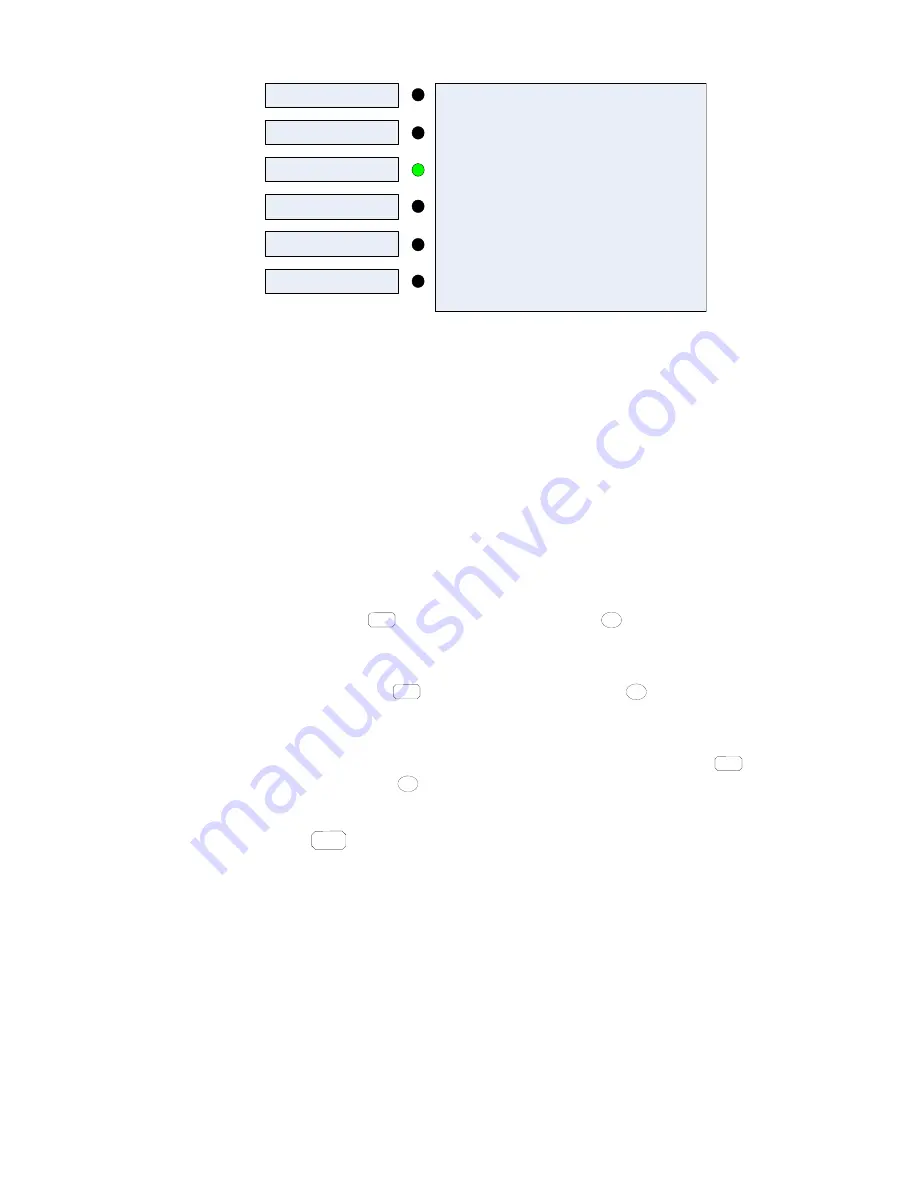
946 Controller Instruction Manual
pg. 56
A1
A2
B1
B2
C1
C2
Torr
FC
399.3
10.01
300.5
1.300
FC
FC
CM
10.07
CM
250.0
FC
4.0E+2
SCCM
PID
SCCM
Close
SCCM
SP
SCCM
SP
Figure 6-18 Front Panel Display during PID Control using Single MFC
•
During PID control process, the active MFC flow reading and corresponding
controlling pressure gauge reading are displayed in blue color to identify these
channels. PID will be displayed as well to indicate the MFC channel under the PID
control (C1 in Figure 6-18).
•
The color of the flow rate will turn into red as a warning if the real flow rate is >2% of
full scale and 20% off the PID set point value. This might happen, for example, if the
gas supply for the MFC is turned OFF accidently during the PID control process.
6.7.3.1.3 Terminate Single MFC PID Control
PID based pressure control with a single MFC can be terminated to any of the following
conditions:
1. Close the MFC:
To close the MFC completely, move the green LED indicator to the MFC in use for
the PID, press the
Close
button on the front panel, and
Enter
key to confirm.
2. Open the MFC fully:
To Open the MFC completely, move the green LED indicator to the MFC in use for
the PID and press the
Open
button on the front panel, and
Enter
key to confirm.
3. Set the MFC to fixed set point defined by the Flowrate SP in Channel setup screen:
To switch the flow rate to that defined in the channel setup screen, move the green
LED indicator to the PID Channel (active MFC channel), and press the
Setpoint
button
on the front panel, and
Enter
key to confirm the action.
4. Set the MFC to the set point defined in the recipe (Preset)
•
Press the
Pressure
Control
to display the PID Control dialog box
•
Switch the PID Control parameter from ON to OFF as shown in Figure 6-17. Once
the PID control is turned OFF, the flow rate for the MFC will be changed to the Preset
set point as defined in the recipe (refer to Figure 6-14).
6.7.3.1.4 Effect of PID Recipe Change While Control is Running
Some of the parameters associated with the active PID control can be changed (via either front
panel or serial communication) while the PID control is running. They are pressure set point (P
Set point), proportional (Prop-Kp), integral (Integral-Ti), and derivative (Derivative-Td). This
allows adjusting and optimizing these parameters without turning ON/OFF the PID control. The
remaining PID recipe parameters cannot be changed while the control is running.
When any of these 4 parameters in a PID control recipe is modified while PID control is operating,
the new setting will take effect immediately in the running pressure control process. However, the