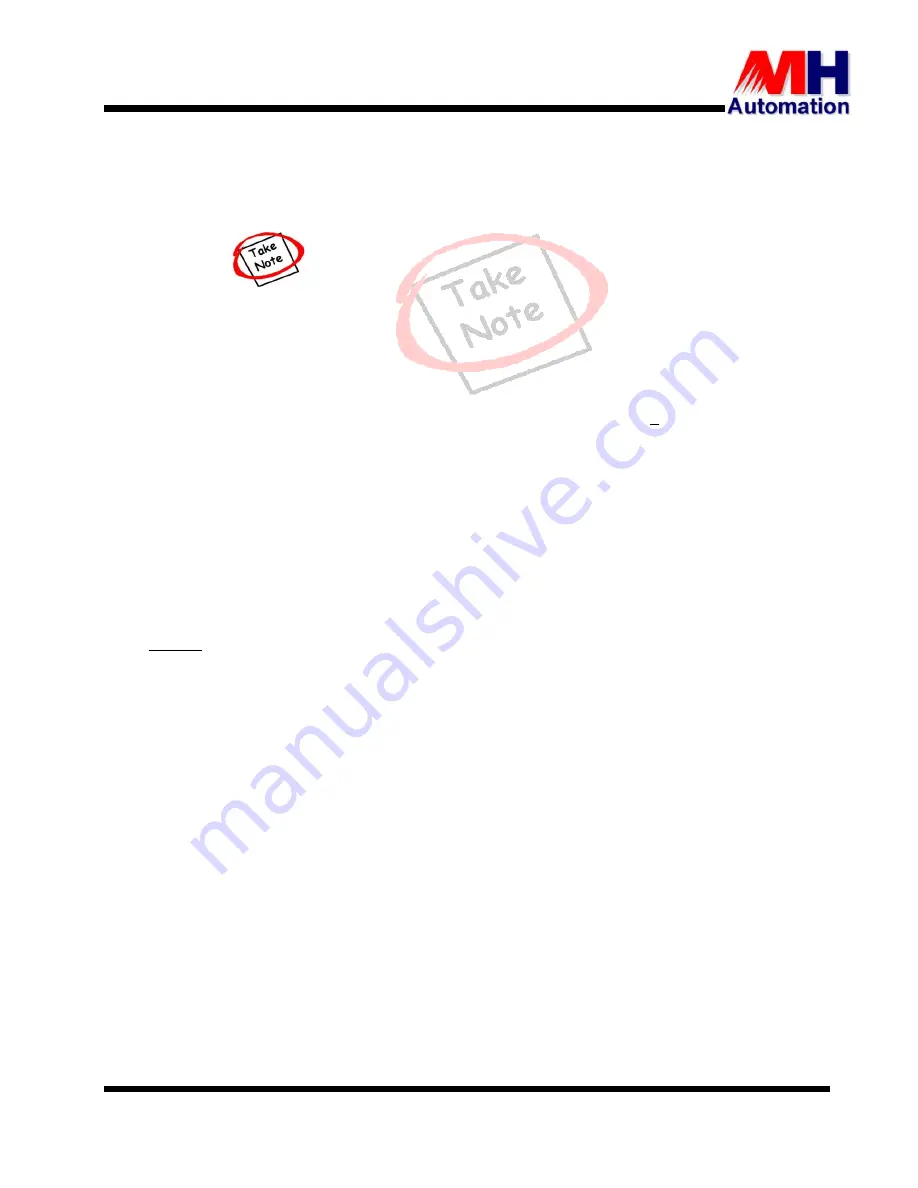
U
U
s
s
e
e
r
r
M
M
a
a
n
n
u
u
a
a
l
l
Revision 8.6
SECTION 5 : COMMISSIONING
72
g)
Move the cabin joystick to Notch 1 Hoisting
h)
Measure the stator and rotor voltages between phases at the motor terminals
i)
Confirm that the Stator/Rotor voltage ratio falls 10% of name plate
NOTE
This test may only be performed for
periods of approximately 10 seconds at the
time since the Thyromat drive will trip on
motor stall, if it remains for longer periods
in Notch 1.
Analyzing the results:
When the above mentioned voltage ratio falls within the reco 10% deviation the test is
considered successful, and the next test must now be performed. When such ratio is out the
recommended deviation, one needs to verify why this is the case.
In the case of an upgraded installation it may be that the motor may have been rewound previously and
its characteristics have changed slightly, if the deviation is too great, it may be possibly that the Rotor
connections have been changed from Y to
∆ or vice-versa. In this case the motor may not perform well
under full load conditions and it may be necessary to replace it with a standby spare motor.
Under a great discrepancy on the rotor voltage, the rotor resistance which was calculated around the
motor name plate values is going to be inadequate too and this needs to be taken in consideration as
well.
Consult MH Automation for advice in the event that the results are out of acceptable boundaries.
Step 10
Perform locked Rotor test (Closed rotor circuit) (this test should only be performed if the test mentioned
in Step 8 is successful).
a)
Repeat step by step all the instructions referred to in Step 9 (a) to (g).
h)
Measure the stator voltages between phases. The supply voltage must remain within 90% of
its rated value, preferably > 95%. Look out for any major phase imbalances.
i)
Measure the stator currents per phase. These currents should be fairly balanced.
j)
Measure the rotor voltages at the motor terminals between phases.
k)
Measure all three rotor currents (at the motor terminals)
l)
Assuming that there are no major unbalances in either rotor voltages or currents, take the
average values of both and apply them to the formula below
Motor kW = Rotor volts x Rotor amps / 605
The resultant kW for a maximum stall voltage of 80% and a Rotor resistance of 0,36k should be
approximately the same as the kW which the system has been designed for.