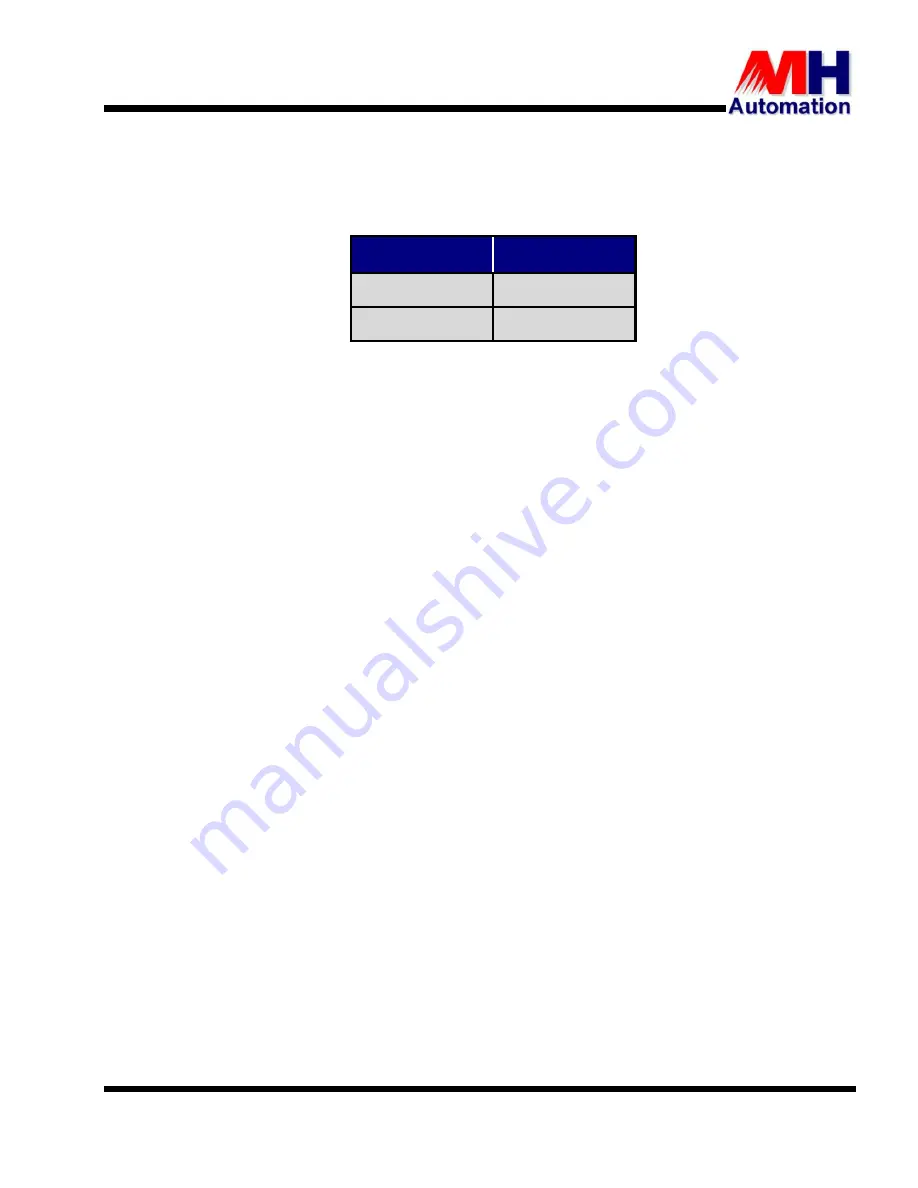
U
U
s
s
e
e
r
r
M
M
a
a
n
n
u
u
a
a
l
l
Revision 8.6
SECTION 2 : SYSTEM DESIGN
12
2.3. PROTECTION
Table 2-3 lists the protection specifications for the THYROMAT.
Table 2-3 : THYROMAT Protection
Item
Specification
Control enclosure
IP51
Thyristor stack
IP00
2.4. THYROMAT - BD DIGITAL CRANE CONTROLLER SELECTION
The selection of the THYROMAT for specific mechanical power requirements depends on the base stator
current rating on of the slip-ring motor to be used. In the event that the base stator current ratings are not
known then it is suggested that the same ratings S
4
or S
5
for crane duty slip-ring motors be used.
Perform the following steps to calculate the mechanical power
Step 1.
Calculate the mechanical power that will be generated by the motor using the speed, load and
efficiency of the motion.
Step 2.
If this data is not available use the electrical power for the specific duty.
Step 3.
Obtain the stator current for the specific power selected
Step 4.
Refer to the table and select the THYROMAT.
The selection of the THYROMAT has been divided into two operational categories for both hoist and
travel namely, standard duty and severe duty.
The following paragraphs define standard and severe duty applications:
2.4.1
Standard Duty
The following defines standard duty:-
Characteristics
Rated starting class
- 150 starts per hour.
Cyclic duration factor
- 40%
Max. Ambient Temperature
- 40ºC
Altitude above sea level
- < 1 500 meters
The typical standard duty applications are as for BS 466:1984 cranes with a group mechanism in M3
and M4, the following lists typical standard duty applications:-