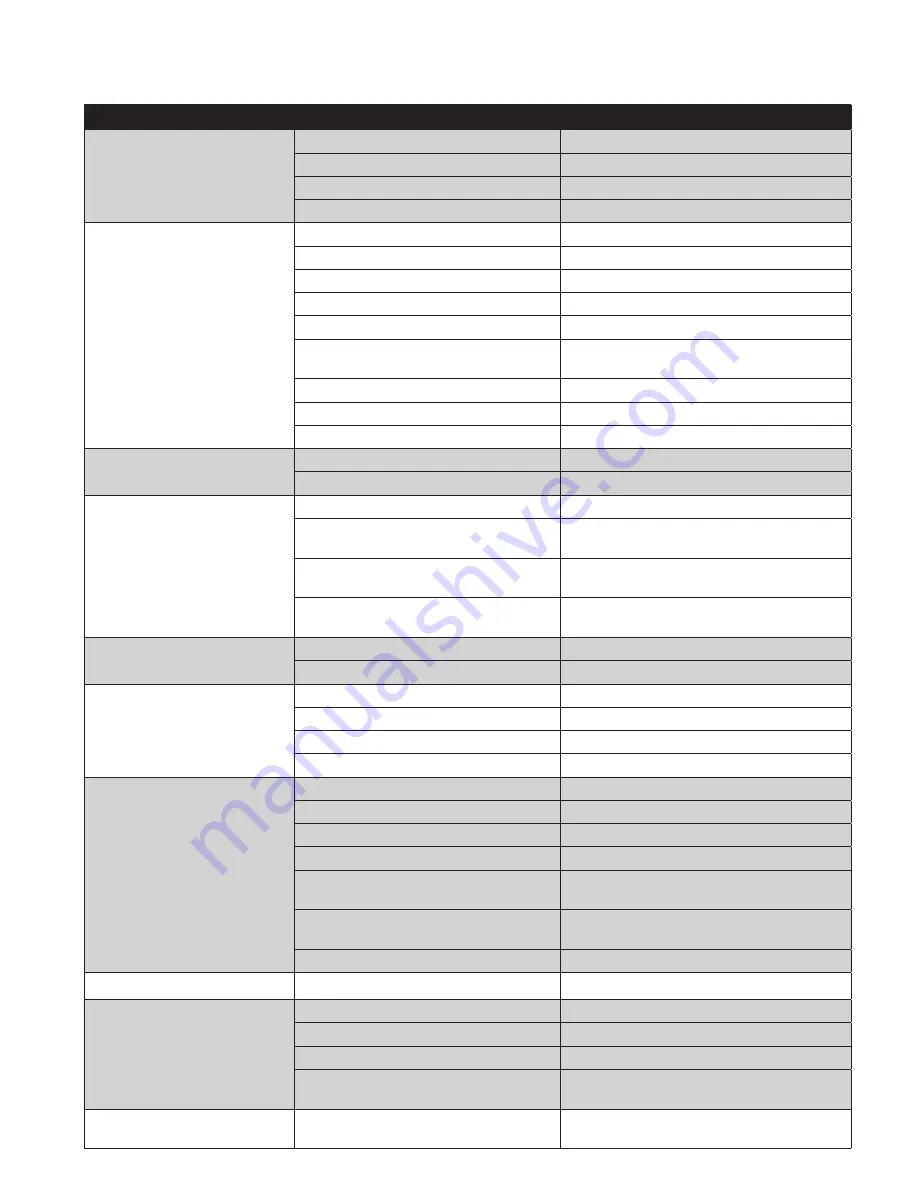
32
Issue
Possible Cause
Possible Solution
A.
Unit fails to initiate a regeneration
cycle.
1. No power supply.
Check electrical service, fuse, etc.
2. Defective circuit board.
Replace faulty parts.
3. Power failure.
Reset time of day.
4. Defective meter.
Replace turbine meter.
B.
Water is hard.
1. By-pass valve open.
Close by-pass valve.
2. Out of salt or salt level below water level.
Add salt to tank.
3. Plugged injector / screen.
Clean parts.
4. Flow of water blocked to brine tank.
Check brine tank refill rate.
5. Hard water in hot water tank.
Repeat flushing of hot water tank required.
6. Leak between valve and central tube.
Check if central tube is cracked or o-ring is damaged.
Replace faulty parts.
7. Internal valve leak.
Replace valve seals, spacer, and piston assembly.
8. Reserve capacity setting too low.
Increase reserve capacity.
9. Not enough capacity.
Increase salt dosage.
C.
Salt use is high.
1. Refill time is too high.
Check refill time setting.
2. Defective flow control.
Replace.
D.
Low water pressure.
1. Iron or scale build up in line feeding unit.
Clean pipes.
2. Iron build up inside valve or tank.
Clean control and add resin cleaner to clean bed. Increase
regeneration frequency.
3. Inlet of control plugged due to foreign
material.
Remove piston and clean control valve.
4. Deteriorated resin. (Maybe caused from high
chlorine or chloramines.)
Re-bed unit. Consider adding carbon pre-treatment.
E.
Resin in drain line.
1. Air in water system.
Check well system for proper air eliminator control.
2. Incorrect drain line flow control (DLFC) button.
Check for proper flow rate.
F.
Too much water in brine tank.
1. Plugged injector or screen.
Clean parts.
2. Valve not regenerating.
Replace circuit board, motor, or control.
3. Foreign material in brine valve.
Clean parts.
4. Unit not drawing brine.
Check for vacuum leak in brine line connections.
G.
Unit fails to draw brine.
1. Drain line flow control is plugged.
Clean parts.
2. Injector or screen is plugged.
Clean parts.
3. Inlet pressure too low.
Increase pressure to 25 PSI.
4. Internal valve leak.
Replace seals, spacers, and piston assembly.
5. Safety valve closed.
Check for leak in brine line connections. Replace safety float
assembly.
6. Vacuum leak in brine line.
Check for leak in brine line connections. Tighten all connec-
tions.
7. Drain line has kink in it or is blocked.
Check drain line.
H.
Valve continuously cycles.
1. Defective position sensor PCB.
Replace faulty parts.
I.
Flow to drain continuously.
1. Valve settings incorrect.
Check valve settings.
2. Foreign material in control valve.
Clean control.
3. Internal leak.
Replace seals, spacers, and piston assembly.
4. Piston is stuck in position. Motor may have failed or
gears have jammed or disengaged.
Check for power to motor. Check for loose wire. Check for
jammed gears or gears disengaged. Replace faulty parts.
J.
Valve makes beeping sound.
1. The piston has not advanced to the next cycle
position properly.
Check for power to motor. Check for loose wire. Check for
jammed gears or gears disengaged.
TROUBLE SHOOTING