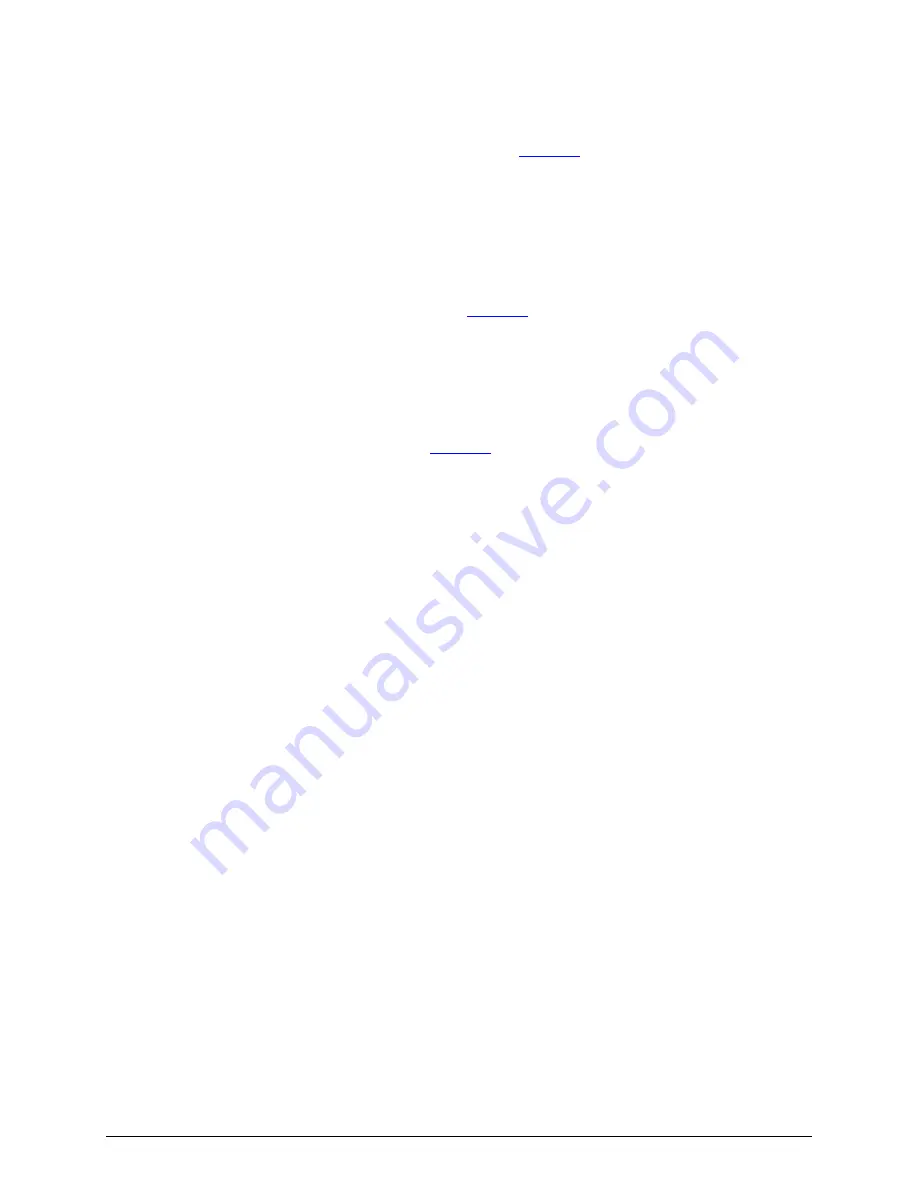
Page 7
4.4.1
Latching vs. Non-Latching Limits
A Latching Limit is one which, when the alarm trips, remains in this condition regardless of what the input may do.
