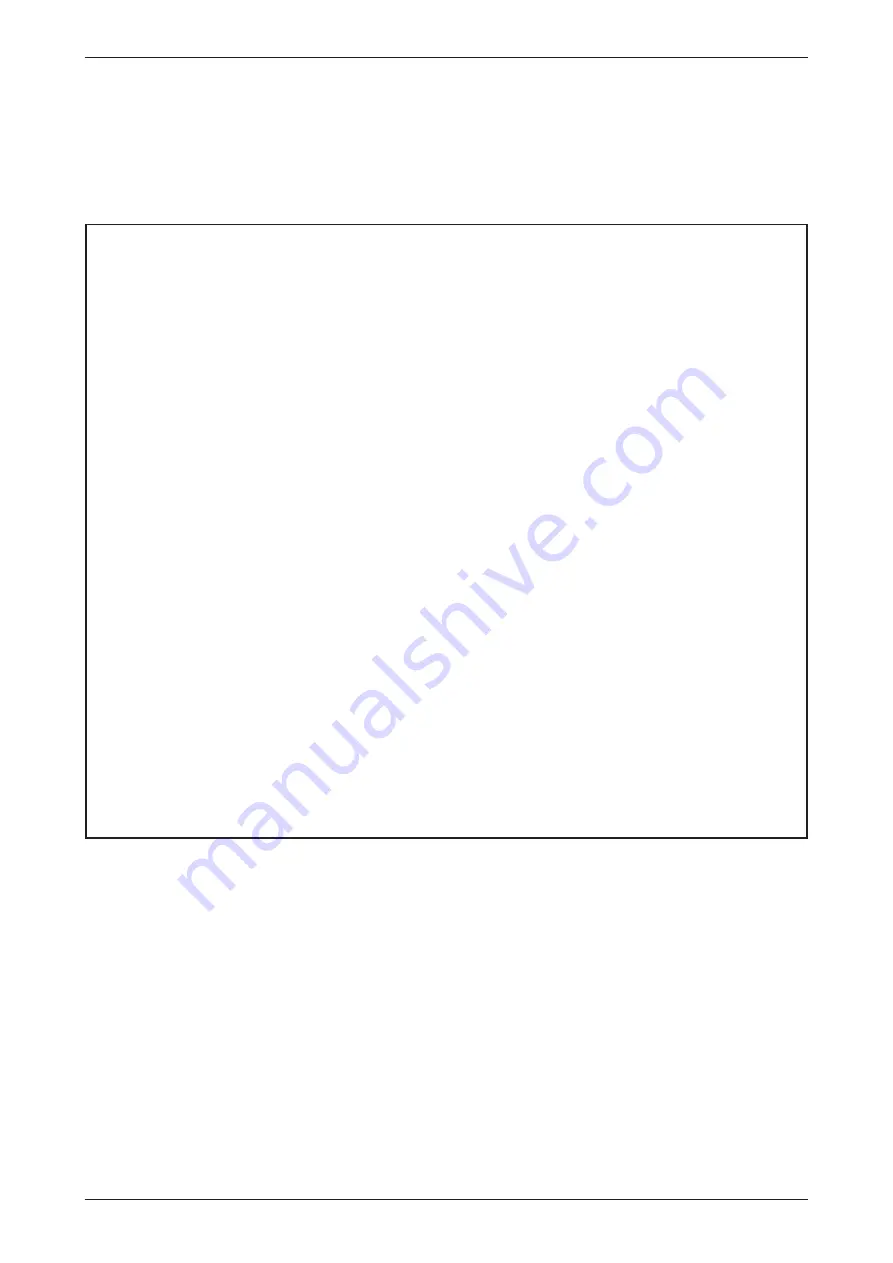
General safety information and precautions
The following safety precautions are intended as a general guideline for using the PLC together
with other equipment. These precautions must always be observed in the design, installation
and operation of all control systems.
P
CAUTION:
Training Manual GX IEC Developer
III
쎲
Observe all safety and accident prevention regulations applicable to your
specific application. Installation, wiring and opening of the assemblies, com-
ponents and devices may only be performed with all power supplies discon-
nected.
쎲
Assemblies, components and devices must always be installed in a shockproof
housing fitted with a proper cover and protective equipment.
쎲
Devices with a permanent connection to the mains power supply must be inte-
grated in the building installations with an all-pole disconnection switch and a
suitable fuse.
쎲
Check power cables and lines connected to the equipment regularly for breaks
and insulation damage. If cable damage is found, immediately disconnect the
equipment and the cables from the power supply and replace the defective
cabling.
쎲
Before using the equipment for the first time check that the power supply rating
matches that of the local mains power.
쎲
Residual current protective devices pursuant to DIN VDE Standard 0641 Parts
1-3 are not adequate on their own as protection against indirect contact for
installations with positioning drive systems. Additional and/or other protection
facilities are essential for such installations.
쎲
EMERGENCY OFF facilities pursuant to EN 60204/IEC 204 VDE 0113 must
remain fully operative at all times and in all control system operating modes. The
EMERGENCY OFF facility reset function must be designed so that it cannot
cause an uncontrolled or undefined restart.
쎲
You must also implement hardware and software safety precautions to prevent
the possibility of undefined control system states caused by signal line cable or
core breaks.
쎲
All relevant electrical and physical specifications must be strictly observed
and maintained for all the modules in the installation.
Содержание FX2N-32CAN
Страница 1: ...MITSUBISHI ELECTRIC FACTORY AUTOMATION Programmable Logic Controllers GX IEC Developer ...
Страница 2: ......
Страница 4: ......
Страница 6: ......
Страница 10: ...IV MITSUBISHI ELECTRIC ...
Страница 18: ...Modular PLC Training Hardware Course Overview and Requirements 1 2 MITSUBISHI ELECTRIC ...
Страница 172: ...Monitoring Instances of Function Blocks Advanced Monitoring Functions 7 12 MITSUBISHI ELECTRIC ...
Страница 176: ...Device Edit 8 4 MITSUBISHI ELECTRIC ...
Страница 190: ...Assigning DUT Variables to Function Blocks Data Unit Types DUT 10 10 MITSUBISHI ELECTRIC ...
Страница 198: ...Array Example Single Dimension Array Arrays 11 8 MITSUBISHI ELECTRIC ...
Страница 219: ...Sequential Function Chart SFC SFC Elements Training Manual GX IEC Developer 14 3 ...
Страница 220: ...14 3 SFC configuration examples SFC configuration examples Sequential Function Chart SFC 14 4 MITSUBISHI ELECTRIC ...
Страница 230: ...Structured Text Program Example IEC Structured Text 16 4 MITSUBISHI ELECTRIC ...
Страница 248: ...Configuring GX IEC Developer to access the PLC on Ethernet Ethernet Communications 18 10 MITSUBISHI ELECTRIC ...
Страница 278: ...PLC Components Glossary Appendix A 18 MITSUBISHI ELECTRIC ...
Страница 283: ......