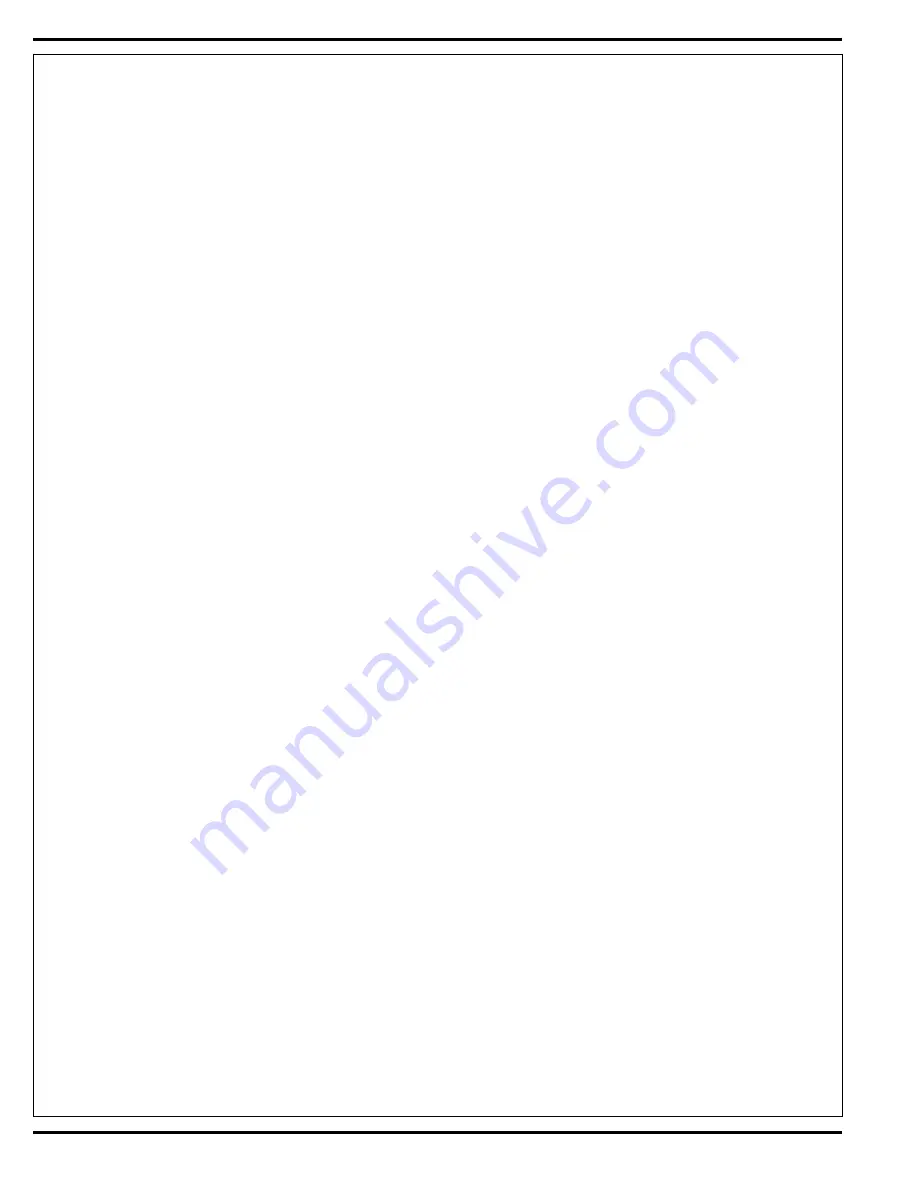
18 - FORM NO. 56043097 / Adgressor
™
/ BR 850S, 850CS, 950S, 950CS, 1050S, 1050CS
WHEEL DRIVE SYSTEM
GENERAL FUNCTIONAL OVERVIEW
See Figures 1 & 2. An 1100-watt 1.5 HP (permanent magnet) 36V motor/gear transmission combination wheel (M3) unit is used to propel all
machines. A Curtis model 1237 PMC solid state speed controller (A1) regulates (outputs) the variable speed Fwd/Rev wheel drive motor functions.
The controller unit is located to the left of the operator seat, behind the electrical access panel. The potentiometer R1 mounted to the operator’s foot
pedal, inputs to the (A1) controller the machine operator’s desired speed and directional demands.
DRIVE MOTOR SYSTEM CONTROLLER FUNCTION OVERVIEW
See Figure 2. To make the A1 speed controllers internal control circuits operational (power it up) the two switches S1 (key) and S2 (seat) must be
closed. This circuit inputs a positive (+) 36V to the A1 speed controls pin terminal #15 (*KSI). The F2 circuit breaker 70 Amp supplies the positive
high current (load) circuit input to the B+ controller terminal (Blu/Orn wire). The black wire from the negative (-) battery standoff supplies the battery
ground input to the B- terminal for both the control and load circuits.
See Figure 3. Depressing the foot pedal in either Fwd or Rev will move the 5K Ohm (R1) potentiometer shaft off its centered balanced (neutral)
setting of approximately 2500 Ohms. With this pot shaft movement the pot’s resistance value changes which generates a variable voltage signal
(0-5 volts). These control board voltage input signals are what energizes the Fwd & Rev directional relays, which selects the motor polarity and what
also manages switches the battery voltage On and Off (**PWM) that varies the motor speed.
*KSI: Key Switch Input
**PWM: Pulse Width Modulation, also called “chopping” is a technique that switches battery voltage to the motor ON and OFF very quickly, thereby
controlling the speed of the motor.
DRIVE MODE SELECTION OPERATION OVERVIEW
The A1 speed Controller allows operation in two distinct modes: mode 1 (M1) & mode 2 (M2).
Mode 1 (M1) is the transport speed range and is automatically selected when the scrub system is OFF (deck up). This allows maximum variable
vehicle speed operation.
Mode 2 (M2) is the reduced slower scrub speed range and is automatically selected when the scrub mode is ON (deck down).
The operator can over-ride the reduced M2 scrub speed by pressing the dash panel Speed Select Switch (L). This allows the operator to scrub at
the higher M1 transport speed. Note the Indicator Light (M) will be green when the faster transport speed is selected.
THE SPEED SELECTOR CIRCUIT INPUT
The main controller E1 will output a 30-31 volt (approximately) battery positive (B+) signal from the speed limit terminal J4-2 (Brn/Wht wire). This
positive signal connection delivers the required A1 speed control input to pin #11. The controller is now in scrub speed (mode 2) and the speed
control mode select is switched ON. Pressing the dash panel Speed Select Switch (L) its Indicator Light (M) turns ON. This action leaves the
speed control input (pin #11) fl oating and actively switches it Off, 0 volts (pulling it to B-) changing the output to the transport speed (mode 1).
Note: The maximum machine drive wheel speed setting for the two drive modes 1 & 2 can be changed by using the Curtis handheld programmer.
Reference the Curtis programmer instructions found in the electrical system manual section to change speed settings from their original factory
specifi cations.
Содержание Adgressor BR 1050CS
Страница 74: ...72 FORM NO 56043097 Adgressor BR 850S 850CS 950S 950CS 1050S 1050CS ELECTRICAL SYSTEM Drive Motor Breakdown ...
Страница 81: ......
Страница 82: ...www nilfisk advance com 2006 ...