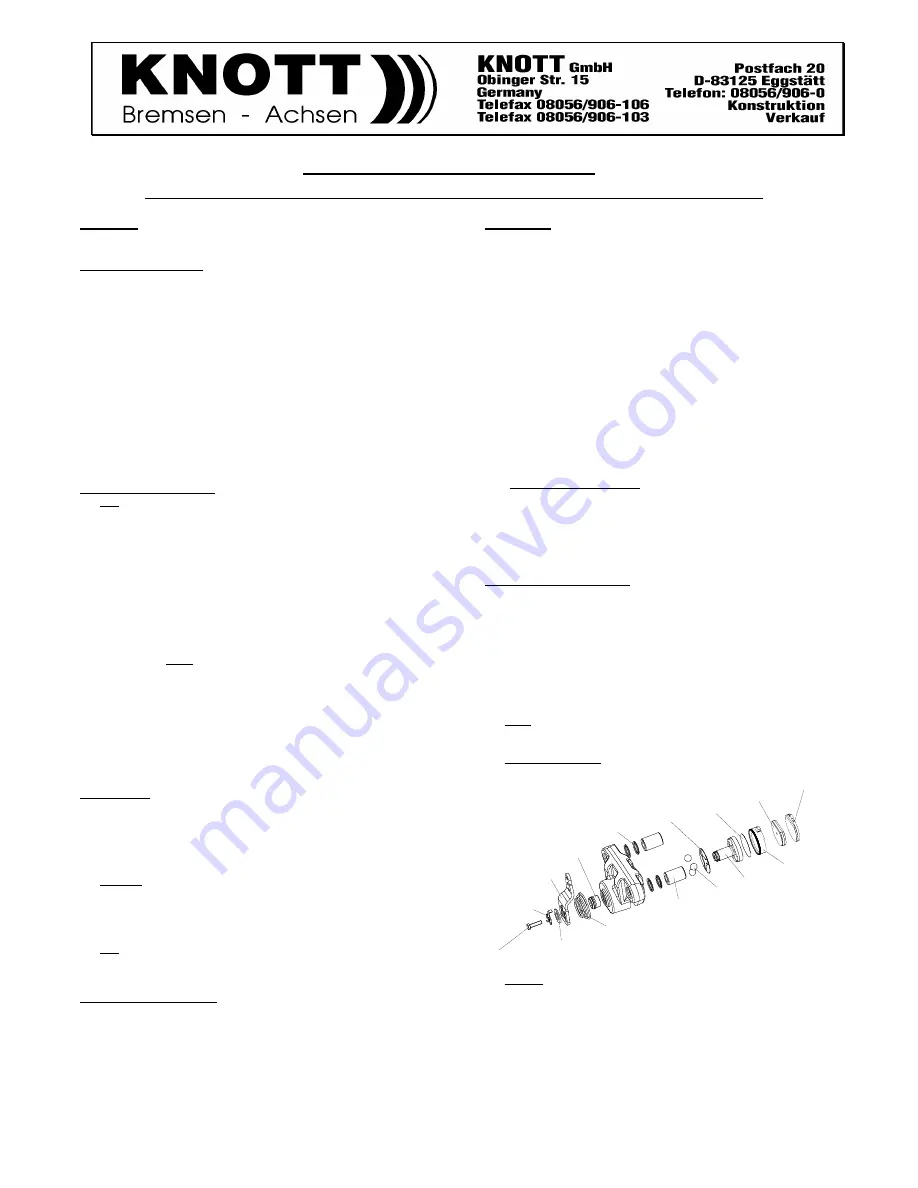
Technical Information 64/97
Functional characteristics and maintenance instructions for mechanical sliding caliper M90
1. General
This data sheet covers important service procedures that apply to the M90A model brake. Refer
to the exploded drawing as the steps are performed.
2. Routine Maintenance
The routine maintenance presented below is suggested to keep the brake system in good working
order.
2.1
Check to insure floating parts move freely and that all other parts are mounted securely. Tighten
hardware as required.
2.2 Check actuator linkage to insure that there is adequate freedom of movement for positive
brake operation. Adjustment of pad gap is to be accomplished by adjusting the actuating
cable or linkage. If adjustment is used up, back off cable or linkage. Unbend tab on anti-
rotation clip and loosen screw enough to disengage lever spline. Rotate the lever one tooth, in
the direction opposite the actuation direction, and retorque the screw making sure the spline
teeth are properly engaged. Bend up a tab that aligns with one of the screw head flats, to
prevent screw rotation. Both lever and linkage must be free to return to home position. An
external return spring is required.