This tripped limit needs to be manually reset by the operator to restore it back to its normal position. Reset is via the
front panel
RESET
button or remotely using Channel 2 Auxiliary input if programmed. A Non-Latching Limit, on the
other hand, will automatically reset itself when the input no longer exceeds the set point, either high or low. The user
can program each limit to be Latching or Non-Latching. Refer to
4.4.2
Dead band (Hysteresis)
Dead band is only applicable to
non-latching limits
. Dead band is a value that is added to the set point (in the case of a
low limit) or subtracted from the set point (in the case of a high limit) so that this new value (set point ± dead band)
becomes the reset point for the alarm. The primary purpose of this function is to prevent the alarm relays from
chattering when the input value remains very close to the set point. Dead band is set in absolute engineering units. For
example if the Limit is set to 200 RPM as a High limit and the dead band is set to 20 RPM, the alarm will trip when the
input is greater than 200 but will not reset until the input goes below 180 PM. Without the dead band feature, the alarm
relays would chatter on and off it the input varied from 199 to 201, which is undesirable. The user can set the
hysteresis to any value from 0.0001 to 99,999. Refer to
NOTE:
The Dead band needs to be less than the setpoint.
4.4.3
Low Limit Lockout
The Low Limit Lockout is a feature that prevents a low alarm from tripping when the input starts from zero. The low
alarm essentially is locked out and will not operate until the input exceeds the low limit, at which time the low alarm is
enabled and will trip when the input goes below the set point. This feature enables a motor that has a low speed cut out
(low alarm) to start from rest without having to short out the normally closed relay contacts externally. This feature
may be enabled or disabled by the user. Refer to
4.4.4
Fail Safe
The Fail Safe option reverses the sense of the relays, essentially energizing them under normal conditions. When an
alarm is set, the relays will drop out (become de-energized). Thus in the event of a power failure the relays will drop
out by default creating the equivalent of an alarm condition.
4.5
Analog (AO) and Current (IO) Output
The
ACT-3X
has options for voltage (0 to 5Vdc) or current (4 to 20mA) outputs.
The analog outputs are derived from a 15-bit digital to analog converter. This means that the output voltage (or current)
changes in steps. The standard analog output has ~32,000 steps from zero to full scale. This implies that each step size is
1/32,000 of the full-scale value or about 0.003% of full scale. The user can set the actual full scale value anywhere from 1
to 999,990. This full-scale value is the value at which the analog outputs are at a maximum, 5 Vdc or 20 mA.
The zero and full-scale range is usually set to give a reasonable working range for the analog output. For example, if you
are measuring the RPM of a motor that typically runs at 1700 RPM, you may want to set the zero scale (offset) for 1000 and
the full-scale for the analog output at 2000. Note that the zero and full scale ranges are always set in the units you choose to
display; RPM in this case. The output voltage will then be 5 Vdc (20 mA) for an input of 2000. It will be linear between
1000 (zero scale) and 2000 (full-scale). Thus, at 1700 RPM the output will be:
(1700 - 1000)
—————— X 5 Vdc = 3.5 Vdc
(2000 - 1000)
(2000 - 1000)
Resolution = —————— = 0.03 RPM
32,000
NOTE:
For any input below the zero scale setting, the outputs will be at 0 Vdc or 4 mA. For any input above the full scale
setting, the outputs will be at their maximum value, 5 Vdc or 20 mA.
4.6
Maximum and Minimum
The unit tracks and saves the maximum and minimum values. These values are continuously updated and can be viewed at
any time by pressing the
RECALL
button on the front panel. The first time this button is pressed the
MAX
imum is shown,
indicated by the MAX light to the right of the display. Pressing the
RECALL
button a second time shows the
MIN
imum.
The user can also reset these values by pressing and holding the
RECALL
button and then pressing the
RESET
button.
The next reading will always update both values. This will keep the minimum value from showing zero unless there was a
zero reading after the
RECALL
and
RESET
buttons were pressed.
Thus, if you start a motor, for example, from zero, the minimum will start recording with the first reading. Usually the user
will reset the minimum once the motor is up to speed. When slowing to a stop, the minimum will naturally tend to zero, but
the maximum will be retained.