to release the taper. The tail stock can also be “Off
Set” to allow taper turning over longer lengths than cannot be
machined using the compound slide.
TAIL STOCK TAPER TURNING (PIC.14)
To set the tail stock for taper turning, slacken the tail stock
clamping nut (Pic14) (14.1) determine the direction the tail stock
has to be moved to give the desired taper. Slacken the off set
adjusting screw on the base of the tail, in the direction that the
tail stock is to be moved (Pic14) (14.2). By tightening the other
off set adjusting screw and observing the graduated scale at
the rear of the tail stock the amount of taper can be determined
(Pic14) (14.3).
Note.
Most good metal turning books will give the mathematical
formula for calculating the correct tail stock off set for a given
taper over a given length. If this formula is not available then
the trial and error method on a scrap piece of material will have
to be used.
Warning.
When using the tail stock off set facility for taper
turning do not over tighten the chuck to prevent straining the
chuck jaws.
THE “MORSE TAPER” SYSTEM.
This lathe can accommodate various sizes of centres, drill
chucks, drill bits and other accessories. Industry uses the
Morse taper system to fit accessories into drive shaft or spindle.
The “Morse Taper” system is a method of securing an external
(Male) taper securely into an internal (female) tapered shaft or
barrel. These tapers are referred to as self holding because
they stay in place when correctly seated. This system allows
the easy changing of dead and live centres, drill chucks, drill
bits and other accessories. The internal and external tapers are
ground at an angle that allows the two tapers to lock together.
Various accessories including, centres, drill chucks, drill bits and
other accessories including adaptor sleeves to accommodate
various size of “Morse Taper” shank can be obtained.
Note:
For the “Morse Taper” system to work correctly the
internal and external tapers must not be damaged and must be
kept thoroughly clean.
Caution.
To prevent damage to the accessory or injury to the
operator carefully hold the accessory with a thick cloth or wear
welders type gloves.
Содержание MC550
Страница 7: ...7 10 8 7 4 35 36 11 1 2 3 21 5 6 19 20 26 22 23 25 24 16 9 14 12 13 27 30 31 33 34 27 32 28 1 ...
Страница 8: ...8 4 2 2 5 3 7 6 2 1 2 2 3 1 4 1 4 1 5 1 6 1 7 5 7 5 7 5 7 4 7 3 7 2 7 2 7 7 7 1 7 6 ...
Страница 10: ...10 1 6 01 0 5 0 15 15 2 15 15 2 15 1 15 3 15 4 15 5 ...
Страница 41: ...41 PL ...
Страница 89: ...89 ...
Страница 90: ...90 ...