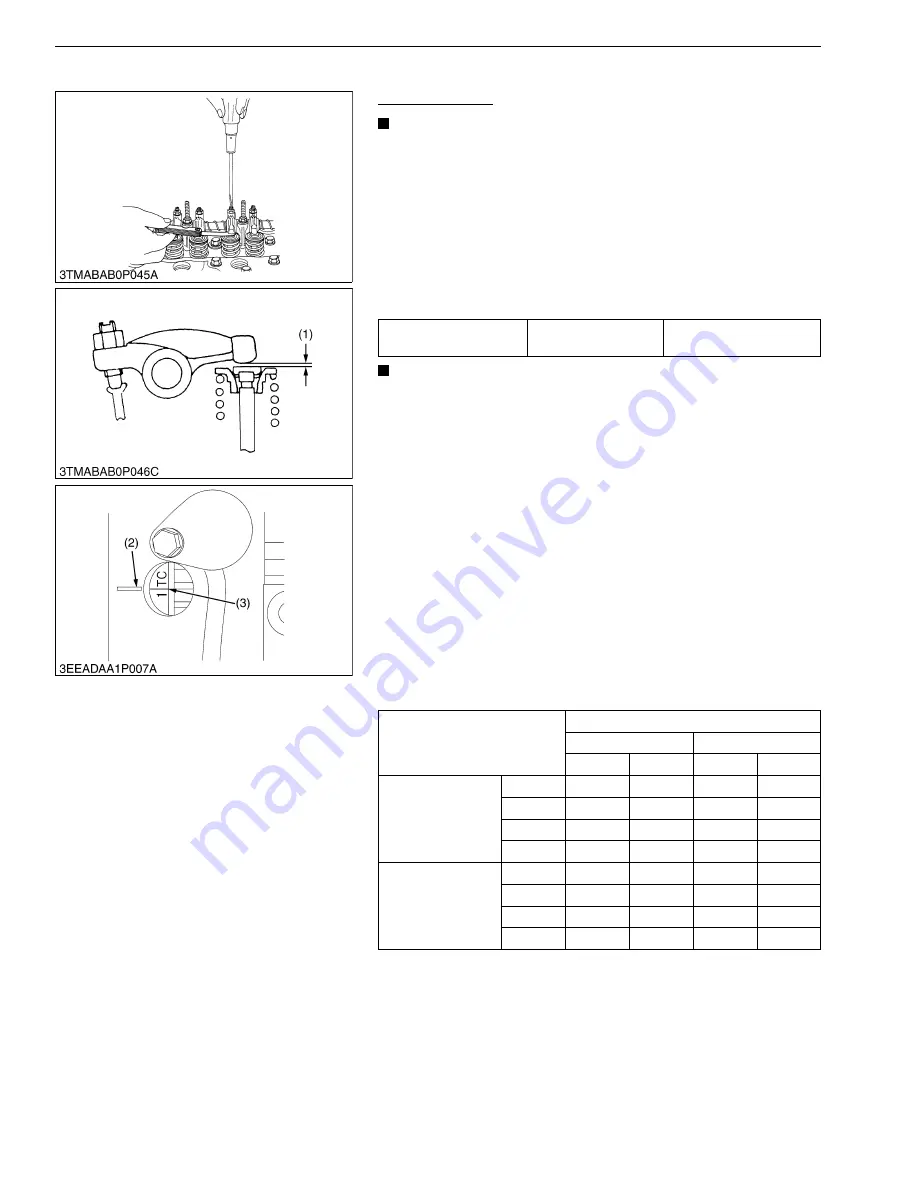
GENERAL
03-M-E3B, 03-M-DI-E3B, 03-M-E3BG, WSM
G-26
[11] CHECK POINTS FOR EVERY 800 HOURS
Valve Clearance
IMPORTANT
• You must examine and adjust the valve clearance when the
engine is cold.
1. Remove the head cover.
2. Align the
"1TC"
mark line (3) on the flywheel and projection (2)
on the housing. Make sure that the No.1 piston comes to the
compression or overlap top dead center.
3. Examine the subsequent valve clearance (1) at the mark " "
with a feeler gauge.
4. If the clearance is out of the factory specifications, adjust with
the adjusting screw.
NOTE
• The "1TC" mark line on the flywheel is only for the No. 1
cylinder. There is no "TC" mark for the other cylinders.
• Align the "TC" mark with the projection (2) in the window
on the flywheel-housing. No. 1 piston is on the top dead
center position at this time. Turn the flywheel 0.26 rad (15 °)
to see if the piston is at the compression top dead center or
the overlap position. Refer to the table below to adjust the
valve clearance (1) again. (The piston is at the compression
top dead center when both the IN. and EX. valves do not
move. The piston is at the overlap position when both the
valves move.)
• Turn the flywheel 6.28 rad (360 °) and align the "1TC" mark
line with the projection (2) correctly. Adjust all the other
valve clearance if necessary.
• After you turn the flywheel counterclockwise 2 or 3 times,
examine the valve clearance (1) again.
• After you adjust the valve clearance (1), tighten the lock nut
of the adjusting screw.
M00000003GEG0036US1
Valve clearance
Factory spec.
0.18 to 0.22 mm
0.0071 to 0.0086 in.
Adjustable Cylinder Location
of Piston
Valve Arrangement
3 Cylinder
4 Cylinder
IN.
EX.
IN.
EX.
When No. 1 piston
is at compression
top dead center
No. 1
No. 2
No. 3
No. 4
–
–
When No. 1 piston
is at overlap position
No. 1
No. 2
No. 3
No. 4
–
–
(1) Valve Clearance
(2) Projection
(3) 1TC Mark Line
KiSC issued 06, 2009 A
Содержание N4.40
Страница 3: ...I INFORMATION KiSC issued 06 2009 A...
Страница 9: ......
Страница 10: ......
Страница 11: ......
Страница 12: ......
Страница 13: ......
Страница 14: ...G GENERAL KiSC issued 06 2009 A...
Страница 61: ...1 ENGINE KiSC issued 06 2009 A...