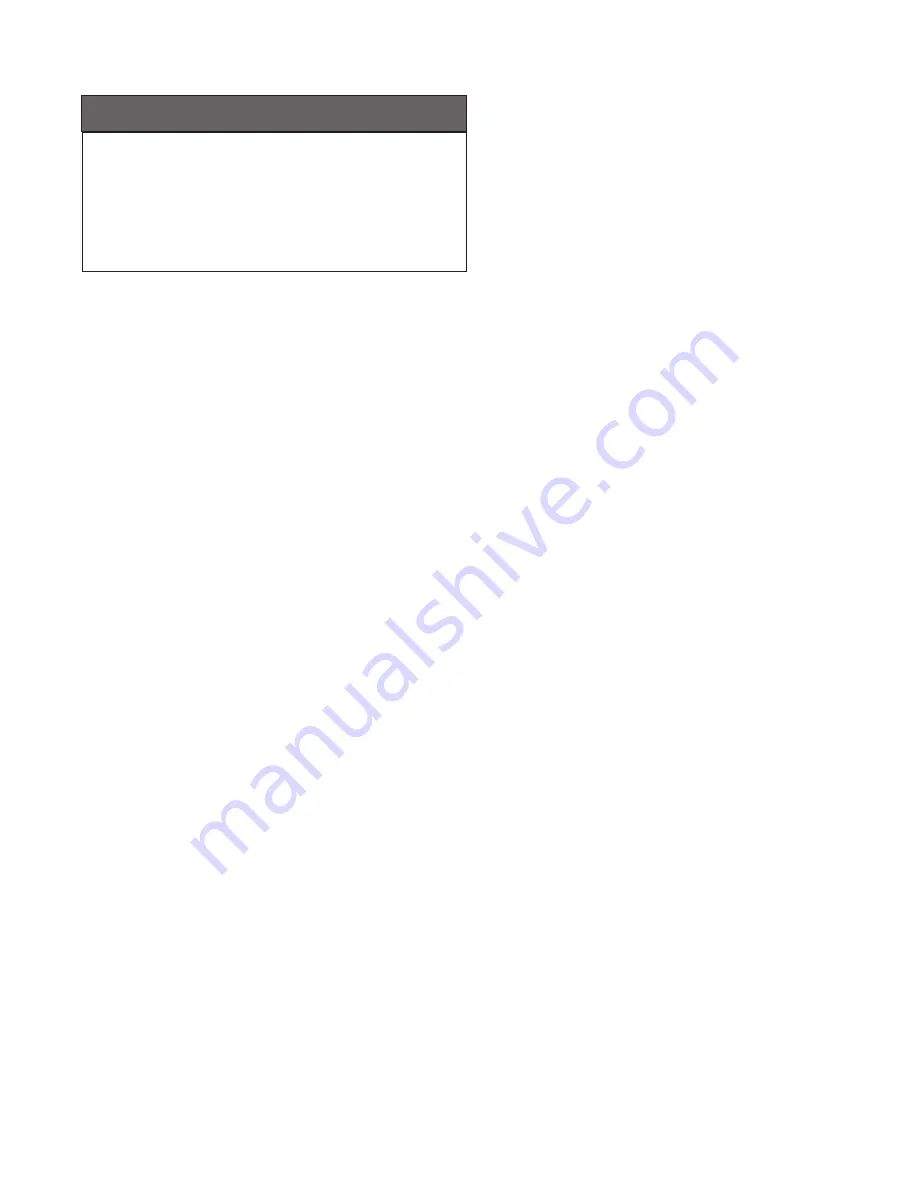
23
MCP15-500.9
START-UP PROCEDURE - CONTINUED
Gas Heating Option
The Gas Heating Option requires gas pressure be measured
and adjusted as required at several points on the unit. The
following steps must be completed:
Identify the Gas Control Type
Before you begin, review the furnace serial plate to determine
the model installed. The serial plate is located on the right hand
access door for the furnace section. Refer to Pages 62 through
66 for Serial Plate and Model Nomenclature information. Note
that the furnace serial plate is separate from the unit (model
MPR) serial plate.
Digit 11 of the furnace model number denotes the type of gas
control used. These are defined below:
4
- Indicates two heat exchangers using basic modulating
controls with United Technologies ignition. Manifold
pressure of both heat exchangers is varied
simultaneously based on demand. Power exhausters
operate at a constant speed.
6
- Indicates a single heat exchanger with Beckett advanced
modulation control which varies the manifold pressure
and power exhauster speed based on demand. High
turn down and more consistent efficiency are possible
with this control.
