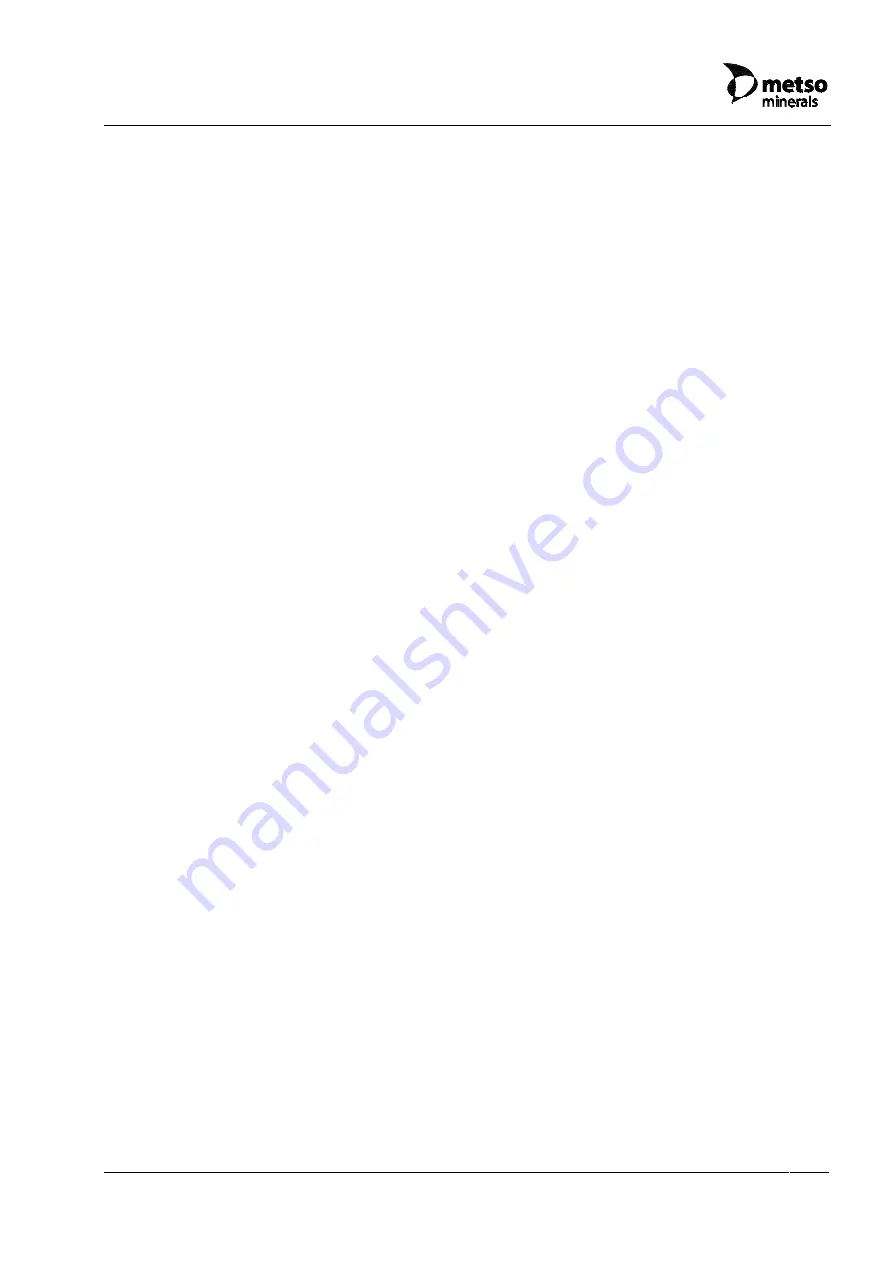
Slurry Pump
WH22AAAAAA0EN_03B.DOC
JAN
04-W08
Care and maintenance
2/3
9.6.3
The pump starts but the motor protection trips
Has flow path or pipe run been
modified ?
No
⇓
⇓
Yes
⇒
•
Alter the flow path or pipe run, or adjust the
rating of the drive motor and pump to suit
new operating conditions.
Is motor protection setting too low ?
No
⇓
⇓
Yes
⇒
•
Check against the motor rating plate and
adjust as necessary
Is shaft jammed or hard to turn?
No
Yes
⇒
•
Securely isolate the power supply.
⇓
⇓
⇓
⇓
•
Remove the belt guard and try to rotate the
pump shaft by hand.
•
Dismantle the pump and clean behind the
impeller. See section 9.5.2. Flush out the
pump and the pump sump
⇓
⇓
⇓
•
Dismantle the drive and check that both the
motor and pump shaft can be rotated. Fit
new bearings if necessary. See section 9.5
and the motor manufacturer’s instructions.
⇓
•
Check that pump clearances are correct.
See section 9.5.1.
9.6.4
The pump is running but the flow rate is too low or nil
Has operating conditions or pipe run
been modified ?
No
⇓
⇓
Yes
⇒
•
Alter the operating conditions, the pipe run,
or adjust the rating of the drive, motor and
pump to suit new operating conditions.
Has leakage been detected in plant ?
No
⇓
⇓
Yes
⇒
•
Renew or seal the leaking parts.
Содержание 25411801001/A5684
Страница 18: ...25411801000 ...
Страница 19: ...25411801000 ...
Страница 28: ...Slurry Pump WH14AAAAAA0EN_04D DOC JAN 04 W08 Control system 1 1 5 CONTROL SYSTEM NOT APPLICABLE ...
Страница 76: ...Slurry Pump WH24AAAAAA0EN_03B DOC JAN 04 W08 Spare parts 1 1 10 4 Spare part drawing ...
Страница 77: ...Slurry Pump WH24AM1W010XX_02E DOC JAN 04 W08 Spare parts 1 1 W3 W2 W4 W1 W6 F3 F4 F1 F2 W17 W19 W20 W21 W18 ...
Страница 84: ...Slurry Pump WH26MM1AAA0EN_03C DOC JAN 04 W08 Appendices 3 2 11 2 Reference publications ...