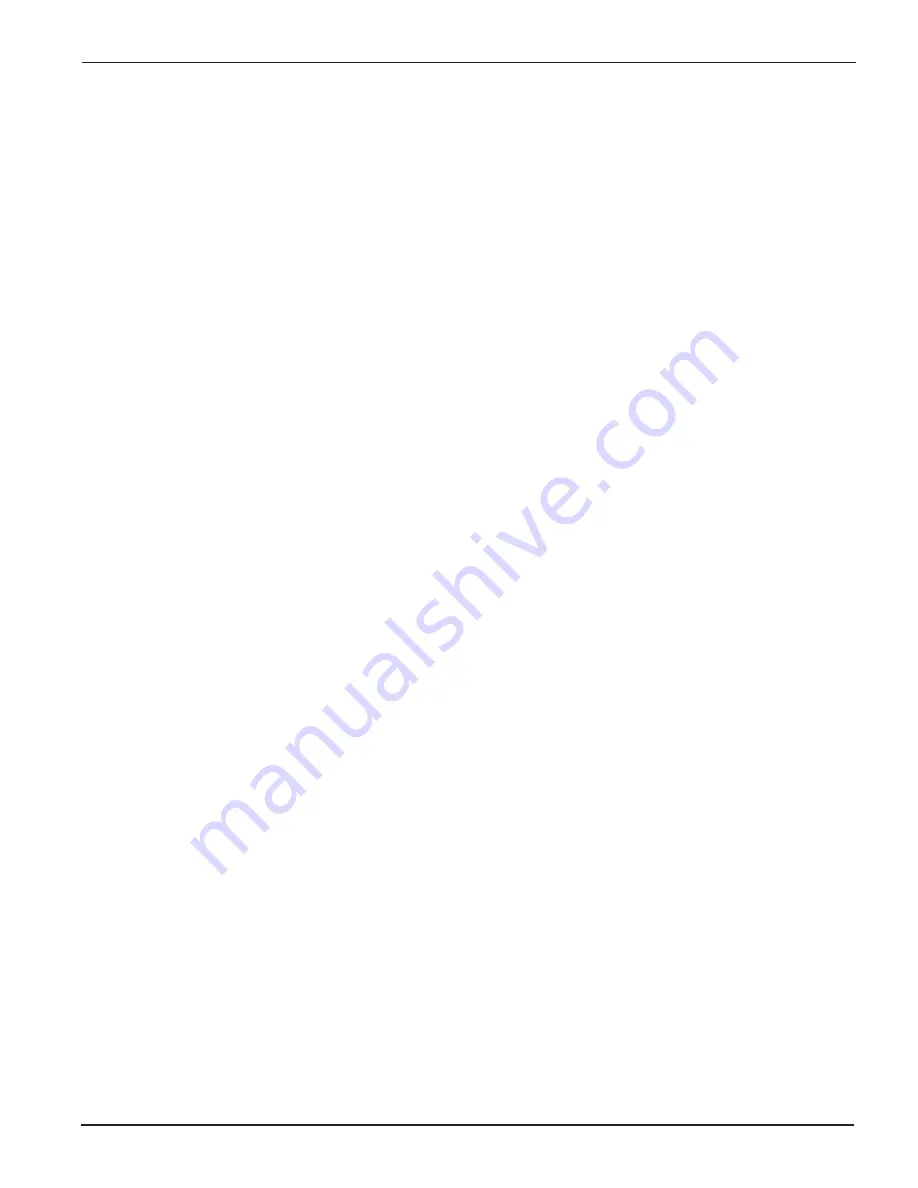
83
Glossary
IMS-MN-LMDA42C_A.pdf
LMD CANopen
M
Microstepping
: A control electronic technique that proportions the current in a stepper motor’s
windings to provide additional intermediate positions between poles. Produces smooth rotation
over a wide range and high positional resolution. Typically, step resolutions range from 400 to
51,200 steps per shaft revolution.
Motor Phase Current
: The available torque of a stepper motor is determined by the motor
phase current. The higher the motor phase current the higher the torque.
N
NEMA
: The acronym for the National Electrical Manufacturer’s Association, an organization that
sets standards for motors and other industrial electrical equipment.
O
Open Loop System
: An open loop motion control system is where no external sensors are used
to provide position or velocity feedback signals, such as encoder feedback of position.
Opto-Isolated
: A method of sending a signal from one piece of equipment to another without
the usual requirement of common ground potentials. The signal is transmitted optically with
a light source (usually an LED) and a light sensor (usually a photo-sensitive transistor). These
optical components provide electrical isolation.
P
Parameter
: Device data and values that can be set by the user.
PLC
: Programmable logic controller
Position Make-up
: When active, the position make-up can correct for position errors occurring
due to transient loads. The lost steps may be interleaved with incoming steps, or reinserted into
the profile at the end of a move.
Power Stage
: The power stage controls the motor. The power stage generates currents for
controlling the motor on the basis of the positioning signals from the controller.
Q
Quick Stop
: Function used to enable fast deceleration of the motor via a command or in the
event of a malfunction.
R
Resolution
: The smallest positioning increment that can be achieved.
Resonance
: The frequency that a stepper motor system may begin to oscillate. Primary
resonance frequency occurs at about one revolution per second. This oscillation will cause a
loss of effective torque and may result in loss of synchronism. The designer should consider
reducing or shifting the resonance frequency by utilizing half step or micro-step techniques or
work outside the primary resonance frequency.
Rotor
: The moving part of the motor, consisting of the shaft and the magnets. These magnets
are similar to the field winding of a brush type DC motor.
Rotor Inertia
: The rotational inertia of the rotor and shaft.
RS485
: Fieldbus interface as per EIA-485 which enables serial data transmission with multiple
devices.