2.3 Check - disc surface condition. Replace if it is badly warped, pitted, or below minimum
recommended thickness. Check for loose mount bolts. Retighten if necessary.
2.4 Check to insure friction pads are not worn to less than .039"(1.Omm) thick. Replace worn
friction pads.
Generally, if the disc is still running true and the pad clearance is still adjustable, no other
maintenance is required. To check for wear, measure the distance from the carrier side
casting face to disc face. If the distance is less than .060" (1.5mm), replace the friction pads.
3. Replacing Friction Pads
Note:
Stamped on the back of each friction pad is a code. The first 1 or 2 characters is a
number that specifies the friction material type. Check to insure new pads are the same
as the worn pads that were removed. Replace friction pads only in pairs.
To replace the friction pads it is necessary to release the brake and disconnect the actuator from
the brake lever.
3.1 Remove one brake mounting bolt. Swing the brake up over the disc to expose the brake pads.
In close clearance applications the brake may be removed from the vehicle. Using a flat
bladed screw driver, pry out the used brake pads from their respective positions. The lever
side friction pad is snapped onto the plastic actuator cover. Care should be used in removing
the friction pad from the plastic actuator cover so as not to break off the center snap tabs.
3.2 Place the new friction pads in their respective positions. The lever side friction pad has a
center hole which snaps over the plastic snap tabs of the actuator cover. The flat on the lever
side pad must align which the flat on the plastic rotor cover, allowing the pad to sit flat. If the
snap tabs are gone dab some silicone gasket adhesive around the back edge of the friction pad
and press firmly into place aligned as described above. Before placing the carrier pad in
postition, clean out existing pad glue from the pad compartment.
Place a layer of silicone gasket adhesive all along the back edge of the carrier
friction pad and press firmly in place. Push the lever side pad into the brake as far
as possible.
3.3
Swing the brake over the disc and install the mounting bolt and tighten all mounting bolts.
(see equipment service manual for proper mounting bolt torque).
3.4 linkage. Unbend tab on anti-rotation clip and loosen screw enough to disengage the lever
spline. Rotate the lever to the OEM position (see equipment service manual to determine
lever position with new pads) and torque screw to 110-140 in.lbs.(12.4-15.8 Nm). Bend up a
tab on the anti-rotation clip that aligns with one of the screw head flats, to prevent screw
rotation. Attach actuating cable or linkage to the lever. Adjustment of pad gap is
accomplished by adjusting the actuating cable or linkage.
4. Disassembly
Perform disassembly on a clean work bench.
4.1 Disconnect the actuator cable or linkage and remove brake from its mounting.
4.2 Remove friction pads. (see "Replacing Friction Pads")
4.3 Unbend anti-rotation clip tab away from lever holding screw. Remove screw, anti-rotation
clip, washer, lever, and spring.
4.4
Push out rotor assembly from the casting.
CAUTION:
Ball spacer and 3 ball bearings may come out with the rotor assembly. (for
rotor disassembly see "Servicing Rotor Assembly").
4.5 Remove 3 ball bearings and ball spacer.
4.6 Shaft seal need only be replaced if excessively worn or cracked. If replacement is necessary,
press out the plastic shaft seal from inside the casting, using a steel spacer block
1.078"(27.38mm) diameter by 2.5"(63.5mm) long and an arbor press.
Note:
A popular brand name 3/8" drive 13/16" hex deep socket works weH as a spacer block.
4.7 After the shaft seal is pressed out, remove the sliver of plastic that may be left in the groove in
the casting.
This completes disassembly of the brake.
5. Cleaning and Inspecting
5.1 Clean all parts with denatured alcohol and either wipe dry with a clean lint free cloth or blow
dry with an air hose.
5.2
Examine all parts carefully for signs of excessive wear, damage, or corrosion. Replace any
parts found to be damaged.
5.3
Check rotor assembly for cracks. Replace if necessary. The rotor assembly must be replaced
as a complete unit. No individual parts are available for service.
5.4 Inspect the casting ball pockets for scoring, pitting, cracks or corrosion. A corroded or deeply
scored casting should be replaced. Light scoring and stains may be removed.
5.5 Check to see that the disc is not bent or misshapen.
5.6 Check lever spring for breakage.
6. Assembly
Prior to assembly make sure all parts are clean and serviceable.
6.1
Install a new shaft seal by Leasing the seal from the outside of the casting with the extended
smooth surface inserted first. Using an arbor press, with a protective spacer block between the
arbor press and the seal, gently press the seal in until it snaps into the groove in the casting.
