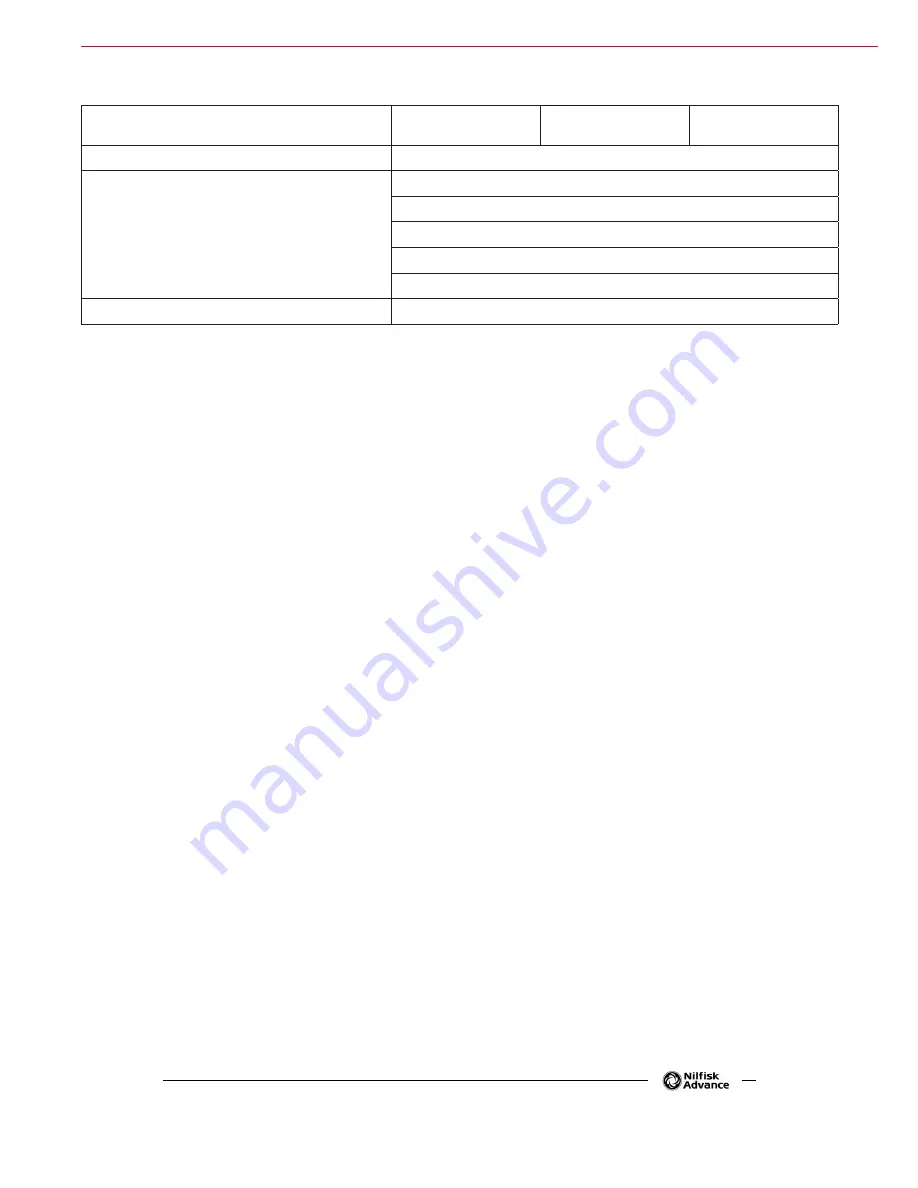
Recovery System
61
Service Manual – SC3000
Specifications
Description
Advance SC3000
Nilfisk BR 652
-
Nilfisk BR 752
-
Nilfisk BR 752C
Recovery tank capacity
21 US gal (80 L)
Vacuum system motor technical data
0.56 hp (420 W)
20.8A VDC 24V
14900 rpm
0.0146 MPa (1,448 mmH
2
O) (Blocked)
26.1 l/sec
Vacuum performance
0.0098 MPa (1,000 mmH
2
O) (Blocked)
Содержание SC3000
Страница 4: ...Table of contents 4 Service Manual SC3000 ...