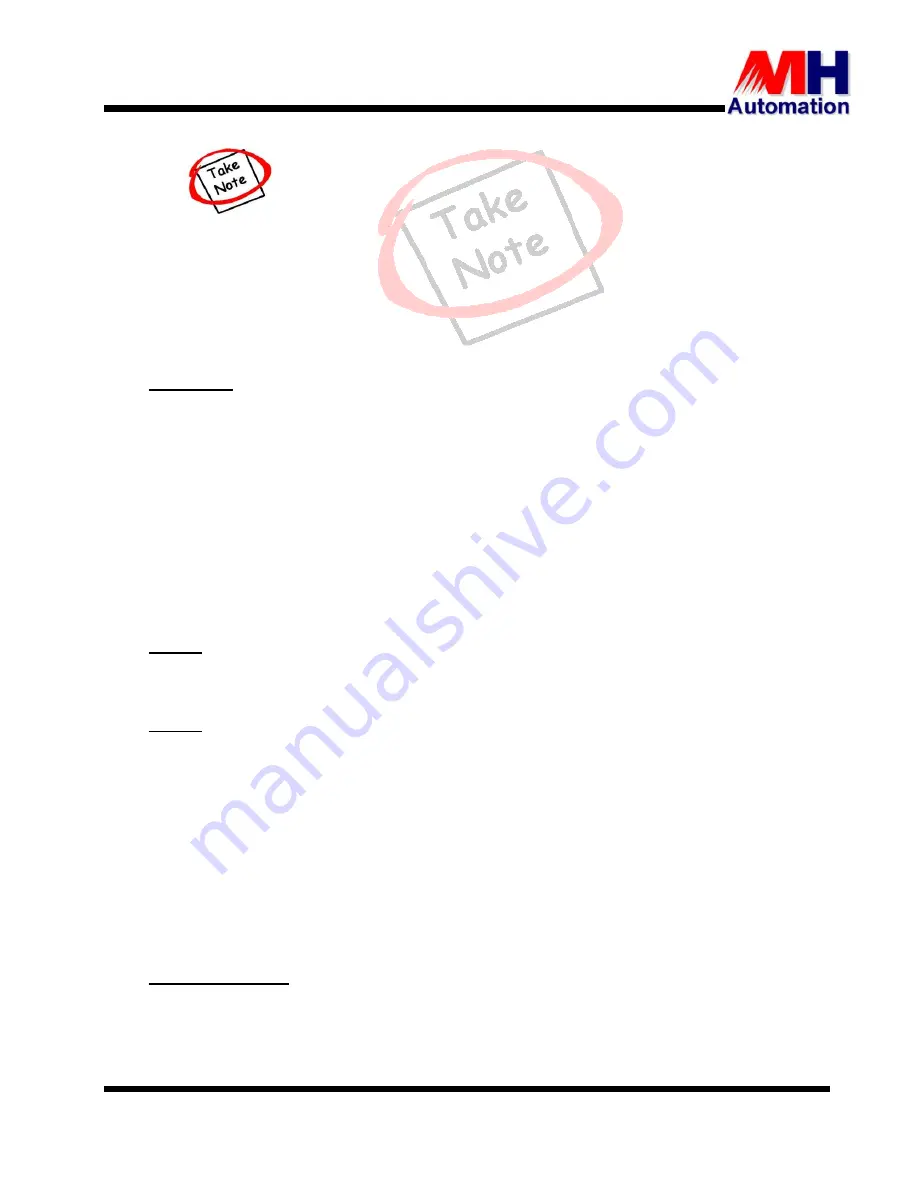
U
U
s
s
e
e
r
r
M
M
a
a
n
n
u
u
a
a
l
l
Revision 8.6
SECTION 5 : COMMISSIONING
73
NOTE
This may not correspond to the rated name
plate kW of the motor if the resistance was
calculated
based
on
the
motion
mechanical power. Usually the schematic
diagrams will make reference to the exact
motor kW which the system has been
designed for.
Helpful Hint:
With the maximum stall voltage set at 80% of the supply:
As a general rule, under this test conditions the rotor voltage will drop by a factor close to 1.5 of its name
plate value. The mechanical or electrical current (depending on the design) will increase by the same
factor.
Major deviations from these general rules it may indicate problems which may require further
investigation. It is not possible to elaborate on the causes of the problem due to an immense variety of
causes which may influence the results obtained during the tests.
It would be advisable to get in contact with the Technical department at MH Automation or any of their
accredited representatives or agents for further assistance.
Step 11
After these tests are performed and assuming that both have had satisfactory results, the brake
contactor coil should be reconnected as recommended and proceed with the next step.
Step 12
No load test
: Run the motion in both directions notch by notch to ensure that the direction of rotation is
correct and there are no other problems. In the case of Hoist motions the rotary limit switch top and
bottom should now be tested.
In the case of Travel motions, slow down and end of course limits if applicable should now be tested.
During the No-Load test, ensure that there is no visible arcing on the contactors. When all the
contactors switching times are known it is easy to set up the parameters to avoid contactor arcing, but in
some cases it is not possible to determine the switch in and drop out times of the contactors and a
practical way of achieving no arcing is by running the Hoist motion in the lowering direction, between 4
th
and 3
rd
notches. This way the reversing contactors as well as the rotor contactors will all be operating,
check for possible arcing and if present increase the Phase Shifter OFF time.
Step 13 (Hoist only)
Monitor the operation of the brake contactor versus the directional contactors. At the end of any cycle
the brake contactor should de-energize first. The power will remain on the motor for a further 500 to
1050 msec. depending on the setting of the respective parameter (Stop delay). Only after this time has
expired the directional contactor will drop out.