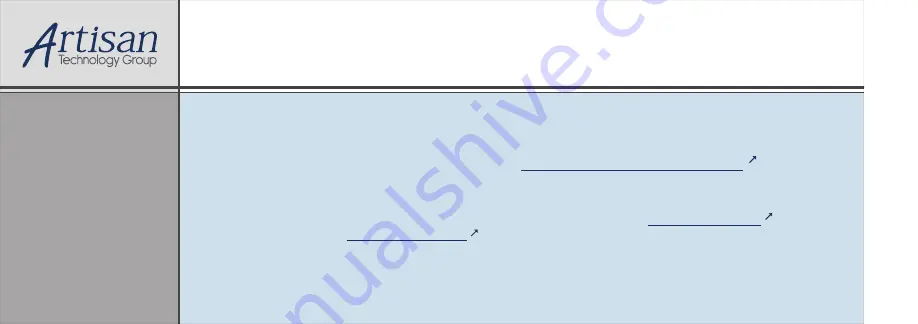
Artisan Technology Group
is your source for quality
new and certified-used/pre-owned equipment
•
FAST SHIPPING AND
DELIVERY
•
TENS OF THOUSANDS OF
IN-STOCK ITEMS
• EQUIPMENT DEMOS
•
HUNDREDS OF
MANUFACTURERS
SUPPORTED
• LEASING/MONTHLY
RENTALS
• ITAR CERTIFIED
SECURE ASSET
SOLUTIONS
SERVICE CENTER REPAIRS
Experienced engineers and technicians on staff
at our full-service, in-house repair center
WE BUY USED EQUIPMENT
Sell your excess, underutilized, and idle used equipment
We also offer credit for buy-backs and trade-ins
www.artisantg.com/WeBuyEquipment
REMOTE INSPECTION
Remotely inspect equipment before purchasing with
our interactive website at
www.instraview.com
LOOKING FOR MORE INFORMATION?
Visit us on the web at
www.artisantg.com
for more
information on price quotations, drivers, technical
specifications, manuals, and documentation
Contact us:
(888) 88-SOURCE | [email protected] | www.artisantg.com
SM
View
Instra
Содержание 1-292-01
Страница 19: ......
Страница 27: ......
Страница 43: ......
Страница 53: ......
Страница 55: ......
Страница 59: ......
Страница 72: ...APPENDIX B ELECTRICAL AND DATA CONNECTIONS UNIFLOW 2 PULSED THERMODE CONTROL 990 228 B 13 Relay State Timing ...
Страница 77: ......
Страница 79: ......
Страница 95: ......
Страница 107: ......