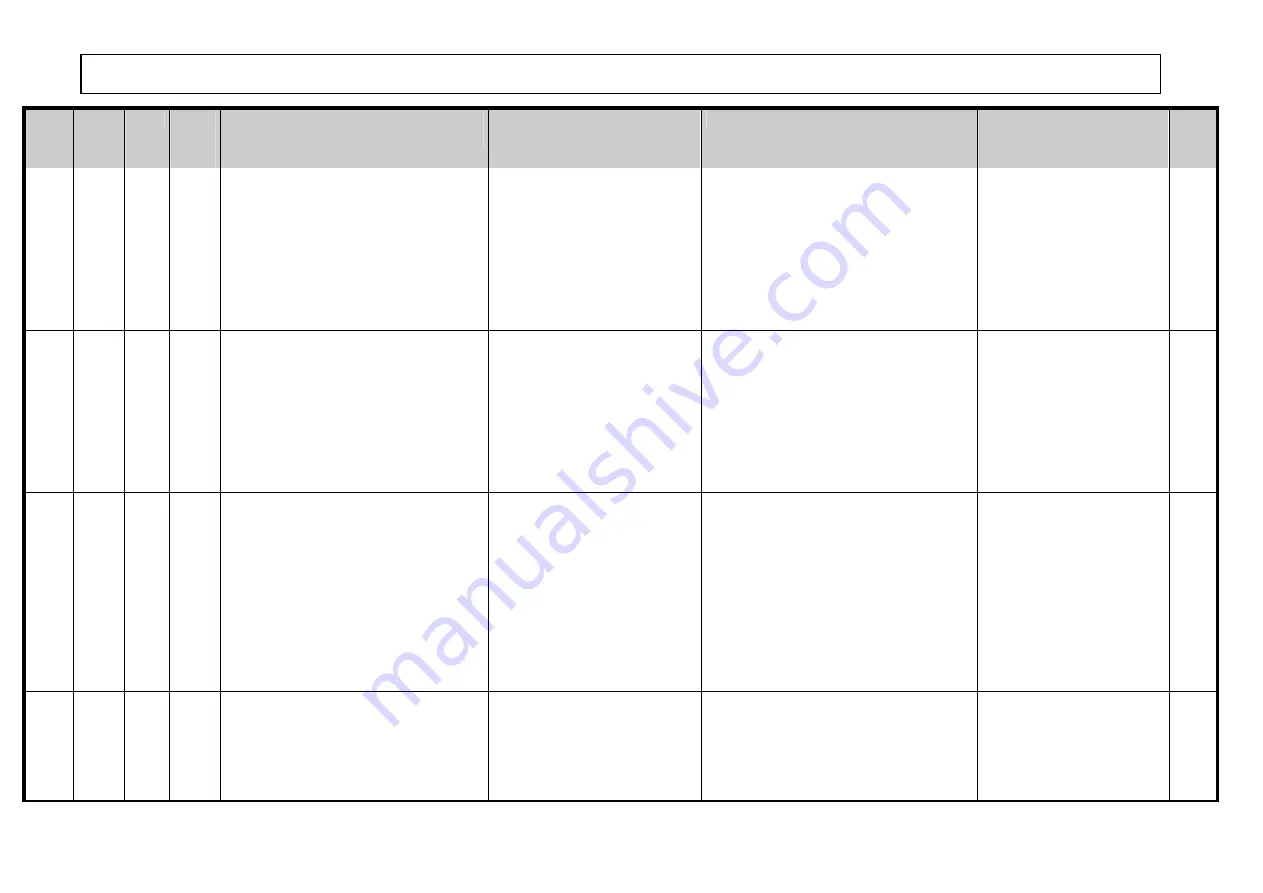
ZF Friedrichshafen AG
description of fault codes for ERGO-Control
97-09-18
TE-AB
F:\15_Kunden_Informationen\FC_Liste\Fc_37_V920.doc
Seite 24 von 58
Fault
Code
(hex)
SPN FMI Int.