6.2
Coat with grease, the ball pockets in the casting, the shaft and ball pockets of the rotor
assembly.
6.3
Insert 3 ball bearings and ball spacer into the pockets in the casting.
6.4
From the inside of the casting slide the shaft of the rotor assembly thru the shaft seal and seat
the ball pockets against the ball bearings.
6.5 Place the spring over the large diameter pilot on the outside of the casting.
6.6 Install the lever, making sure the small diameter of the spring is piloted on the outside of the 4 pins
in the lever. Set the lever in the OEM position. (see equipment service manual to determine lever
position).
6.7 Install the washer and anti-rotation clip with its tab inserted into the lower hole in the lever.
6.8 Insert screw into rotor assembly shaft and tighten to110140 in.lbs.(12.4-15.gNm), while guiding
lever over rotor assembly spline.
6.9 After the proper torque is achieved and the lever is in the OEM position, bend up a tab on the
anti-rotation clip that aligns with one of the screw head flats, to prevent screw rotation.
6.10 Install the friction pads onto the rotor assembly and carrier. (see "Replacing Friction Pads").
6.11 Stroke lever in its proper direction. The lever must rotate thru 60 degrees of rotation. Return lever
to the 0EM position and make sure the lever side friction pad is fully returned.
7.
Replacing Mount Bushings
7.1 Push mount bushings completely out of the brake casting.
7.2 Remove the four (4) o-rings from the grooves in the casting, being careful not to damage the
grooves. Clean the grooves and the bore with denatured alcohol or cleaning solvent. Let dry.
Lubricate the grooves and o-rings with the grease furnished with the service kit. Install the o-rings
into the grooves.
7.3 Coat the bushings with kit grease. Insert bushing through the o-rings. Wipe off any excess
grease.
8. Servicing Rotor Assembly
Disassemble brake as previously described.
8.1 Using a sharp knife, make several cuts through the outside diameter of the rigid plastic rotor cover.
Break apart the plastic, remove and discard.
8.2 Discard the stainless steel insert from under the plastic cover.
8.3 Thoroughly clean all dirt and grease residue from the rotor.
8.4
Amply grease one face of the new stainless steel insert and place it into the new rotor cover, grease
to plastic. Amply grease the other face of the insert.
8.5
To assemble the new plastic rotor r-over a bench vise is necessary. Snap a friction pad onto the
plastic cover. Place the plastic cover over the rotor, place in a vice, and slowly squeeze the cover
and rotor until the cover snaps in place. Remove the friction pad and reassemble the brake as
previously described.
NOTE:
Mount bushing o-rings are also furnished in the rotor service kit. For installation see
“Replacing Mount Bushings”.
9. Sketch of the brake
anti-rotation clip
lever
screw
washer
spring
shaft seal
mount bushing
ball
lever side friction pad
carrier side friction pad
plastic cover
ball spacer
O - ring
rotor assembly
protection washer
10. General
If you lock defects or troubles by non presented parts of course you have to repair it res. you must replace
it by using original KNOTT – spare parts.
Loosing information res. instructions can you hear from the vehicle – or brake-manufacturer.
Tm6497e.doc
Содержание 65E Turbo Motor Grader
Страница 2: ...This page intentionally left blank ...
Страница 7: ...Service Manual Section 1 Electronic Display Service 2 00_2013 03 ...
Страница 33: ...Service Manual Section 2 Engine Service 2 00_2013 03 ...
Страница 34: ......
Страница 70: ...65E Turbo Motor Grader Service Manual Service 2 00_2013 03 2 26 Section 2 Engine CAT Tier IVi Fuses ...
Страница 75: ...Service Manual Section 3 Operator s Platform and Controls Service 2 00_2013 03 ...
Страница 76: ......
Страница 90: ...65E Turbo Motor Grader Service Manual Service 2 00_2013 03 3 4 Section 3 Operator s Platform and Controls Cab ...
Страница 92: ...65E Turbo Motor Grader Service Manual Service 2 00_2013 03 3 6 Section 3 Operator s Platform and Controls ...
Страница 121: ...Service Manual Section 4 Transmission Service 2 00_2013 03 ...
Страница 122: ......
Страница 149: ...ERGOPOWER Geschäftsbereich Arbeitsmaschinen Antriebe und Achssysteme 2 1 Edition ...
Страница 171: ......
Страница 202: ...Order No 5871 146 002 ZF ERGOPOWER 6 WG 115 ZF Passau GmbH Donaustr 25 71 D 94 034 Passau ...