8
- Indicates two or more heat exchangers; one equipped
with advanced Beckett modulation primary control
and the other(s) equipped with non-modulating single
input secondary control. The secondary control heat
exchanger(s) is controlled and monitored by the primary
control and will turn on or off depending on demand.
Check/Adjust Pressure Upstream of Unit
With the field installed manual gas shut-off valve in the “OFF”
position, recheck the gas supply pressure at the field installed
manual shut-off valve. The inlet pressure should be 6"-7" W.C.
on natural gas or 11”-14” W.C. on propane (LP) gas, while all
burners are operating, but never more than 14" W.C when the
burners are off. If inlet pressure is too high, install an additional
pressure regulator upstream of the combination gas control.
Check/Adjust Pressure at Combination Gas Valve
1. Open the field installed manual gas shut-off valve and set
the combination gas control valve to the “ON” position.
Note for C- and D-Cabinet sized units, the Gas Heating
Option consists of two or more heating sections. For this
step, only one combination gas valve is to be set to the
“ON” position.
2. Enable the unit controls. For furnace models with furnace
model Digit 11=6, the LED readout on the furnace control
board (Figure 25.1) will briefly display the furnace size.
Verify that the model readout is correct for the unit being
started.
3. Ensure that the supply fan blower is operating at the proper
airflow and adjust the Modine Control Systemc control
setpoint to create a call for heat. Refer to the Controls
Manual, literature #MCP74-525 for instructions on changing
the setpoint.
4. Check the ignition control and gas valve for electrical
operation.
5. Check to make sure that the main gas valve opens while
the supply fan blower is operating.
6. Check the gas pressure at the INLET to the combination
gas control valve (refer to figures on pages 26 through 31)
and adjust as needed to maintain 6-7" W.C for Natural Gas
(11-14" W.C. for Propane) while the burners are operating
at high fire. This pressure is required for proper ignition and
to attain the rated input of the unit. If this pressure cannot
be obtained, the gas supply is undersized and needs to be
corrected or the gas supplier must be contacted.
7. Check gas pressure on the OUTLET of the combination
gas control valve (refer to figures on pages 26 through
31) when the burners are functioning. This should be set
to 4.0" W.C. for Natural Gas (10.5" W.C. for Propane)
for all furnaces with furnace model Digit 11=4, or 6. For
C-Cabinet furnaces with furnace model Digit 11=8, only
the right hand modulated heat exchanger (Primary) is set
to 4.0”W.C. for Natural Gas (10.5" W.C. for Propane). The
left hand fixed input heat exchanger (Seondary) is set to
3.5”W.C. for Natural Gas (10.0" W.C. for Propane). Adjust
the gas control valve regulator as needed (see gas valve
instruction sheet for location.)
8. Check to ensure that gas controls sequence properly (see
Controls Manual, literature #MCP74-525).
9. For units with multiple heat exchangers, repeat steps 3
through 8 for each heat exchanger before proceeding to
the next step.
Check/Adjust Pressure at Manifold
The following steps are required to check/adjust the manifold
pressure on modulated heat exchangers. For units with furnace
model Digit 11=4, this process applies to both heat exchangers
and is conducted on one heat exchanger at a time. For all
other units, this process applies to only one heat exchanger,
normally the lower right heat exchanger on multiple heat
exchanger units.
1. Move the field installed manual shut-off valve to the “OFF”
position.
2. Remove the 1/8" pipe plug in the pipe tee of the furnace.
3. Attach a digital or “U” tube type water manometer which is
at least 12" high and capable of reading to 0.1" W.C.
4. The Maxitrol EXA modulating valve series (refer to figures
on pages 26 through 31) has a cover secured with two
screws that must be removed. Once removed, there
are a bank of (3) DIP switches and two buttons and a
communication LED for the user interface as shown in
Figure 24.1.
5. Verify that the DIP switches are properly set to the settings
shown in Figure 24.1.
6. Move the field installed manual gas shut-off valve to the
“ON” position.
7. Adjust the High Fire Setting as follows:
a. Enable the unit controls.
b. For units with furnace model Digit 11=6 or 8, place
the furnace control into the “Checkout Test Mode”
as described on the next page and set the Fire Rate
Input to 10.0.
THIS SECTION APPLIES TO UNITS WITH
OPTIONAL GAS HEAT
(MODEL DIGIT 17=2, 3, 5 OR 6).
IF THE UNIT DOES NOT HAVE GAS HEAT,
SKIP TO PAGE 32.
REVIEW BEFORE PROCEEDING
Содержание MPR Series
Страница 17: ...17 MCP15 500 9 PAGE INTENTIONALLY LEFT BLANK ...
Страница 67: ...67 MCP15 500 9 PAGE INTENTIONALLY LEFT BLANK ...