Code
(dec)
MEANING OF THE FAULT CODE
possible reason for fault detection
reaction of the TCU
possible steps to repair
remarks
costu
mer
55
5270
9
177
SCT1
TIMEOUT
Timeout of CAN-message
SCT
1
from
steering computer
•
interference on CAN-Bus
•
CAN wire/connector is broken
•
CAN wire/connector is defective and
has contact to vehicle ground or
battery voltage
OP-Mode: normal
•
check steering computer
•
check wire of CAN-Bus
•
check cable to steering computer
Kalm
ar
55
5270
9
177
FLC1
TIMEOUT
Timeout of CAN-message FCL1 from
cluster controller
•
interference on CAN-Bus
•
CAN wire/connector is broken
•
CAN wire/connector is defective and
has contact to vehicle ground or
battery voltage
TCU keeps old auto/man
selection, old Clutch cutoff
selection and old Clutch Cuttoff
Setting
OP-Mode: normal
•
check cluster controller
•
check wire of CAN-Bus
•
check cable to cluster controller
John
Deere
55
5270
9
177
F
RONT
W
HEEL
D
RIVE
S
TATUS
TIMEOUT
Timeout of CAN-message
‘Front Wheel Drive Status
(V_IDENT_FWD)’
•
interference on CAN-Bus
•
CAN wire/connector is broken
•
CAN wire/connector is defective and
has contact to vehicle ground or
battery voltage
•
FWD Controller is defective
TCU shifts to neutral
•
check wire of CAN-Bus
•
check FWD controller
O&K
56
5280
9
105
ENGINE
CONF
TIMEOUT
Timeout of CAN-message ENGINE
CONF from engine controller
•
interference on CAN-Bus
•
CAN wire/connector is broken
•
CAN wire/connector is defective and
OP-Mode: substitute clutch
control
•
check engine controller
•
check wire of CAN-Bus
•
check cable to engine controller
J1939
Содержание 65E Turbo Motor Grader
Страница 2: ...This page intentionally left blank ...
Страница 7: ...Service Manual Section 1 Electronic Display Service 2 00_2013 03 ...
Страница 33: ...Service Manual Section 2 Engine Service 2 00_2013 03 ...
Страница 34: ......
Страница 70: ...65E Turbo Motor Grader Service Manual Service 2 00_2013 03 2 26 Section 2 Engine CAT Tier IVi Fuses ...
Страница 75: ...Service Manual Section 3 Operator s Platform and Controls Service 2 00_2013 03 ...
Страница 76: ......
Страница 90: ...65E Turbo Motor Grader Service Manual Service 2 00_2013 03 3 4 Section 3 Operator s Platform and Controls Cab ...
Страница 92: ...65E Turbo Motor Grader Service Manual Service 2 00_2013 03 3 6 Section 3 Operator s Platform and Controls ...
Страница 121: ...Service Manual Section 4 Transmission Service 2 00_2013 03 ...
Страница 122: ......
Страница 149: ...ERGOPOWER Geschäftsbereich Arbeitsmaschinen Antriebe und Achssysteme 2 1 Edition ...
Страница 171: ......
Страница 202: ...Order No 5871 146 002 ZF ERGOPOWER 6 WG 115 ZF Passau GmbH Donaustr 25 71 D 94 034 Passau ...
Страница 330: ...Service Manual Section 5 Front Axle Service 2 00_2013 03 ...
Страница 331: ......
Страница 339: ...65E Turbo Motor Grader Service Manual Section 5 Front Axle Service 2 00_2013 03 5 x This page intentionally left blank ...
Страница 371: ...65E Turbo Motor Grader Service Manual Section 5 Front Axle Service 2 00_2013 03 5 30 This page intentionally left blank ...
Страница 381: ...65E Turbo Motor Grader Service Manual Section 5 Front Axle Service 2 00_2013 03 5 40 This page intentionally left blank ...