Страница 330: ...Service Manual Section 5 Front Axle Service 2 00_2013 03 ...
Страница 331: ......
Страница 339: ...65E Turbo Motor Grader Service Manual Section 5 Front Axle Service 2 00_2013 03 5 x This page intentionally left blank ...
Страница 371: ...65E Turbo Motor Grader Service Manual Section 5 Front Axle Service 2 00_2013 03 5 30 This page intentionally left blank ...
Страница 381: ...65E Turbo Motor Grader Service Manual Section 5 Front Axle Service 2 00_2013 03 5 40 This page intentionally left blank ...
Страница 382: ...Service Manual Section 6 Rear Axle and Tandem Service 2 00_2013 03 ...
Страница 383: ......
Страница 456: ...Service Manual Section 7 Electrical Service 2 00_2013 03 ...
Страница 457: ......
Страница 465: ...65E Turbo Motor Grader Service Manual Section 7 Electrical Service 2 00_2013 03 7 x This page intentionally left blank ...
Страница 470: ...65E Turbo Motor Grader Service Manual 7 3 Service 2 00_2013 03 Section 7 Electrical TIER III ELECTRICAL SCHEMATICS ...
Страница 471: ...65E Turbo Motor Grader Service Manual Service 2 00_2013 03 7 4 Section 7 Electrical ...
Страница 472: ...65E Turbo Motor Grader Service Manual 7 5 Service 2 00_2013 03 Section 7 Electrical ...
Страница 473: ...65E Turbo Motor Grader Service Manual Service 2 00_2013 03 7 6 Section 7 Electrical ...
Страница 474: ...65E Turbo Motor Grader Service Manual 7 7 Service 2 00_2013 03 Section 7 Electrical ...
Страница 475: ...65E Turbo Motor Grader Service Manual Service 2 00_2013 03 7 8 Section 7 Electrical ...
Страница 476: ...65E Turbo Motor Grader Service Manual 7 9 Service 2 00_2013 03 Section 7 Electrical TIER IVI ELECTRICAL SCHEMATIC ...
Страница 477: ...65E Turbo Motor Grader Service Manual Service 2 00_2013 03 7 10 Section 7 Electrical ...
Страница 478: ...65E Turbo Motor Grader Service Manual 7 11 Service 2 00_2013 03 Section 7 Electrical ...
Страница 479: ...65E Turbo Motor Grader Service Manual Service 2 00_2013 03 7 12 Section 7 Electrical ...
Страница 480: ...65E Turbo Motor Grader Service Manual 7 13 Service 2 00_2013 03 Section 7 Electrical ...
Страница 481: ...65E Turbo Motor Grader Service Manual Service 2 00_2013 03 7 14 Section 7 Electrical ...
Страница 509: ...65E Turbo Motor Grader Service Manual Service 2 00_2013 03 7 42 Section 7 Electrical 12 24 VOLT CONVERTER ...
Страница 518: ...65E Turbo Motor Grader Service Manual Section 7 Electrical Service 2 00_2013 03 This page intentionally left blank ...
Страница 519: ...Service Manual Section 8 Hydraulics Service 2 00_2013 03 ...
Страница 520: ......
Страница 528: ...65E Turbo Motor Grader Service Manual Section 8 Hydraulics Service 2 00_2013 03 8 x This page intentionally left blank ...
Страница 534: ...65E Turbo Motor Grader Service Manual Section 8 Hydraulics Service 2 00_2013 03 8 2 This page intentionally left blank ...
Страница 535: ...65E Turbo Motor Grader Service Manual 8 3 Service 2 00_2013 03 Section 8 Hydraulics TIER 3 HYDRAULIC SCHEMATIC ...
Страница 536: ...65E Turbo Motor Grader Service Manual Service 2 00_2013 03 8 3 Section 8 Hydraulics TIER 4I HYDRAULIC SCHEMATIC ...
Страница 627: ...OUT IN Eaton Gear Pumps No 6 623 Revised March 1993 PartsInformation Model 25500 Gear Pumps L2 Series ...
Страница 633: ...Char Lynn No 7 145 November 1996 Hydraulic Motor Repair Information TSeries General Purpose Geroler Motor 001 ...
Страница 641: ...Service Manual Section 9 Moldboard and Implement Service 2 00_2013 03 ...
Страница 642: ......
Страница 677: ...Service Manual Section 10 Diagnostic Fault Codes Service 2 00_2013 03 ...
Страница 678: ......