Страница 382: ...Service Manual Section 6 Rear Axle and Tandem Service 2 00_2013 03 ...
Страница 383: ......
Страница 456: ...Service Manual Section 7 Electrical Service 2 00_2013 03 ...
Страница 457: ......
Страница 465: ...65E Turbo Motor Grader Service Manual Section 7 Electrical Service 2 00_2013 03 7 x This page intentionally left blank ...
Страница 470: ...65E Turbo Motor Grader Service Manual 7 3 Service 2 00_2013 03 Section 7 Electrical TIER III ELECTRICAL SCHEMATICS ...
Страница 471: ...65E Turbo Motor Grader Service Manual Service 2 00_2013 03 7 4 Section 7 Electrical ...
Страница 472: ...65E Turbo Motor Grader Service Manual 7 5 Service 2 00_2013 03 Section 7 Electrical ...
Страница 473: ...65E Turbo Motor Grader Service Manual Service 2 00_2013 03 7 6 Section 7 Electrical ...
Страница 474: ...65E Turbo Motor Grader Service Manual 7 7 Service 2 00_2013 03 Section 7 Electrical ...
Страница 475: ...65E Turbo Motor Grader Service Manual Service 2 00_2013 03 7 8 Section 7 Electrical ...
Страница 476: ...65E Turbo Motor Grader Service Manual 7 9 Service 2 00_2013 03 Section 7 Electrical TIER IVI ELECTRICAL SCHEMATIC ...
Страница 477: ...65E Turbo Motor Grader Service Manual Service 2 00_2013 03 7 10 Section 7 Electrical ...
Страница 478: ...65E Turbo Motor Grader Service Manual 7 11 Service 2 00_2013 03 Section 7 Electrical ...
Страница 479: ...65E Turbo Motor Grader Service Manual Service 2 00_2013 03 7 12 Section 7 Electrical ...
Страница 480: ...65E Turbo Motor Grader Service Manual 7 13 Service 2 00_2013 03 Section 7 Electrical ...
Страница 481: ...65E Turbo Motor Grader Service Manual Service 2 00_2013 03 7 14 Section 7 Electrical ...
Страница 509: ...65E Turbo Motor Grader Service Manual Service 2 00_2013 03 7 42 Section 7 Electrical 12 24 VOLT CONVERTER ...
Страница 518: ...65E Turbo Motor Grader Service Manual Section 7 Electrical Service 2 00_2013 03 This page intentionally left blank ...
Страница 519: ...Service Manual Section 8 Hydraulics Service 2 00_2013 03 ...
Страница 520: ......
Страница 528: ...65E Turbo Motor Grader Service Manual Section 8 Hydraulics Service 2 00_2013 03 8 x This page intentionally left blank ...
Страница 534: ...65E Turbo Motor Grader Service Manual Section 8 Hydraulics Service 2 00_2013 03 8 2 This page intentionally left blank ...
Страница 535: ...65E Turbo Motor Grader Service Manual 8 3 Service 2 00_2013 03 Section 8 Hydraulics TIER 3 HYDRAULIC SCHEMATIC ...
Страница 536: ...65E Turbo Motor Grader Service Manual Service 2 00_2013 03 8 3 Section 8 Hydraulics TIER 4I HYDRAULIC SCHEMATIC ...
Страница 627: ...OUT IN Eaton Gear Pumps No 6 623 Revised March 1993 PartsInformation Model 25500 Gear Pumps L2 Series ...
Страница 633: ...Char Lynn No 7 145 November 1996 Hydraulic Motor Repair Information TSeries General Purpose Geroler Motor 001 ...
Страница 641: ...Service Manual Section 9 Moldboard and Implement Service 2 00_2013 03 ...
Страница 642: ......
Страница 677: ...Service Manual Section 10 Diagnostic Fault Codes Service 2 00_2013 03 ...
Страница 678: ......